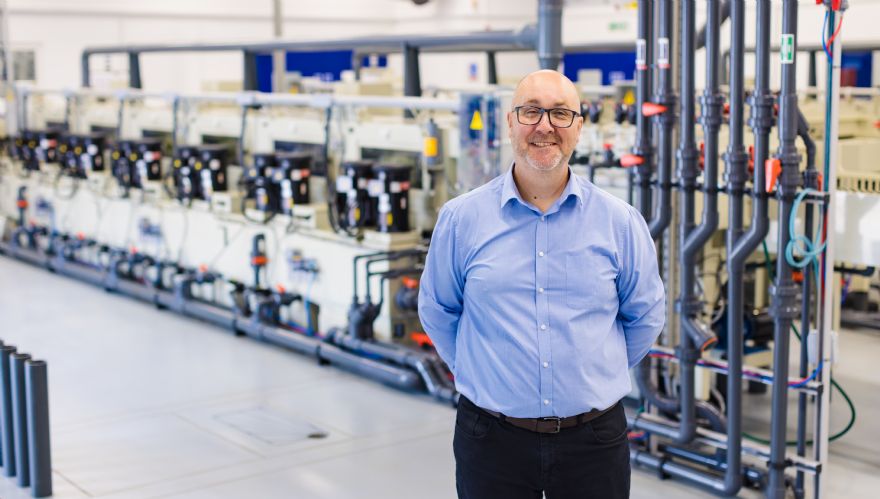
Global chemical etching supplier
Precision Micro has installed a new etching and stripping machine at its Fort Dunlop site in Birmingham, which puts the finishing touches to a second new etch room. Part of a £1.8 million investment reported last year, the business believes it is now uniquely placed to meet the increasing global demand for next-generation energy technologies such as hydrogen production and storage, carbon capture, green energy buffering, electric, and hydrogen electric vehicles (EVs).
Karl Hollis, Precision Micro’s director of engineering (pictured), said: “With carbon neutrality and ‘net zero’ a crucial agenda item for many countries and businesses around the world, there is an ever-growing appetite for complex etched components used in the production, storage, recovery and transfer of ‘green’ energy. This includes parts such as printed circuit heat exchangers, busbar battery interconnects, bipolar plates for fuel cells and electrolysers used for hydrogen production.
“The increased volumes needed to meet this demand, however, often require much larger and thicker sheets of metal to be used and after many conversations with customers in the green energy sector, it became clear there was a gap in the market for a supplier that had the capacity and equipment to manufacture these components.”
Believed to be an industry first, the new etch room is home to six new ‘state of the art’ etching and stripping machines, as well as an automatic exposure unit which enables larger sheet metals up to 1,500 x 600 x 2.5mm in size to be etched in production volumes. In addition to increasing throughput and delivering cost savings to customers, the new equipment also minimises human interaction and manual handling.”
To support this investment, Precision Micro has also made further improvements to its chemical regeneration processes by introducing automated systems that will increase the overall effectiveness of the new machines.
Mr Hollis concluded: “Larger sheets of metal require more chemistry and subsequently more waste management. ESG ( Environmental, Social and Governance) is at the forefront of this investment with Precision Micro already regenerating or recycling 98% of its waste site-wide. We are hugely excited about this unique offering and looking forward to helping emerging sectors create the technologies required to make ‘net zero’ a reality.”