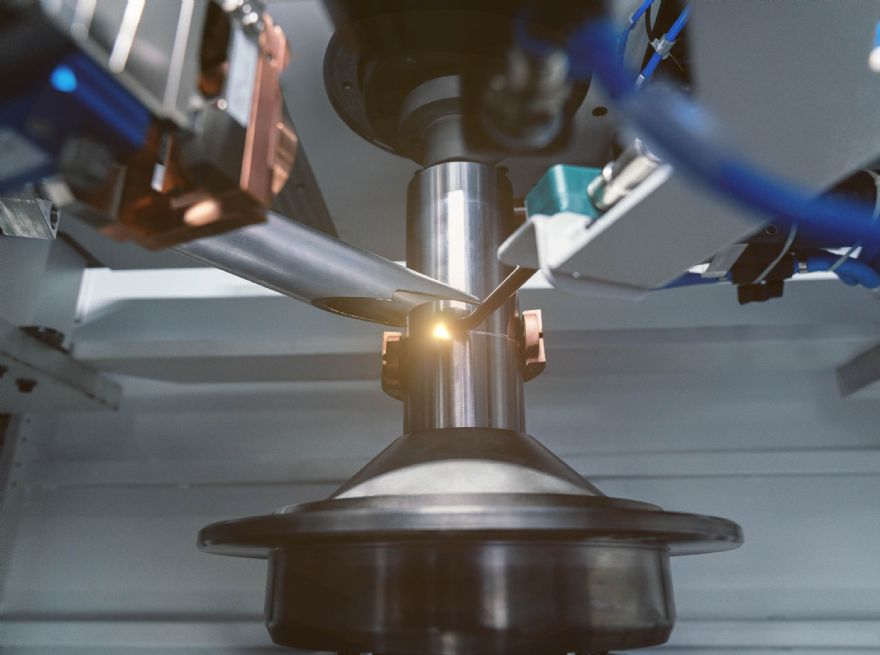
Sales of electric vehicles (EVs) are rising rapidly worldwide and the International Energy Agency (IEA) estimates that 14 million will be sold this year, representing a 35% increase in sales compared with 2022.
As a result, production planners are focusing on the manufacture of key components of the electric motor, such as the rotor shaft, and are looking for innovative solutions ‘from a single source’ that allow these to be machined efficiently and reliably in ever larger quantities. To meet the anticipated demand,
Emag LaserTec GmbH — based in Heubach, near Aalen (Germany) — is offering its ELC 6 laser welding machine, which combines joining, preheating, and welding processes on a ‘rotor shaft assembly’.
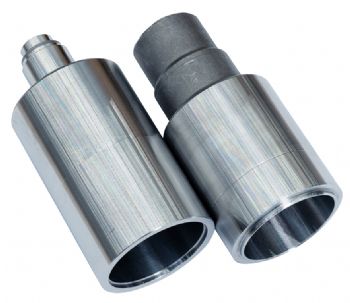
Emag says advances in e-mobility, including hollow designs for rotor shafts, allow great freedom in design, while lightening their weight and lowering material costs. “At the same time, this ‘heart’ of the electric motor has to withstand particularly high loads, as motor speeds of up to 20,000rev/min are now possible, a speed that is considerably higher than the camshaft in a combustion engine, for example. This means the production of assembled rotor shafts is always about manufacturing tolerance, with even minimal imbalances having to be avoided at all costs.
“The ELC 6 machine offers a highly efficient solution for joining the two halves of the rotor shaft, with part handling, preheating, and joining as well as welding taking place in quick succession and perfectly timed by the machine’s rotary table, while the precisely metered, concentrated energy of the laser beam allows high welding speeds with minimal distortion on the welded component.
“The processes undertaken by the machine, which was specially developed for powertrain components with circumferential welds, comprise: laser cleaning of the individual parts before being loaded into the ELC 6; preheating and joining of the two parts; checking the weld seam position and adjusting it as necessary (the contour is scanned and the data communicated to the welding optics and the NC axes); and welding of the vertical assembly, which rotates while the laser optics only move radially towards the workpiece. After welding, the component is transported out of the machine by a swiveling motion of the rotary table and unloaded by a robot.”