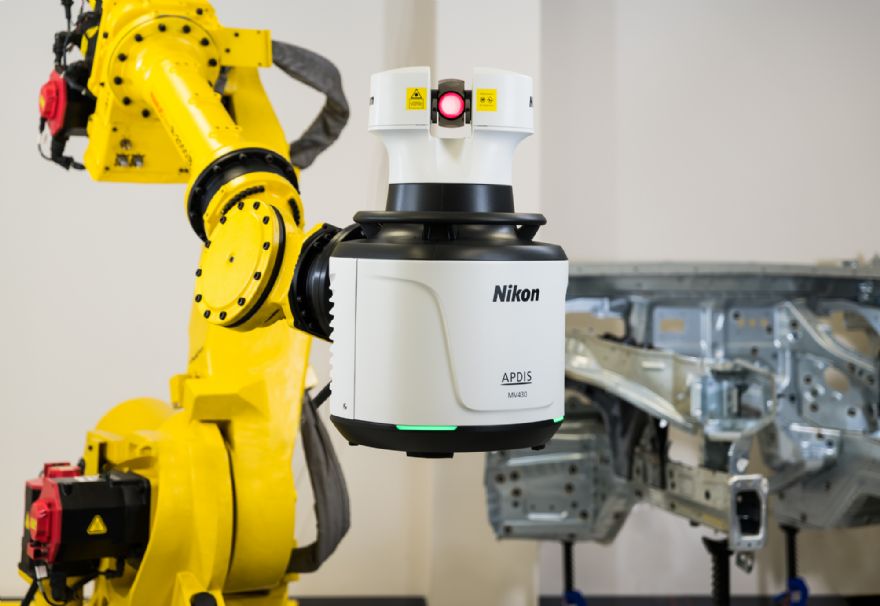
Nikon Metrology NV, a subsidiary of
Nikon Corporation, a supplier of traceable shopfloor metrology, has welcomed the recent comprehensive update to Volume 5.1 of the automotive measurement standards issued by the German Association of the Automotive Industry (VDA). The newly updated standards cover a wider range of measurement applications within the automotive sector, and address the industry’s growing demand for more diverse and sophisticated metrology solutions.
Andreas Fuchs, an application engineer at Nikon Metrology, said: “We already offer innovative, traceable measurement solutions based on national and international standards for the automotive industry. The new standard defines very precisely the procedures for evaluating the precise technology that we provide. After all, with the APDIS laser radar, our portfolio has featured a product for some time now that can also deliver traceable inline measurements as described in VDA Volume 5.1. Incidentally, those who use this technology no longer need a dedicated measuring room for a fixed cordinate measuring machine – enabling them to save a great deal of money, time and space.”
The unique APDIS Laser Radar has a proven ability to measure details at a distance without needing handheld probes, targets, or surface preparation makes it ideal for automating repetitive inspection tasks with high accuracy. The system covers many manufacturing, industrial, and research applications, including those that involve hard-to-reach features and are complex, delicate, or labour-intensive.
The additional benefits of the APDIS Laser Radar include fast and accurate automated measurements with minimal set-up time for maximum productivity with flexible and portable installation. This allows for the absolute and accurate measurement of parts during production or wherever required, including directly on the production line. The APDIS Laser Radar, in particular, displays its strengths in the automotive industry. For example, the system can measure automotive features with absolute accuracy at high speed with no part preparation, whether inline or offline.
Smart evaluation methodsWith inline measurement, data can be collected in a much larger sample, resulting in a much more extensive data volume for process control. Therefore, it is wise to develop and use smart evaluation methods or systems and, in the process, adapt the reaction speed to the increased data volume.
Mr Fuchs continued: “These days, inline measuring technology tends to measure 100% of the parts, giving a very dense test sample with an extremely short response time and close to production. When the part goes through, a real-time statement regarding the quality of the part is delivered immediately – meaning the response time, as well as statistical and general process control, are far better than before. A measuring room, on the other hand, only provides information about ongoing quality with a delay. In addition, there are no statements about the ongoing process, and production continues.”
VDA Volume 5.1 appears to consider the trend that measurements are increasingly being made using traceable inline measuring systems instead of offline in the measuring room, making the implementation of suitability certificates for inline measuring processes in accordance with VDA Volume 5 more critical. VDA Volume 5.1 introduces an eight-stage model for evaluating inline measuring systems throughout their lifecycle.
This model generates suitability certificates crucial for system release, ensuring compliance with automotive manufacturing standards. These certificates are significant in procurement as tenders for measuring systems regularly reference VDA volumes, highlighting the importance of standards in guiding industry-wide quality control and measurement practices.
Nikon Metrology will host a webinar on the topic of VDA Volume 5.1 on 17 September, 2024, at 11am: ‘APDIS Laser Radar already meets the guidelines of the new inline measurement technology standards’
The registration link can be found at:
here.