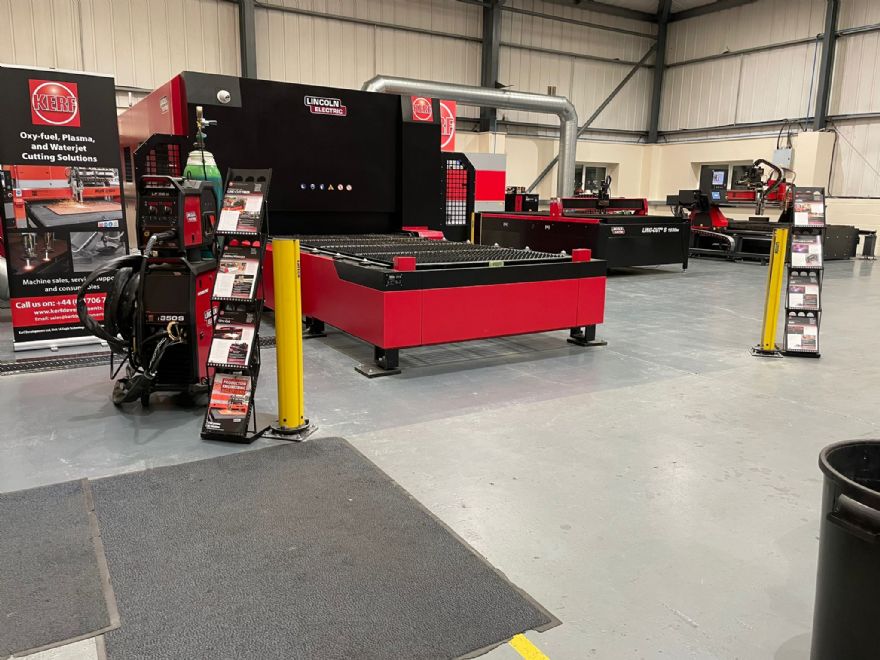
Earlier this month,
Kerf Developments Ltd — a manufacturer of advanced cutting and profiling technology — hosted an
Open House event at its Rochdale headquarters to celebrate the opening of its new technical and demonstration centre — a fully refurbished facility where engineers ‘can investigate the company’s complete range of profile cutting disciplines’.
Machines include fibre laser, oxy-fuel, UltraSharp plasma, and water-jet types; and while, based upon their cutting requirements and workload, some attendees arrived with a pre-conceived idea of what machine they needed, Kerf said expert advice and the company’s ability to offer a full suite of technologies enabled the ‘best-fit’ solutions to be proposed — those that ‘maximise productivity and efficiency while reducing production costs’.
The facility’s four new permanently sited machines comprise a new Lincoln Electric Linc-Cut Fibre 1530A fibre laser system, an Optima 420 water-jet system, a Kerf Ultra oxy-fuel machine, and an UltraSharp plasma machine. Introduced to the UK at
MACH 2024, the Linc-Cut Fibre 1530A is available as a 3kW, 6kW, or 12kw machine with a 2 x 1m, 3 x 1.5m, or 4 x 2m bed; it also incorporates advanced features such as ‘Flycut,’ ‘Fast-Cutting’, ‘Smooth Microjoint’, ‘Frame Border’, ‘Circle Centring’, and ‘Collision Avoidance’ — all designed to enhance productivity and cutting speed.
The UltraSharp plasma machine at the facility has the FineLine 300 plasma unit from Lincoln Electric, which features advanced piercing technology and a water-mist system that ensures high cut quality when cutting mild steel, stainless steel and aluminium, to minimise the need for grinding, edge preparation, and other secondary operations.
Meanwhile, the Ultra oxy-fuel machine incorporates a ‘unique oxy-fuel automatic gas console (AGC) that helps address ‘the industry’s current skills shortage by replicating the skills of an experienced machine operator by using pre-programmed technology software’. This sets variables such as cut heights for piercing, as well as low and high preheat gas pressures; the new AGC also reduces gas consumption, increases consumable life, and improves cut quality.
The Optima 420 water-jet machine can cut a broad range of materials, from granite and stone through to titanium, Inconel, duplex, super duplex, tool steel, and composites — and much more. Kerf says this machine will appeal to machine shops that want to make precision cut blanks, saving considerable time on subsequent CNC machining tasks and saving material consumption.