Photos courtesy of University of Glasgow’s James Watt School of EngineeringA ‘small piece of outer space’ recreated in a basement in Glasgow could help ensure that a key enabling technology for future space missions will not lead to deadly ‘rifle bullets’ of space junk circling the Earth. Researchers at the
University of Glasgow’s James Watt School of Engineering have built the NextSpace Testrig — the world’s first dedicated facility for testing the structural integrity of materials that will be 3-D printed in space.
The NextSpace Testrig was developed by the university’s Dr Gilles Bailet in partnership with the
Manufacturing Technology Centre, supported by £253,000 in funding from the UK Space Agency (UKSA). The facility, which uses a specially constructed vacuum chamber capable of generating temperatures between -150°C and +250°C to create space-like conditions on Earth, is designed to help support the developing field of space manufacturing which aims to radically change how objects and materials are sent into orbit.
Instead of carrying complete devices like solar reflectors into space on rockets, specially-designed 3-D printers could create structures more cheaply directly in orbit instead. Several experiments have already sent prototype 3-D printers into orbit and metal parts have been made using additive manufacturing (AM) by astronauts aboard the International Space Station (ISS).
Extreme physical strainsUntil now, no research facility has been dedicated to ensuring that polymers, ceramics and metals 3-D printed in orbit will be able to withstand the extreme physical strains they will face in space which are subjected to a hard vacuum that cycles rapidly between extremes of temperature — conditions that can wreak havoc on the structure of 3-D printed materials which are not rigorously constructed.
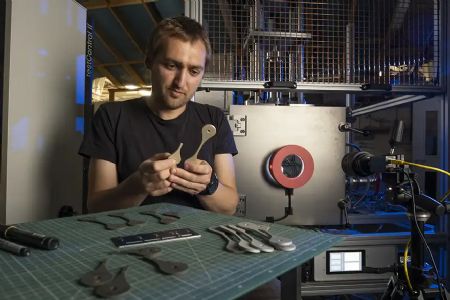
Imperfections such as tiny bubbles or poorly melted sections that might be inconsequential on Earth can behave differently in space. Those flaws could cause 3-D printed objects to shatter, scattering dangerous fragments into orbit which would contribute to the growing problem of ‘space junk’ — pieces of debris from defunct satellites, previous space missions, or collisions between human-made objects in orbit.
Dr Bailet said: “3-D printing is a very promising technology for allowing us to build very complex structures directly in orbit instead of taking them into space on rockets. It could enable us to create a wide variety of devices, from lightweight communications antennae through to solar reflectors, to structural parts of spacecraft, and even human habitats for missions to the Moon and beyond.
“However, the potential also comes with significant risk, which will be magnified if efforts to start 3-D printing in space are rushed out instead of being properly tested. Objects move very fast in orbit, and if a piece of a poorly-made structure breaks off it will end up circling the Earth with the velocity of a rifle bullet. If it hits another object like a satellite or a spacecraft, it could cause catastrophic damage, as well as increase the potential of cascading problems as debris from any collisions cause further damage to other objects.”
Real-world testingHe continued: “The NextSpace TestRig is open to academia, researchers and commercial customers from around the world to help them ensure that any materials they plan to 3-D print in space will work safely. We also expect that the data we will be gathering in the years to come — which cannot be replicated anywhere else in the world at the moment — will help regulatory authorities to make safety standards for in-space manufacturing, informed by real-world testing.”
The testing facility features a unique magazine system that can autonomously test multiple samples in a single cycle, making it significantly more efficient than traditional testing methods. The system can apply up to 20kN of force (equivalent to 2,000kg) to break samples and analyse their properties in vacuum conditions matching those of space. It can also subject samples to cycles of extreme temperatures mimicking those they would face in orbit.
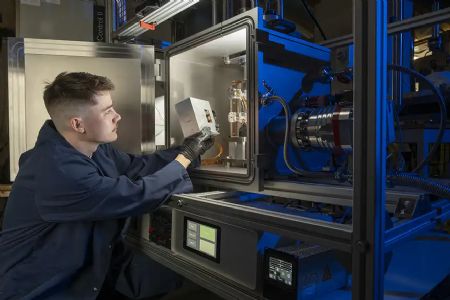
The facility is the latest development in Dr Bailet’s research in spaceborne AM. He has also patented a prototype 3-D printer which is designed for use in orbit and has been tested during a series of trips on a research aircraft known as the ‘Vomit Comet’.
He added: “We expect that the NextSpace TestRig will be of real use to the UK space industry in the years to come. Glasgow is already a centre of excellence for space technology — companies here manufacture the most satellites in the world outside the west coast of the USA. Our facility will help augment the capabilities of future spacecraft assembled in orbit, ensuring that the UK space sector can be more competitive internationally.”
The development of the NextSpace TestRig was supported by funding from the
UK Space Agency’s Enabling Technology Programme. Iain Hughes, the UK Space Agency’s head of the national space innovation programme, said: “We are proud to have supported the University of Glasgow in developing the world’s first facility for testing 3-D printed materials in space-like conditions. This innovation will help to drive UK advancements in space manufacturing, unlocking numerous benefits and meeting the Government’s growth ambitions while ensuring safe and sustainable space use.”