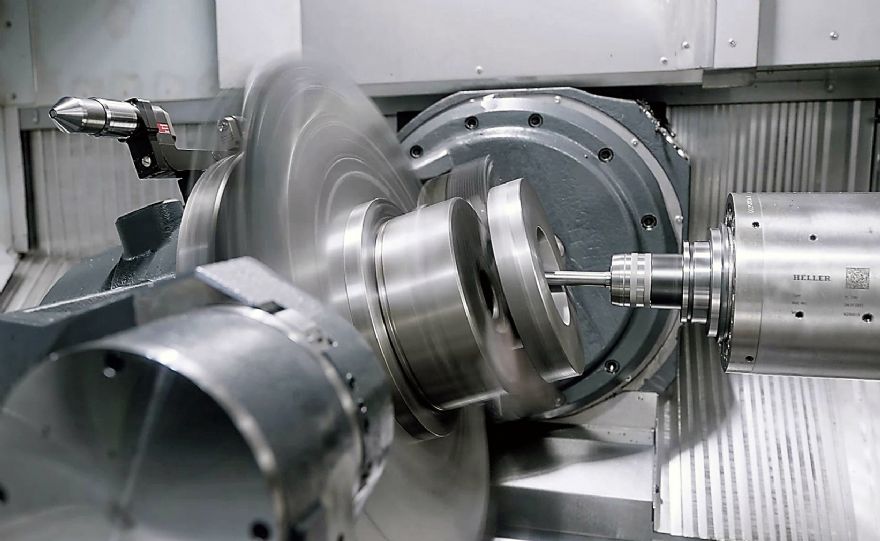
Horizontal-spindle machining centre manufacturer
Heller Maschinenfabrik GmbH recently held an in-house event at its headquarters in Nürtingen, Germany, which took place from 3-5 May, and attracted around 850 visitors. It focused on the company’s latest generations of four-axis and five-axis machining centres and presented innovative technologies such as power skiving and friction stir welding, along with future-proofed digitalisation and automation solutions.
Reinhold Groß, the company’s new CEO, said: “It was my first Heller in-house exhibition. Our subsidiaries GSN, Paatz, STS and Wenzler as well as more than 20 partners and suppliers also presented their solutions.
“A total of six different guided tours provided insights into our networked manufacturing and assembly of machining centres, spindle manufacture, component repair, and our modern training factory for machine tool engineers of tomorrow.”
Second-generation HF 3500/5500 five-axis machining centres were also on display, with emphasis on their greater flexibility, productivity and precision. Meanwhile, there was a spotlight on the fourth generation of the H 4000/6000 four-axis machining centres that once again demonstrated their dynamics, stability and high performance. A CP 6000 five-axis mill/turn machining centre showed powerful complete machining on a single platform.
For the first time, Heller presented friction stir welding technology — the process for bonding different workpieces was integrated into its four- and five-axis machining centres. The joining process enables complete machining and welding in a single set up, offering advantages in terms of productivity and precision.
Two methods for manufacturing gears on five-axis machining centres were presented. Production of different external and internal gear teeth by power skiving on a standard machine with turning functionality was demonstrated, as was hobbing of external gears. Software and a programming interface for both processes can be retrofitted.
In addition to conventional mill-turn functionality for complete machining, the Nürtingen-based machine tool manufacturer showed an alternative option – interpolation turning. New software has been developed by Siemens, for which Heller provided exclusive support.
The flexible system is an attractive alternative for users who rarely need to produce rotational features on a machining centre. The two turning options are complemented by Heller's U-axis facing and boring head that can be integrated into its spindle heads.
Automation for maximum system availabilityHeller automation solutions ensure maximum machine availability and are flexible as well as easy and intuitive to operate. Visitors to the Open House were able to see the HF 3500 with RSP rotary pallet magazine from STS for automated handling of machine pallets. Additionally, an FPC pallet container from Fastems and a robotic workpiece loading solution from STS on an HF 5500 with flexible workpiece handling were demonstrated. Heller also highlighted automated tool loading and unloading with a Kuka KMR Cybertech on an HF 3500.
The Open House also made a point of promoting digital solutions. The machine tool manufacturer presented its mobile ‘Shopfloor Interface’, which provides a holistic view of all data relevant to an assembly process. The Services Interface ensures increased transparency at the machine, higher productivity and a reduction in unscheduled downtime. A range of modules were on display, including for collision protection and tool magazine optimisation.
The benefits of the Heller Academy were also highlighted. It provides customers with targeted and effective support in the form of practical, customer-specific training courses throughout the lifetime of a machine. The training areas and equipment were available to view and financing and leasing offers were explained, as well as flexible usage models and the new ‘myHELLER’ customer portal that helps keep track of machines on the shopfloor and place orders and service requests easily.
A further announcement was that from autumn this year, it will be possible to coat the internal surfaces of small cylinders in engine blocks, as Heller will be launching a system called CBC 10 equipped with new technology based on single electric-arc wire spraying. It will be the smaller sibling of the CBC 200 thermal coating system based on twin-wire technology, which has been established for more than 10 years.
The aim of this development is to make the coating process used for two- to three-litre engines available for the production of smaller engines up to 125cc. Engines manufactured with this technology are much more environmentally friendly, as it not only reduces friction and wear but also fuel consumption and emissions.