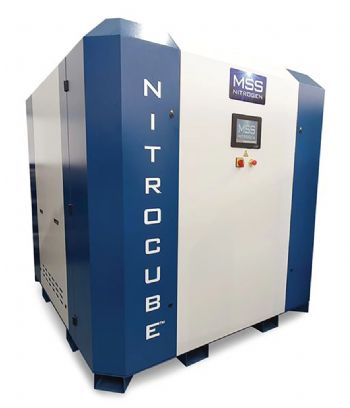
Rugby-based
MSS Group is set to exhibit a range of technologies at
EuroBLECH 2024, which takes place 22-25 October, in Hanover (Hall 12, Stand B183).
Taking centre stage will be the MSS Nitrocube ECO, a nitrogen generation system which is the UK and US market leader in on-site, high-pressure nitrogen generation. The most efficient system available anywhere, the Nitrocube combines the highest quality components housed in a unique cube enclosure with sophisticated MSS intelligent monitoring and controls.
All systems provide 300bar nitrogen and 99.5-99.999% gas purity as standard, a huge range of flow rates and storage capacities are available to suit most applications. The new MSS Nitrocube ECO offers class-leading efficiency backed with MSS unrivalled pedigree and experience of laser cutting applications.
Also on display will be the MSS Aircube, a high-pressure compressed air plug and play solution for laser air cutting applications. A compact and quiet all in one system providing clean, dry and oil-free compressed air supply for laser cutting assist gas. All systems provide 15 or 40bar compressed air, and generous 150m
3/h flow rates as standard. Aircube also feature an outlet dewpoint monitoring control with emergency shut-off in case of an air quality issue to give the laser system full protection from condensate or oil contamination. This performance and safety combined with MSS unique intelligent monitoring and controls package makes the Aircube a sound solution to those looking for an economical and secure laser cutting gas package.
On-line variable gas-mixing technologyAlso highlighted will be the MSS Nitr02 — an innovative gas mixing system. MSS Nitr02 gas mixer system has been specially developed by MSS for use with high-power fibre laser cutting systems, and is the only one available on the market today that allows on-line variable gas-mixing technology with fully integrated CNC controls to allow the laser operator to select the precise nitrogen/oxygen gas mix required directly from the laser HMI control.
Extremely compact, the system can be installed with minimum floor space without the need for any large storage tanks, simply connect existing nitrogen and oxygen lines into this unit and you will have the same outputs plus a variable ‘mixed gas option’ to optimise your laser cutting quality. This clever technology allows significant increases in fibre laser cutting speed and quality and give higher quality cutting results on lower quality plate material.
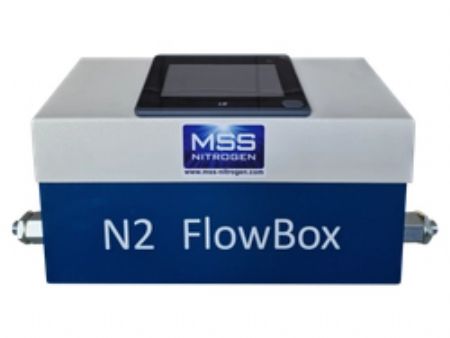
Also on display will be the Oxyboost — a liquid oxygen line pressure boost system for laser gas mixing which is an important development for laser users wishing to use their existing liquid oxygen supply for laser gas mixing applications. A standard liquid oxygen gas line supply does not provide adequate pressure for laser gas mixing systems to function correctly, so MSS have developed this new system to overcome this issue. MSS Oxyboost may be installed on all liquid oxygen lines in conjunction with the MSS NitrO2 gas mixing unit for a complete package solution to suit all laser operations.
Another highlight will be the MSS Flowbox, a gas use measuring and monitoring system. MSS Flowbox measures and monitors high-pressure nitrogen gas flow into the laser cutting system allowing the operator to exactly measure the amount of gas used on a daily basis and even scrutinise the volume of gas used per product/sheet being cut to understand overhead costs more accurately. The Flowbox can also be used for leak detection and may be installed on any laser-cutting system.
Completing the ine-up will be the MSS Puregas — a laser-cutting gas filtration system. The MSS PureGas filters high-pressure nitrogen, oxygen and compressed gas to particles sizes >0.01µM including oil vapour removal carbon filter stages. The MSS Puregas may be installed on any fibre laser to give full protection against particle damage or oil contamination to the laser cutting system including the cutting head. An important safeguard and a must for all fibre laser operations especially where nitrogen and air lines/ring mains may be old, degrading or contaminated.