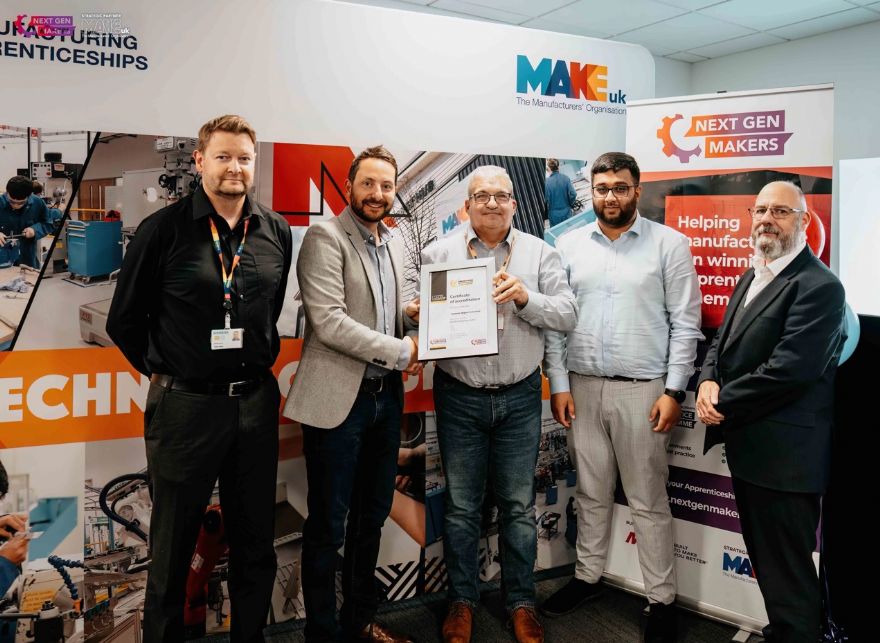
Continuous improvement is not a new concept within manufacturing and engineering, but applying it to an apprenticeship scheme as part of benchmarking and best practice sharing is. However, engineering companies from around the UK have recently been revealing their views on how benchmarking has positively impacted their apprenticeship schemes and made them more attractive to employers.
The companies are part of the
Next Gen Makers Engineering Apprenticeships: Best Practice Programme, a large online community of UK engineering and manufacturing firms committed to achieving excellence in how they attract, develop, and retain young engineering talent through best practice sharing, while working to achieve best practice benchmarks.
They are also the latest to receive the
Make UK Engineering Apprenticeships: Employer Kitemark accreditation as part of the programme, with LISI Aerospace, Renishaw, Petford Group, Kirkstall Precision Engineering, Siemens Digital Industries, SMC and Whale Tankers receiving the Kitemark for the first time this month – and Thomas Dudley Ltd, KUKA, Weir Minerals, Wienerberger UK, Fablink Group, Eminox and Ishida successfully retaining their accreditation.
The Make UK
Engineering Apprenticeships: Employer Kitemark Accreditation recognises exemplar employers of engineering apprentices – companies that have undergone a 12-month accreditation process that includes satisfaction surveys of existing engineering apprentices and benchmarking of the company’s apprenticeship scheme against industry best practices. It is quickly becoming a badge of honour for companies that ‘go the extra mile’ in creating a great apprentice experience for the engineers of the future. Companies are recognised with either the Gold standard ‘Excellent Employer Kitemark’ status, or the Silver standard ‘Aspiring for Excellence’ status – helping them to differentiate and stand out as attractive employers for potential engineering apprentices moving forward.
Mark Capell, Rugby-based
LISI Aerospace general manager, said: “We have been working with apprentices for many years, but in the early days it was quite ad hoc and hit and miss in the results. The benefit of bechmarking is that we can share best practice, determine whether our ideas are actually good and we can really maximise the potential of our scheme. Since being involved in the ‘Best Practice Programme’, I can safely say our apprenticeship scheme has improved, it has evolved and stabilised, we are far more successful at finding and retaining young talent as a result. Having the Kitemark really demonstrates to local schools, colleges and students that we have a quality scheme and are a great choice for them.”
Iqbal Bahia, managing director of Leeds-based
Kirkstall Precision Engineering, said: “For us benchmarking drew a line in the sand and highlighted where we were at. If you can’t measure something you can’t improve it, so to have that measure enabled us to identify where we can improve it. That made us be more focused internally on what we were doing, and also focused on what the college were doing for us too. The feedback from the independent survey of our existing apprentices was absolutely fantastic, it highlighted where we were strong and also gave us focus to improve. We know that there is a recruitment shortage in the market and for us to recruit the best apprentices we need to show them that we are committed. Having the Kitemark shows potential apprentices that Kirkstall Precision is an organisation that takes apprentice training seriously.”
Companies can join the
Engineering Apprenticeships: Best Practice Programme at any time to benchmark, learn and improve their apprenticeship scheme. When they feel that they are ready, those that meet the qualifying criteria of having at least three current engineering apprentices can then opt in to one of four annual accreditation cycles — January, April, July and October. All companies are re-accredited each year to retain the Kitemark or improve their achieved Kitemark level.