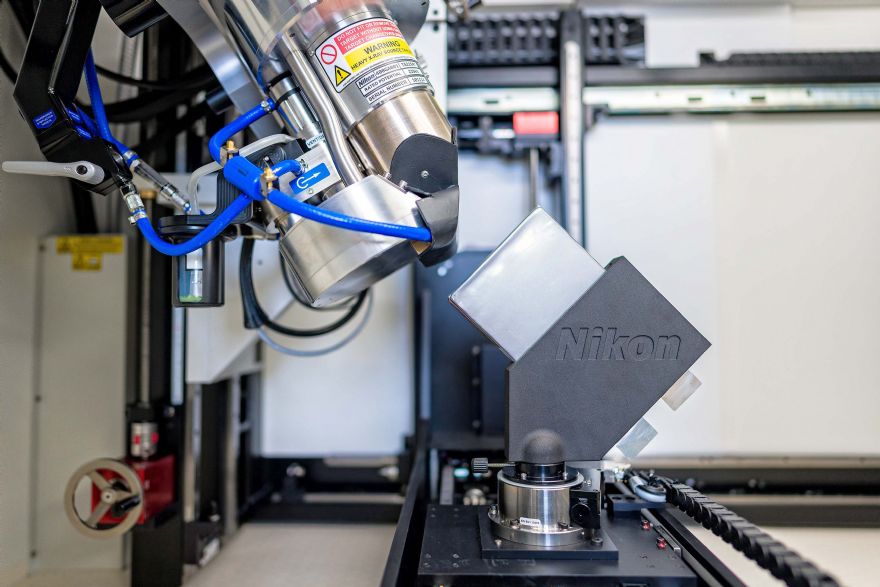
Following the introduction of LiB.Overhang Analysis software powered by artificial intelligence (AI) from the Industrial Metrology Business Unit of
Nikon Corporation, the inspection and analysis of anode overhang in lithium-ion battery (LiB) cells during their mass production can be carried out automatically, precisely and consistently by 3-D X-ray scanning and computed tomography (CT) — in a production environment where short inspection cycle times are a key require.
The software is designed to enable high production yield to meet increasing market demand for batteries while resulting in fewer warranty claims from users of electric vehicles, energy storage systems and other battery-powered equipment. The aim of LiB.Overhang Analysis is to encourage more in-line inspection earlier in the manufacturing process to improve product quality.
The anode in a LiB cell is larger than the cathode to prevent lithium plating and possible dendrite formation, so there are passive areas on the anode known as overhang regions that are not opposed by corresponding areas of cathode. They must consistently be within close limits, otherwise battery performance may be reduced — and in extreme cases a battery may spontaneously combust. It is therefore critically important to analyse anode overhang.
The problem with doing this by traditional 2-D radiography inspection is that, although fast, it does not provide results that are sufficiently precise or repeatable, particularly when X-raying cells, as the beam must be parallel with every internal sheet for a perfect image. It is extremely difficult to distinguish individual layers with a single cone-beam radiograph, especially when the sheets are not perfectly flat.
However, automating overhang analysis by 3D X-ray CT, which is relatively new to the market, eliminates these difficulties, as LiB.Overhang Analysis is fast enough to cope with the speed of production lines — and it is less sensitive to noise in 3-D images acquired by high-speed scanning.
This is because Nikon’s advanced machine learning AI model can use prior information to identify and classify anode overhang features and flaws in cells, regardless of the presence of typical noise and scan artefacts. Such data would confuse conventional methods of analysis and produce erroneous results when trying to segment the anode and cathode layers automatically.
Written in-house specifically for Nikon’s own XT H-series of X-ray CT systems, LiB.Overhang Analysis software allows battery cells to be scanned quickly, accurately, and reliably, either in-line or line-side in a factory.
The software is integrated with the customer’s X-ray CT equipment by Nikon to provide a complete solution, ensuring that the system is ready for use immediately after commissioning, with overhangs calculated automatically for each layer in the anode/cathode stack, generating not a simple pass/fail result but instead numerical measurements of critical features. The inspection data is normally stored in a manufacturing execution system database to allow full traceability of each individual cell.