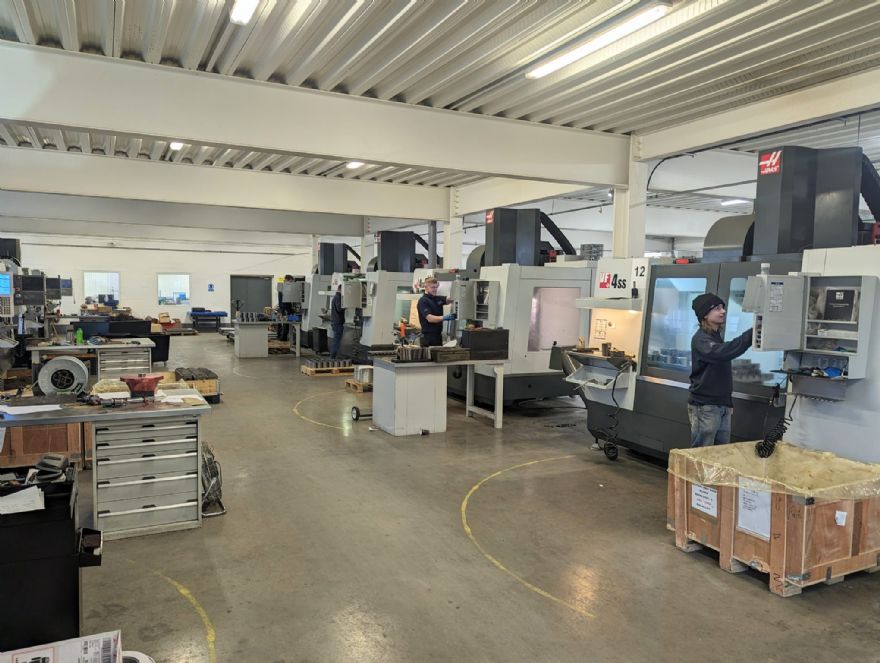
Wythenshawe-based
Howells Railway Products Ltd, founded in 1946 as a radio and TV repair shop, has come along way down the track since those early days, having grown into one of the largest producers of coils and transformers in Manchester. The manufacturer entered the rail industry in the 1960s when power supplies for railway signalling moved away from traditional mechanical operation.
This evolution led to the introduction of other electrical and electro-mechanical equipment and in 1992, the Howells Group plc was formed with the creation of the Howells Railway Products Ltd subsidiary. 30 years on, the company has expanded rapidly and now includes the likes of Siemens, Network Rail, Alstom, Transport for London, Bombardier and Babcock Rail among its customers.
To work at the cutting edge of technology with industry leaders, Howells Railway Products has added a new 40,000ft
2 CNC machine shop with 26 Haas machine tools and cutting tools supplied by
Industrial Tooling Corporation Ltd (ITC).
The rail specialist now manufactures everything from transformers and rectifiers, impedance bonds, tubular stretcher bars, disconnection boxes, AWS magnets, railway signals and overhead lines. To efficiently machine such a diverse range of products in varying quantities, Howells Railway has worked with ITC since 2018.
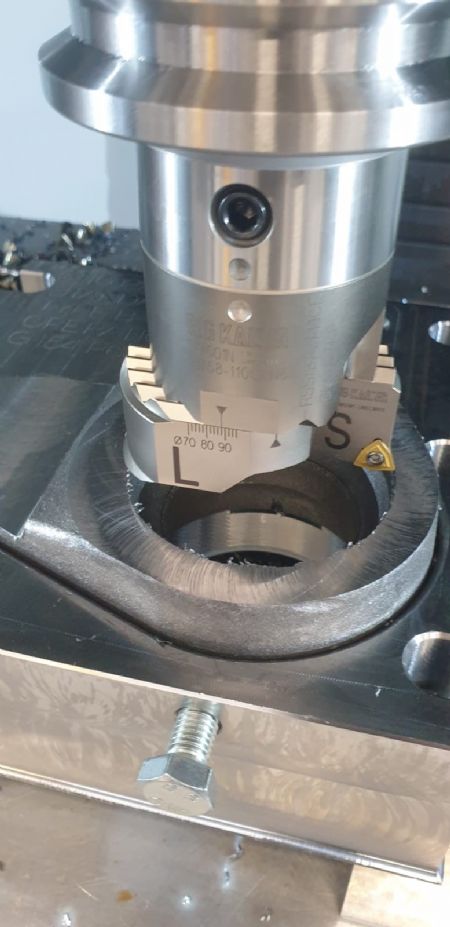
Initially having issues with tool life and performance in some of its processes, a relationship with ITC was formed and the cutting tool specialist instantly made an impact. ITC introduced its solid-carbide end mills and drills to deliver tool life improvements and cost benefits across a wide range of applications. This was then increased to turning products which again offered a competitive alternative to the existing tools being used on site.
From this early success, ITC’s Gary Murrey then introduced the Widia line of indexable cutting tools with modular drills and high-feed shell mills being trialled on CLA3 alloy steel castings. The end bracket components for rail stretcher bars were manufactured in volumes up to 200 per month with four parts set up on three different Haas machining centres.
Presenting the 50mm diameter Widia VXF09 high-feed milling system with five inserts in a ‘like-for-like’ trial, the Widia cutter managed to process 11 sets of four parts (44 parts in total). The ability to machine 44 parts with a single edge of the four-sided insert was a vast improvement upon the 28 parts the previous supplier could achieve between insert failure – resulting in a reduction in insert costs. In September, Howells Railway informed ITC that they were moving the same parts and set up from three BT40 taper three-axis Haas machines to one larger Haas VF11 BT50 taper machine with a 3m bed.
Justin Johnson, Howells Railway machine shop manager, said: “The end brackets were being produced in batches of four on three different machining centres. Each machine was dedicated to each of the three different operations. This was tying up three machines and two machinists, so we moved everything to the larger Haas VF11. This enabled us to set up 12 parts on the machine bed simultaneously and machine each of the three operations in one hit.”
This transition to a more robust BT50 taper machine provided ITC’s Gary Murrey with an opportunity to re-assess each of the three operations from a tooling perspective. One of the first changes was the introduction of the Widia M8065HD face mill for removing excess stock from the castings. With a more robust set up, ITC supplied a 63mm diameter cutter to remove 6mm of stock in a single pass from the facing and shoulder process. With the previous high-feed face mill removing material at a rate of 1mm per pass, the M8065HD significantly improved the cycle time on the parts and provided a more stable process.
Always looking to take productivity gains to the next level, Mr Murrey introduced the benefits of the BIG Kaiser system to the end bracket components. The end brackets also require an 88.1mm bore at a depth of 65mm as part of op1. Prior to the process review by the ITC team, the bore was processed with a high-feed 50mm diameter indexable shell mill helical interpolating inside the bore – a process that took 3in 30secv.
Fantastic surface finishMr Murrey said: “After looking at the options available, we highlighted the BIG Kaiser boring system and discussed changing the process from helical interpolation to a plunging application. The BIG Kaiser Twin Bore tooling system (SW Rough Boring Head) was selected by my colleague Simon Yeomans, our resident BIG Kaiser expert. We run the Twin Bore head at 542rev/min with an 81mm/min feed rate. It worked extremely well, left a fantastic surface finish in the bore and it reduced the whole cycle time by 11min 20sec or 2min 50sec per part.”
Alluding to the benefits of this first BIG Kaiser tool, Mr Johnson continued: “By changing to the BIG Kaiser system on the bore, we found a less aggressive method that improved surface finishes and reduced the stress on our machine. However, the major benefits were the cycle-time reduction of almost 12min for each batch of 12 parts and the tooling cost saving.
“We were using a high feed shell mill with five inserts that needed an edge change every 20 parts. In comparison, the BIG Kaiser boring tool only has two inserts, and they only need to be changed after machining 100 parts. Not only has this made a huge tooling cost reduction, but we now only need to change the inserts once every shift as opposed to three or four times a shift with the high-feed shell mill.”
Adding his thoughts, Alex Barnes, the CNC programmer at Howells Railway who was instrumental in the process changes, said: “As a team, we worked closely with ITC to move the components to the larger Haas VF11, which has revolutionised the process. Working with ITC, we instigated new tooling concepts and reprogrammed the parts to significantly improve cycle times and increase throughput.”
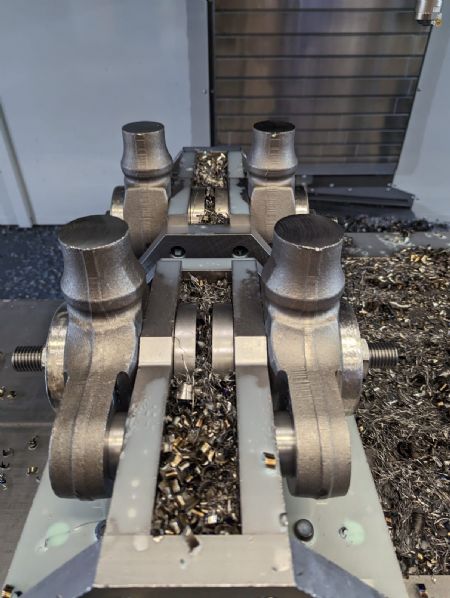
Regarded as the world's leading provider of hole boring technology, the diversity of the BIG Kaiser range also enabled the ITC team to investigate potential improvements on the third operation of the end bracket parts at Howells Railway. Within the 12 cast parts simultaneously set up on the Haas VF11, there are four components set vertically, which use a 16-insert porcupine cutter to interpolate around a 44.9mm diameter spigot. At its biggest diameter, the process removes 7.5mm of stock to a depth of 40mm.
Using the previous porcupine tool, the four spigots were machined in a cycle time of 6min with significant noise and vibration throughout the process. Switching to the BIG Kaiser SW twin-head overturning tool, the ITC engineers ran the new tool with just two inserts and cutting data of 800rev/min and 290mm/min feed.
The result was a cycle time reduction of 5min 10sec, slashing the cycle time to just 50sec for the four parts. The process took 10sec to machine each spigot with 10sec traversing between the components. At the widest point of the forging, the tool is removing 7.5mm of stock material in a single pass, improving surface finishes, and tool life performance and also reducing chatter and vibration to minimise spindle load.
Mr Johnson continued: “It is too early to calculate the reduction in tooling costs by transitioning to the VF11 and applying the BIG Kaiser tools, but we know it is significant. As an overall process, bringing all three operations to a single machine has yielded time, labour and capacity savings. What we didn’t envisage by undertaking this process is the potential benefits of changing from a BT40 machine to a BT50 from a tooling perspective.
“The increased machine stability has allowed us to completely change the process. As a top-line figure, we know we have decreased our cycle time for 12 parts from 1hr 38min to 50min. Machining over 200 parts a week on an ongoing basis, is a huge saving to our business.”
He concluded: “However, the benefits are much further reaching. With fewer insert changes and tool changeovers, reduced impact upon our machine spindles and the fact that we are using fewer machines – the project has been a complete success. As one of our key cutting tool suppliers, ITC always provides exceptional service and rather than resting on his laurels, Gary always strives to deliver continuous improvement for our business.”