SigmaNEST, a leading innovator in CAD/CAM and business software for the fabrication industry, part of
Sandvik, has released version 23 of its software suite which delivers new nesting strategies for real-world manufacturing that optimise part processing and workflow efficiency beyond classic nesting for material. Workflow optimisation and expanded control are central themes of the new software suite. Also, three new ‘Connected Shop’ Apps assist shopfloor management.
Vice president Kevin Ramirez said: “While the goal is to optimise all available manufacturing resources, the emphasis on real-world nesting based on operational processes has shown extraordinary value in compounding efficiency beyond material savings alone. We look forward to expanding a holistic view of the manufacturing workflow based on market-driven data collected in our collaboration with our Sandvik peers.”
Making life easier downstream has been a key focus of version 23 with several strategies for pushing the workflow for assemblies or secondary operations and uncluttering the shopfloor. For example, best sheet with mixed grouping keeps parts of similar material together for those who program several days of work at once, or those who load sheets manually. Additionally, an enhanced ‘Array Function’ allows users to dynamically drag the variety of parts for a required quantity of kits, assemblies, or fixed part configuration.
In a step toward simplifying the way to the best nesting results, several nesting features are now built in for HD Trueshape and HD Advanced Trueshape users, who will gain full access to stack nesting, multi-torch nesting for large parts, dynamic X and Y clearance, as well as improvements to common line nesting. Bump nesting updates include the ability to retain a boundary and avoid nesting within destructed notch areas, tool-dependent bump boundaries, part rotation based on tooling, and common cut line bumping.
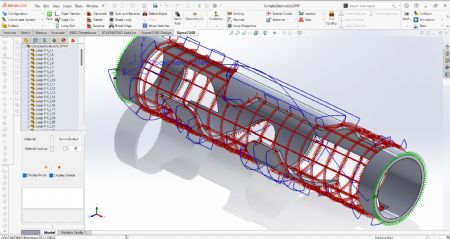
For the best in efficiency and quality, the brand new ‘Relax Nest’ feature can spread parts out on the cropped area of a completed nest to create a stronger skeleton, reducing the risk of part tipping and part distortion from excess heat.
Furthermore, several user-experience enhancements allow users to optimise the process workflow as they profile cut rather than forcing them to start over to add the options for the nest, such as removal of pre-piercing operations, crop cut side selection, apply scrap cut preferences, or apply proven company standard defaults. There is also support for additional fly cut patterns and taper correction for 3-D bevel and waterjet machines that adjust the tilt of the machine head during straight and bevel cuts.
Version 23 also has some powerful tools to boost the productivity of the punch programmer, including: ‘Interactive Nesting’ for punch, automates bump boundaries for each tool, improving the speed and precision of part placement; ‘Punch Patterns’ allow for multiple contours; and ‘Single-click Loading’ to the turret of tools, including entire pattern tool groups, can be done using a new ‘Quick Drop’ feature.
Additionally, SigmaTUBE for SolidWorks expedites the programming process with the addition of automatic ‘Auto Destruct’ to eliminate time-consuming manual work. Meanwhile, the ‘Dead Zone’ nesting option supports open section profiles and single part nests, significantly increasing material yield by using previously scrapped areas of the stock. Mazak users in particular will appreciate support for ‘Auto Touch Probing’ rules which helps drive fully automated programming.
Part of the Sandvik Design and Planning Automation division, SigmaNEST empowers customers in all major industry sectors with a machine-agnostic approach, an integrated platform, and a worldwide team of experienced product experts.