Hybrid processes such as stone and belt processing, can be carried out on the NaShaft Eco-Suprfinish centres. Photo: NagelNagel Maschinen- und Werkzeugfabrik GmbH is presenting its latest technologies at
AMB 2024 (Hall 5, Stand B21 and Hall 1, Stand B80), currently taking place 10-14 September at the Stuttgart exhibition centre. For example, the focus will be on cost-effective and flexible honing solutions for small series, individual pieces and prototypes, as well as versatile systems for superfinishing. New additions include robot-assisted superfinishing of free-form surfaces, the revolutionary NaPrep technology for selective cutting edge rounding and solutions for e-mobility.
Nagel's developments have a dual focus: on the one hand, they want to contribute to cost reduction through greater efficiency and, on the other, to reducing CO
2 emissions. This includes, for example, increasing the service life of tools and machines. The associated reduction in manufacturing and energy costs plays an important role in the company’s — and now every company’s — sustainability strategy. This is because every manufacturing company is now required to account for its resource consumption. Nagel’s solutions are developed according to sustainability criteria, but also aim to produce long-lasting, sustainable products for customers. The company will be presenting and discussing examples of this at this year’s
AMB.
A specialised honing machine is not always required for honing bores. Using optimised honing tools, machining companies can also achieve high-quality bores on machining centres and similar machines without having to reclamp the workpiece. This reduces the machining time and therefore the costs per bore. Nagel offers both classic honing and single-stroke solutions such as the Precidor tools and the new, cost-effective DAL-E honing drills. Both are characterised by high dimensional and shape accuracy, and this for all types of materials, even hardened materials.
High-precision resultsThe DAL-E drills, based on the proven Precidor tools, offer a service life-optimised and economical alternative to reamers. They enable high-precision results and are versatile thanks to their simple adjustability. These tools can be used not only on machining centres, but also on lathes, milling machines and even hand-held drilling machines, which makes them particularly flexible and adaptable.
Pictured right: NaFin: a modular machine concept for creating ultra-fine surface topographies down to Rz <0.2µm.As a machine highlight, Nagel is presenting a NaShaft Eco superfinishing machine. Superfinishing is a technology on the rise, as excellent or precisely defined surface quality, e.g. on shaft journals, has an impact on efficiency and therefore on the CO
2 footprint. NaShaft Eco, for example, enables the defined production of roughness topographies and optimum geometry values. The machine’s ultra-fine machining processes significantly increase the load-bearing capacity of the machined surfaces. Sealing seats can also be machined more precisely, minimising the amount of leakage of the often expensive lubricant — a cost and environmental aspect.
Another advantage is the flexibility in terms of machining processes: whether superfinishing with belt or stone, the NaShaft Eco offers the right solution. The superfinishing belt works with ground shells, pressure rollers or the patented dFlex 2.0 multi-range finishing shell. Alternatively, a specially adapted high-performance superfinishing stone can be used, which enables precise material removal thanks to workpiece rotation and short-stroke oscillation.
The machine also offers fully automatic belt and stone repositioning as well as the option of using up to four compact, high-performance finishing modules simultaneously. In addition, brush deburring processes for defined edge rounding and polishing operations for the production of high-gloss surfaces can be integrated as additional processes.
Operation particularly easySpecial equipment features include full panelling with integrated tool drawers, a 200-litre detergent preparation unit and an automation interface that enables loading from four possible sides (front, rear, right and top). The touch panel makes operation particularly easy.
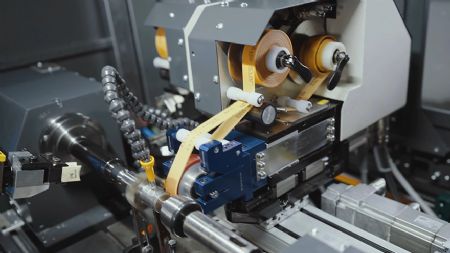
What’s more, at Nagel, customers not only receive a machine, but also the cutting tool production in-house. This guarantees consistent quality. Furthermore, there is only one contact person for all matters.
A current key topic in the field of superfinishing is bearing machining. The experts at the Nagel stand will be providing new information to interested parties from this sector. Since, as with shafts, the demands on surface quality are also constantly increasing for rolling bearings, Nagel and the Italian grinding and finishing specialist
O.ERRE.PI. have recently started offering a complete hard machining line for rollers and bearing rings, consisting of a cylindrical grinding machine, face grinding machine and NaFin SCD finishing machine. The message from the two partner companies to bearing manufacturers is that all components come from a single source. This saves users costs, as there is no need to coordinate with several suppliers.
The NaFin SCD is a centreless throughfeed superfinishing machine based on a modular machine concept. It impresses with its ability to produce the finest surface topographies down to Rz <0.2µm. The centreless throughfeed process is the fastest and offers maximum process reliability for ultra-fine machining of rotationally symmetrical surfaces. The outstanding features of the machine include the reduction of surface roughness, the generation of precise generatrix shapes as well as the increase of the material contact ratio and the improvement of the short wavelength. The modular design of the machine enables to offer customised solutions for specific production tasks.
The equipment includes high-performance, mass-balanced and monitored oscillation drives with a long service life. The feed rollers of different insert lengths can be adapted for various applications such as tapered rollers. The machine also features automatic wear compensation for the stone tool, including end-of-life and breakage monitoring (Industry 4.0 interface), which increases efficiency and durability.
Unique competitive advantageThe machines are known for their robustness and long service lives of over 30 years in some cases. Another significant advantage is once again the in-house development of cutting materials by Elgan, a sister company of Nagel. The material composition of the customer’s workpieces is examined in the laboratory, after which the appropriate stones are manufactured in-house. This customised approach guarantees optimal results and a high level of customer satisfaction.
With the combination of Nagel’s innovative technology and comprehensive service and O.ERRE.PI.’s expertise in hard machining, this partnership offers customers a unique competitive advantage. The NaFin SCD machine and the complete hard machining line set new standards in bearing machining. Customers benefit from an end-to-end process chain with high quality and maximum efficiency.
Pictured right: honing tool with holder for the spindle in the machining centre or another processing machine. The equipment includes honing stones that can be expanded using coolant pressure and an optional connection for air measurementRobotics and automation have long been focus topics at Nagel. For this reason, the new Advanced Robotic Solutions department was created. The company is thus pooling its many years of experience in process development, cutting tool production and the development of customised special machines. One of the most recent projects is the robot-assisted precision machining of free-form surfaces.
Product manager Manuel Kernchen names a few applications: “The flexible robot technology enables the machining of complex geometries, such as those required in medical technology for knee and hip joints, in general industry for taps and door handles and in the automotive sector. The potential for increasing efficiency in the polishing of injection molds is particularly noteworthy.”
With the help of an intuitive path planning tool, the robots can be easily programmed without any special knowledge of programming languages. Nagel’s approach of continuously working on the improvement and further development of ultra-fine machining technologies is paying off.
Mr Kernchen continued: “The growing experience in process development and mechanical engineering expertise gives us the opportunity to constantly optimise the technology and transfer it to new fields of application. We are at the beginning of an exciting development and are convinced that our robot-controlled superfinishing of free-form surfaces will make a significant contribution to increasing efficiency and improving quality in many branches of industry.“
The new NaPrep technology is also part of Advanced Robotic Solutions. With this, Nagel is entering the field of tools with geometrically defined cutting edges. NaPrep stands for an innovative solution for the selective and defined rounding of cutting edges on milling cutters, drills, indexable inserts, etc. Originally developed from an internal request from sister company TBT Tiefbohrtechnik, NaPrep quickly developed into an independent product with great market potential. The concept is based on a robot-controlled brushing process. Nagel opted for this process as it allows targeted control of the material removal. A cutting edge can be rounded in different ways, even with brushes.
A highlight of the NaPrep concept: the integration of optical 3-D measurement technology from
Bruker Alicona provides an in-process measurement system that delivers high-resolution and robust measurements of the cutting edge. The process is thus continuously monitored and readjusted if necessary, so that optimum and, above all, repeatable results are always achieved. The first machines have already been successfully tested by customers.