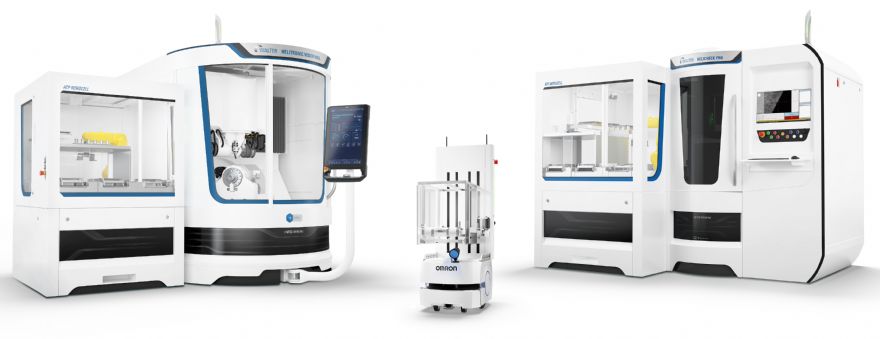
With its new automated tool production (ATP) system, Germany-based
Walter, a manufacturer of high-quality CNC grinding, erosion and measuring machines, offers an innovative automation system for highly effective tool handling in the manufacture and inspection of precision cylindrical cutting tools — effectively networking its own tool production and measuring machines but also upstream and downstream machines from other system partners.
Available in the UK from Warwick-based
Walter Ewag UK Ltd, ATP provides a higher degree of automation which results in higher levels of efficiency. ATP does not require additional floor space and can be integrated into existing tool manufacturing systems independently of current automation providers and without the need to change system layouts.
System control is based on the OPC-UA data model ‘Flames’ and comprises at least one robot cell accessible from the front (ATP Robocell) for automatic machine loading/unloading plus at least one autonomous, mobile transport robot (ATP AMR) for transporting workpiece pallets and individual parts between storage and processing stations. OPC-UA also includes a standardised communication model between the machines and ATP AMR, as well as a control system for higher-level data and process control.
The ATP Robocell offers three access gates and therefore additional buffer spaces for production without waiting times or even downtime. A separate removal station for the in-process exchange of individual tools between the measuring and production machine enables automatic correction and, as a result, closed-loop processing. A multi-range gripper in the ATP Robocell contributes to the system’s high flexibility. The gripper covers a large workpiece diameter range and can exchange collets at the same time.