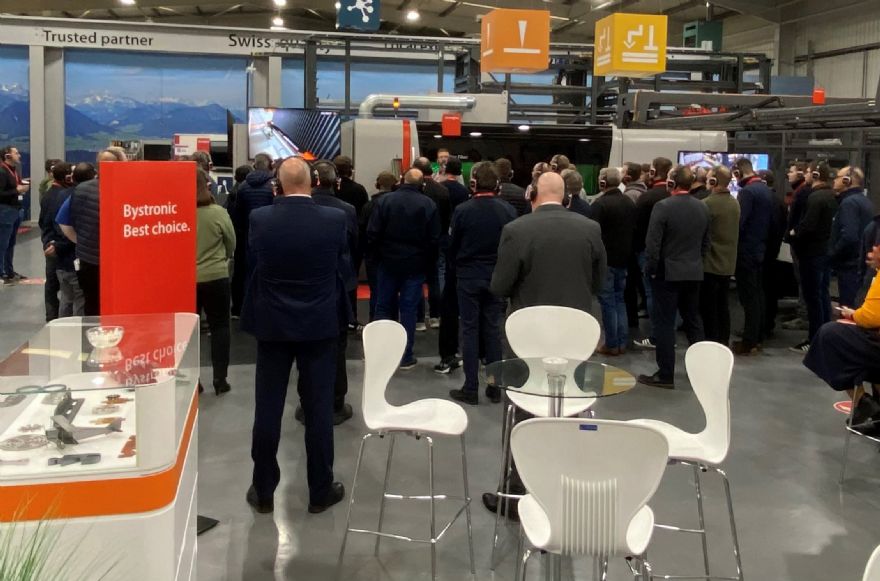
Coventry-based
Bystronic UK, a leading provider of high-quality solutions for the sheet metal and tube processing sectors, reported its busiest-ever Open House last week with 175 people from 84 companies in attendance over the three days.
Paul Cooper, Bystronic UK managing director, said: “It was fantastic to see so many people and to show off our latest innovations. It was clear from my conversations with our customers that, despite some difficult circumstances, such as high energy costs, supply chain issues and skills shortages, UK manufacturing remains buoyant and in very good health.”
Taking centre stage was the new ByStar Fiber with 20kW of laser power and an optimised cutting process that provide enhanced cutting quality and productivity. The machine was displayed with full automation. This latest laser offers reliable cutting and is suitable for a wide range of applications, thereby enabling sheet metal-processing companies to take a major step forward in terms of productivity and efficiency. Bystronic says the technological leap from the previously available 3-15kW laser output levels to the latest 20kW level is considerable and opens up new possibilities for its customers.
“Compared to a 15kW fibre laser, the productivity of the 20kW ByStar Fiber is, on average, 40% greater in mild steel and stainless steel in thicknesses from 4 to 20mm. Moreover, whether cutting aluminium, non-ferrous metals, or steel, the high-performance Bystronic cutting head excels with maximum precision in both thin and thick sheets and profiles.
“In addition, the 20kW of laser power offers extended applications in steel and aluminum up to 50mm thick. Furthermore, the optional ‘Parameter Wizard’ ensures that the correct quality of the cut parts is always selected, as the user can obtaining the perfect parameter within minutes.”
“The new power level is available for the ByStar 3015, 4020, 6225 and 8025; this latest machine is controlled by Bystronic’s ByVision Cutting software via a 21.5in touch-screen, which makes ‘operating the machine as simple as using a smartphone’.”
Unmanned operationA wide range of automation solutions have been designed to ensure maximum machine utilisation and process reliability, even during unmanned operation. These include loading and unloading systems, sorting solutions, and individually customisable storage systems.
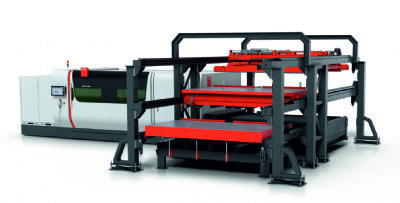
Bystronic added: “These make it possible to create an automated laser cutting process that is seamlessly integrated and adapted to the existing production environment and the available space.”
Also on display was the BySmart Fiber laser cutting system which is available with new laser output levels of 8 or 10kW on the BySmart Fiber 3015 and the BySmart Fiber 4020. Thanks to the increased power, users can now cut sheet metal even faster and with even higher precision. Depending on the production spectrum and customer requirements, the BySmart Fiber is available with laser outputs of 3, 4, 6, 8, 10 and 12kW (in addition, the BySmart Fiber 3015 is also available with 2kW).
Customers can cut 3 to 15mm mild steel, stainless steel and aluminum on average 15% faster than with a 10kW fiber laser. This fast speed is supported by the high-performance Bystronic Cutting Head V2, which provides an even more continuous cutting process. No matter, if thin or thick material, non-ferrous metal or steel — the ByStar Fiber is able to cut them all.
What is more, users achieve particularly high-quality cuts in material thicknesses up to 30mm and it opens up new possibilities for cutting jobs in thick materials where the finish of the cut parts is critical.
For many users, automated laser cutting is a decisive success factor. Automation solutions for fiber laser cutting offer a key advantage: They increase the capacity utilisation of the laser cutting system and reduce the user’s workload with regard to the time-consuming material handling. Both these factors mean that cutting jobs are performed faster and at reduced cost.
Bystronic offers the Byloader, ByTrans, ByTrans Extended, and ByTrans Modular loading and unloading solutions as well as the BySort parts sorting system in both the 3015 and 4020 formats. In addition, third-party automation solutions can also be integrated. Depending on the order situation, the Bystronic systems organise the material flow fully and semi-automatically while also offering sufficient flexibility to process smaller orders manually whenever required.
Also highlighted were the compact ByBend Star 40 and ByBend Star 80 mobile press brakes which have been redesigned with and a new drive system that ensures energy-efficient and dynamic bending processes.
For many users, bending still means producing small to medium-size parts on press brakes that are too large. This limits them, because processing bending parts on presses that are too large costs time, space and sometimes impacts on quality. For parts of up to about 1,500mm bending length and a maximum thickness of 20mm, these users do not need a large-scale bending station, but rather a small and versatile press brake.
Bending in the tightest of spacesThe new ByBend Star 40 and 80 were developed precisely for such requirements – compact, fast press brakes that fit into almost any production environment. The mobility of the two ByBend Star press brakes is a significant advantage over large-format press brakes. while large presses must be placed in a fixed position in the factory and often take up a lot of space due to their design, the new ByBend Star 40 and 80, the smallest ones from Bystronic bend as reliably but in the tightest of spaces.
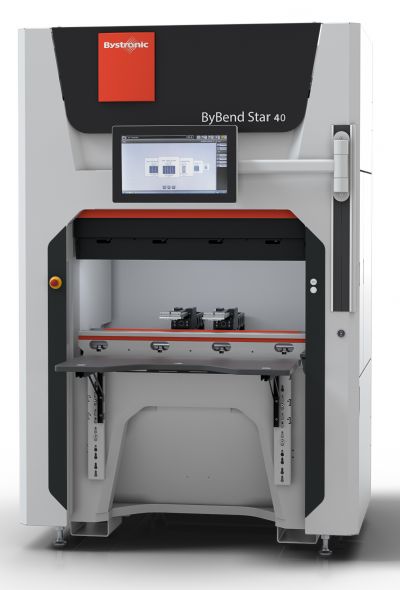
As a result Bystronic offers an ideal bending solution for production landscapes that are subject to constant change. The ByBend Star 40 and 80 support users in flexible contract production with fluctuating batch sizes and highly varying bending parts as well as in series production with recurring parts. For this purpose, the machines can, for example, stand next to a laser cutting machine today and be used tomorrow lined up with other press brakes for series production.
The new servo-hydraulics enable bending speeds of up to 30mm/s. This makes the ByBend Star 40 and ByBend Star 80 three-times faster than a large press brake.
Compared to the ByBend Star 40, the ByBend Star 80 offers more bending length and more pressing power, making it suitable for a wider range of applications. On a bending length of around 1.5m the ByBend Star 80 develops a pressing force of 80 tonnes and the footprint of the machine is less than 6m
2.
On the ByBend Star 40 and 80, the ByMotion drive control developed by Bystronic ensures the precise acceleration of the upper beam and back gauge. This results in a perfect interplay of speed, precision, and bending force. The result is bending processes with the highest repeatability.
The economical drive concept “Dynamic Drive System” allows dynamic bending sequences without energy loss. The ByBend Star 40 and 80 supply the exact force required for each bent part. Added to this are intelligent functions such as the energy saver and an automatic start-stop function. Compared to large models, the two ByBend Star press brakes offer almost unbeatable energy efficiency throughout the entire bending process.
Meanwhile, the ByBend Smart press brake offers innovative bending technology and numerous new functions at an affordable price. From the outset, Bystronic designed this press brake to offer a performance package with intelligent functions that enable users to produce high-quality parts at low cost.
The new press brake is at least 30% faster than its predecessor, the Xact Smart – and even 50% faster with the new ‘Efficiency Booster’ option. This makes it the ideal machine for all those sheet metal processing companies for which time is a crucial factor in the day-to-day competition for orders.
One of the ByBend Smart’s flexibility-enhancing features is the daylight and stroke length expansion. This upgrade, which is available with the purchase of a new machine, extends the daylight for bending tools from 480 to 580mm. The additional 100mm boost the ByBend Smart’s flexibility by as much as 30% because this means that it can use taller tools can be used, which enables users to produce parts with lower bending edges. This is particularly useful when bending boxes and drawers.
The ByBend Smart can also be equipped with a five-axis back gauge; The fifth-axis movement assists with sheet metal products where the bending edges are not just parallel, but are tapered. Similar to the expansion of the daylight opening and stroke length, the various backgauge systems represent an option to increase the bending versatility. The basic version of the ByBend Smart comes with a two-axis back gauge system.