Interroll vertical crossbelt sorterDerbyshire-based
Conveyor Systems Ltd (CSL), a leading materials-handling solutions provider, has helped a leading e-commerce customer to upgrade its packing and sortation system to meet increasing levels of online consumer demand. CSL designed and installed a ‘start of the art’, multi-stage, high-speed crossbelt system which has enabled the company to sort and pack over 180,000 orders a day. The customer, which is based in the North West of England, processes online orders at a staggering rate of 7,500 items per hour. The project involved handling a very diverse range of products such as cartons, cardboard envelopes, polybags and jiffy bags. All of these items were to be processed by 120 operators on a 24-hr shift basis so all upgrades had to be completed without fault and with minimal downtime.
Previously, the client faced challenges due to the extensive use of manual labour for packing and sorting items for shipment. This approach often resulted in delays to dispatching items or, even worse, occasional damage to products. After consulting with multiple solutions providers, the customer selected CSL as its preferred supplier. CSL understood that an advanced packing and sorting system needed to effectively use floor space while ensuring the speedy, secure delivery of products along this packing line. Additionally, the customer needed to be able to track and monitor the position of goods along the sortation line to make sure that all packages were delivered to the correct final destination.
To meet this challenge CSL worked with its customer to design a sortation system that featured eight product packing lanes, each outfitted with 15 packing benches. Packed products from each of these lanes were then transferred onto the main transit line using multi-speed metering belts and mitre belt merges. The main transit line weaved its way through the building, taking a 90-degree turn before ascending to a height in excess of 2,500mm. This arrangement allowed for operator movement beneath the system, maximising the efficiency of the flow of people and products.
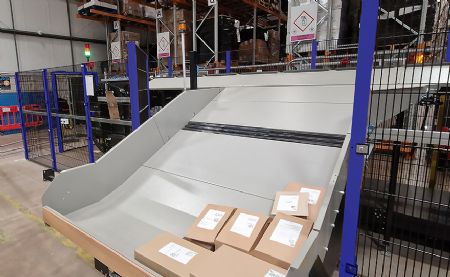
Upon reaching the higher level, each product underwent scanning through a Sick scanner array. The relevant information was relayed to and from a cloud-based server, providing CSL with a precise destination lane for each item. The packages were subsequently indexed via a multi-stage belt system onto a high-speed vertical cross belt sorter. This sorter housed 44 destination chutes, including a run-out chute for barcode misreads and orders requiring special attention.
Using the sorter’s control system, the customer could assign a specific sort location to a dedicated chute. Each chute was fitted with an indicator beacon, which notified the operator about the chute’s status. If a chute reached 75% or even 100% capacity, the system could automatically redirect packages to a previously selected destination. Other upgrades included adding two desktop PCs with Scada operator interfaces which allowed for remote, real-time system operation and the installation of two bespoke access platforms to maintain operator access to the main fire exits.
CSL managing director Mike Graham said: “We are overjoyed with the results we were able to achieve for our valued e-commerce customer. The installation, testing, and commissioning of the entire system showed CSL’s commitment to operational efficiency and customer satisfaction as we were able to complete the project within a 19-week period and worked with our customer to ensure a seamless changeover to the new packaging and sorting system.”