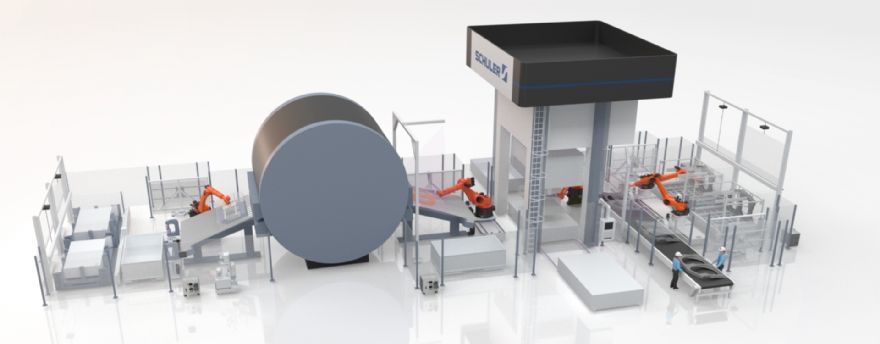
Conventional roller hearth furnaces have a length of up to 45m so that large components such as body sides or base assemblies can be produced economically by hot stamping.
BSN Thermprozesstechnik GmbH and
Schuler have now developed a compact rotary furnace that saves both space and energy, is also easy to maintain and, last but not least, ensures a repeatable temperature of the heated parts. This is important because any deviation from the specified temperature can lead to inaccuracies and therefore to problems during assembly.
With a length of 14m including loading unit and centring, a width of 6m including heating and drives and a height of 7m, the new compact rotary furnace requires only around a quarter of the space compared to a conventional roller hearth furnace. The minimum cycle time per part is 12sec. The innovative furnace, which runs on both electricity and gas, can save around 1,200MWh of energy per year.
The blanks for the body side of an SUV reach dimensions of 3,000 x 1,600mm. A 1,800-ton hydraulic press from Schuler with a table size of 3.60 x 2.5me is therefore ideal for the stamping process. The “Pressure Controlled Hardening” (PCH) technology ensures shorter cooling times and better forming tolerances here.
Schuler will present its latest solutions for forming technology at
EuroBLECH 2024, taking place 21-25 October in Hanover (Hall 27, Stand G82).