New S110 internal cylindrical grinding machine in situ at White Drive Motors and Steering SP Z.O.O.Poland-based
White Drive Motors and Steering SP Z.O.O., a leading global provider of motors and steering solutions, recently invested in a new S110 internal cylindrical grinding machine supplied by Swiss company
Studer.
Paweł Soćko, senior process engineer at White, said: “We opted for the S110 because it exactly meets our requirements in terms of performance and quality in production. Thanks to our long-standing cooperation with Studer, we are able to grind our components with the highest precision but with comparatively low costs — Studer is instrumental in our success.”
In White’s modern plant in Wroclaw which employs around 600 people, several Studer machines are now in use alongside the new S110, as well as other machines from sister companies in the United Grinding Group. This setup enables the production of innovative electrohydraulic high-performance solutions, for example for steering systems in agricultural and construction machinery. White has over 50 years’ experience in this field and is now part of the global
Interpump Group.
Adrian Schürch, Studer’s area sales manager for Poland, said: “The relationship with White has existed for decades and we are delighted that our grinding machines can continuously contribute to their success here.” As Studer has a local representative in Poland, communication went very well right from the start. However, before deciding on a specific machine model, the requirements of the component to be produced with it had to be determined. He added: “As always, we examined this in detail with our specialist team to find the best solution for the customer.”
Excellent price-performance ratioIn this case, an optimal solution was required for the internal grinding of hardened steel sleeves for hydraulic steering systems. It quickly became clear that the S110 from Studer’s extensive range of grinding machines was ideal for the component geometry and production requirements. Mr Schürch continued: “In addition to high precision, reliability, and compactness, this internal cylindrical grinding machine also offered an excellent price-performance ratio.”
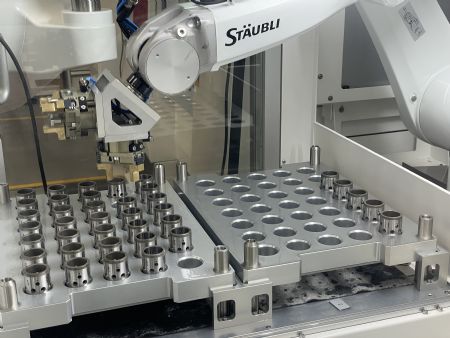
But that was just the beginning. The Studer team specially configured and adapted the S110 for White so that the machine could be easily integrated into and enhance the production process. This fell within the remit of Cesare Mastroianni, who is responsible for project management at Studer’s internal grinding competence centre in Biel.
He said: “The optimisation is based on the specifications, where all technical details, the geometry of the component to be manufactured, and operation plans are defined. We worked on this with the customer and were very impressed by White’s technical expertise, professionalism, and constructive attitude. It was a very pleasant cooperation, and between us we found the perfect solution between customer requirements and technical implementation.”
One of the challenges was to find the best mix of short cycle times in series production and high component quality. The S110 is now able to grind around 350,000 high-quality sleeves per year at the plant and White is extremely satisfied with the result. Mr Soćko said: “We produce in high volume, and this requires the best solutions in the world — because we cannot afford any losses due to insufficient precision or fluctuating capacity. The Studer S110 meets our requirements perfectly, it is both stable and reliable.”
Automation capabilityAnother reason for choosing the S110 was its automation capability. In the optional loading and unloading cell, a robot picks up the raw parts from a pallet, clamps them in the machine, and places the finished ground sleeves in another pallet. This process only takes a few seconds per sleeve. The S110 can therefore operate autonomously for at least one hour without human intervention and internal functions facilitate quality control.
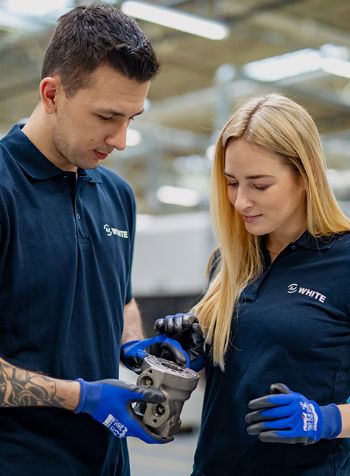
Mr Soćko added: “In practice, we even have almost two hours of autonomy, which reduces labour costs enormously.” This also has major benefits for production efficiency — employees can devote themselves to other tasks and the robot ensures a speed and consistency that would otherwise not be attainable.
While the new S110 improves production with its high-tech capabilities, White continues to rely on tried and tested Studer technology — the oldest of the company’s Studer machines is still working well after 30 years. One reason for this is the machine overhaul service that Studer offers its customers, where an ageing machine can be restored to as-new condition — as when it first left the factory. Steven Thiel, Studer customer care consultant for Eastern Europe and Northern Germany, explained: “Customers who are familiar with their machines and do not require new technologies for grinding components benefit enormously from this service. This is because the machine overhaul only costs a fraction of the price of a new system and the customer can continue to work with the familiar machine in as-new condition, ensuring optimal precision and quality.”
The sustainability factor is also important for White, which has already had several machines overhauled. Mr Soćko said: “Environmental aspects always play a role for us, which is why Studer machines with their energy-saving solutions fit perfectly with our corporate values.”
This is because instead of replacing an outdated model that once required a lot of energy and resources to build, it can be used again for decades. It takes around three months to overhaul a machine at Studer‘s plant in Thun, Switzerland, with the machine tool manufacturer taking care of all aspects of logistics — a loan machine is provided so that there are no production downtimes.
With its proven processes combined with the latest technologies, White believes it is well-positioned for the future. Mr Soćko concluded: “Properly implemented processes ensure success. Studer has shown that it is the ideal company to accompany us on this journey.”