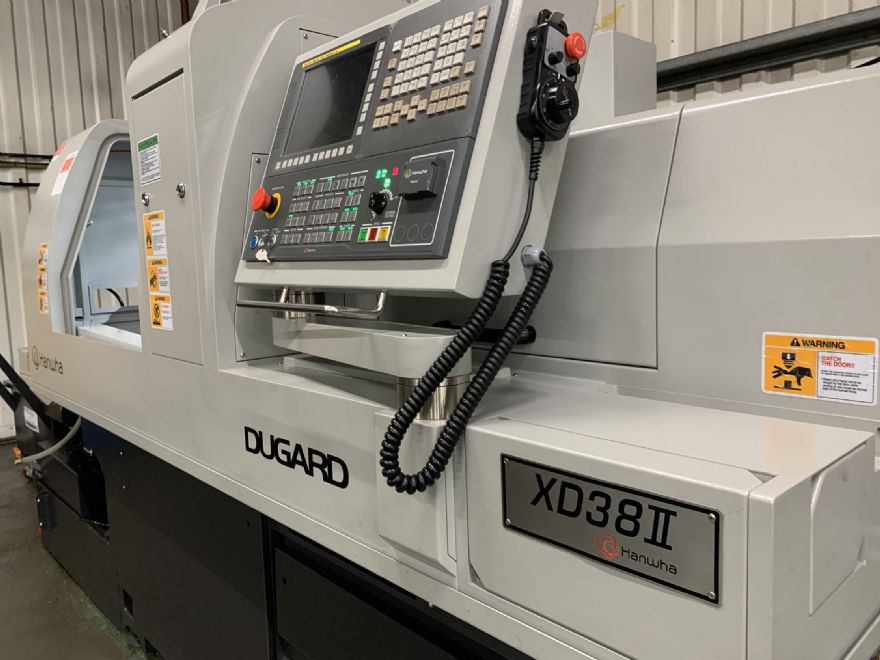
As a Tier One automotive supplier as well as a manufacturer for the fastener, electrical, food and pharmaceutical industries, the Rugby-based sub-contract machinist
Arturn Precision Engineering Ltd is no stranger to high-volume production runs; and with much of the company’s work in the diameter range 32-38mm, investing in a 38mm-capacity Hanwha XD38II sliding-head turning centre to increase its capacity and capabilities was ‘a logical choice’.
Asked why he selected this machine from Hove-based
C Dugard Ltd, Arturn Engineering’s Myles Rudkin said: “Where the tools are located, particularly the power tools, provides easy access for changing cutting tools and speeds up our setting processes. I also appreciate the Fanuc 32i-Model B CNC system and its programming, because a lot of the M-Codes are like on a fixed-head machine and already familiar to me. This means that my knowledge of fixed-head machines and their respective G and M-codes will transfer directly to the Hanwha machine.
“Furthermore, there are a large number of coolant hoses on the machine, and these can be moved and directed at specific tools, helping reduce wear and prolong tool life. We also have an LNS mist extraction system on the machine to eliminate coolant mist from the work envelope before we open the door, and an LNS Alpha 342 bar-feeding system; during a machining run it tells you exactly how many bars you have left and how many components remain to be produced. We do a lot of mid- to high-volume work — from 500 to 50,000-plus — and this helps.
As an operator, I know exactly when I will need to get more bar and how much I will need to keep the machine running. This also helps with scheduling.
“We do a wide variety of work on the new Hanwha, with materials ranging from EN18 alloy steel and mild steel to 316 stainless steel — and more. The machine also offers high power and rigidity. With one particular component that requires a large bore and two flats milled on the OD, the Hanwha has taken out two operations compared to our previous method, allowing this part to go straight to the customer as a finished item, giving us a massive saving.”