
Switzerland-based
Fritz Studer AG while internationally renowned for its high-end cylindrical grinding machines, still offers the same uncompromising quality and precision with its growing entry-level ranges. Sandro Bottazzo, CSO of Fritz Studer AG (pictured above), said: “We are continuously expanding our entry-level range for customers who appreciate Studer quality and utmost precision but do not need all the features offered with the premium machines.” The entry-level machine ranges currently include the favorit, favoritCNC, and S100 models.
The favorit is a CNC universal cylindrical grinding machine ideal for the individual and batch production of short to long-size workpieces. Distances between centres available are 400, 650, 1,000 and 1,600mm, all with a centre height of 175mm. It can grind workpieces with a maximum weight of 150kg and external or internal grinding are possible in one setup.
The favoritCNC is an entry-level CNC cylindrical grinding machine that is suitable for universal use and it features distances between centres of 650 or 1,000mm and a centre height of 175mm. It can grind workpieces with a maximum weight of 80 or 120kg and both external and internal grinding are possible in one set up.
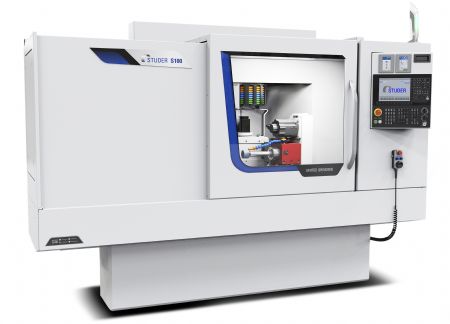
Completing the line-up is the S100 (pictured left), an entry-level CNC universal internal cylindrical grinding machine that is ideal a wide range of internal, face, and external grinding applications. It has a workpiece length (including clamping device) of 550mm and maximum workpiece dia of 420mm. It offers an external grinding dia of 420mm and a maximum internal grinding length of 200mm.
Studer’s CTO Daniel Huber said: “Compared to our high-end models, the number of tools and range of spindle power is limited, and many technical processes and interfaces standardised – but this allows them to cover a wide range of grinding applications while providing excellent value for money.”
Depending on the model, optional accessories and adaptations are also possible. Studer thus has the right machine for any application. Mr Bottazzo continued: “Our sales staff and representatives are familiar with the specifications of each machine and can accordingly offer the suitable model with the optimal configuration.”
Another unique feature that all Studer entry-level machines have in common is very short delivery times. The machines are assembled on a unique specially designed, high-precision conveyor system (flow assembly+). Customers benefit from the shortest throughput times and high manufacturing quality. Discussing the purchase of a Studer favorit, Okyay Erik, general manager of the Turkish automotive supplier Celikis, said: “We were surprised by what our Studer favorit can achieve, even though it is classified as an entry-level machine.” The company based in Izmir produces various products including differential gears, shafts, and housings for major automobile manufacturers.
He continued: “With the favorit, we have significantly increased the efficiency of our driveshaft production. Where we used to produce 15 drive shafts an hour, we can now manage 25. Plus, we no longer need to use a measuring system, as the machine’s accuracy is very high. This, in turn, reduces reset times, boosting productivity further.”
Entry-level machinesAs a CNC universal cylindrical grinding machine that is easy to program thanks to the 24in multitouch screen, the favorit can grind both short and long workpieces weighing up to 150kg — in single or series production. The cross and longitudinal slides, made of high-quality grey cast iron, ensure the highest precision. As with all Studer machines, the machine bed is made of the patented mineral casting Granitan, which ensures the best surface quality of the ground parts with its excellent damping and thermal behaviour. These are just a few examples of how customers benefit from Studer’s premium manufacturer status even in entry-level machines.
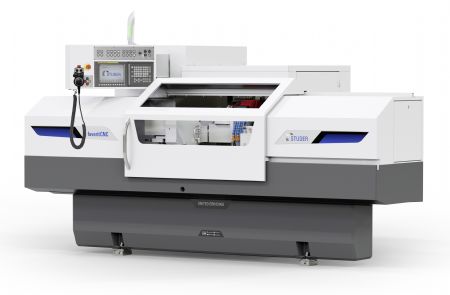
The same applies to the favoritCNC (pictured right). This CNC universal cylindrical grinding machine is the leader in terms of value for money and can be adapted to a variety of grinding tasks with different options such as a measuring system, balancing system, contact detection, and longitudinal positioning. With a distance between centres of 650 or 1,000mm, it is suitable for universal use and can handle key applications. Its high grinding precision, even at this entry-class level, is demonstrated by its high roundness accuracy of less than 0.0004mm. Thanks to the in-house StuderPictogramming grinding software, even complex grinding cycles can be executed easily, and intuitively.
Meanwhile, with the S100, there is also a specialist for internal cylindrical grinding in the entry-level portfolio, serving as the counterpart to the favoritCNC in external cylindrical grinding. It handles a wide range of internal, face, and external grinding applications with the highest accuracy and is thus the ideal universal internal cylindrical grinding machine in this segment. Its specialty is the complete machining of workpieces with a length of up to 550mm (including clamping devices) and a dia of up to 420mm. Thanks to the wheelhead with multiple grinding spindles and QuickSet for quick set up, it significantly reduces setup and re-setting costs. The S100 is also easy and quick to control, with ergonomically arranged operating elements and StuderPictogramming.
Innovative technologyShrinking and ageing populations around the world are making it increasingly difficult to replace retiring workforces who, through their years of experience, were able to achieve high quality results with manual grinding machines. Mr Huber added: “Thanks to the innovative technology, intuitive software, and simple operation of our entry-level machines, our customers’ employees can now grind workpieces of the highest quality after just a few days of training.”
Automation is also becoming increasingly important to manufacturers as it helps save time and work for operators and makes overall production more efficient. For instance, the favorit and the S100 can be equipped with a standardised loader interface, which can automatically open and close the operating door. As a result, customers can integrate the machine into their automated production processes with a robotic arm or a gantry loader.
Mr Bottazzo continued: “Besides high quality and precision, top reliability is particularly important. Our customers, particularly small and medium-size enterprises, appreciate that they can grind highly economically with our machines, while minimising downtime.” Technical standardisation not only ensures an economical price but also a low susceptibility to errors. In the event of a problem, Studer’s customer-oriented and efficient Customer Care service is quickly available to provide expert assistance.