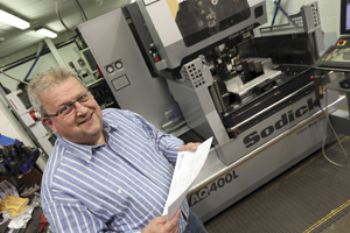
The Newcastle-under-Lyme-based company Xtrutech has installed a new wire-cut EDM machine that is allowing it to increase throughput and achieve shorter set-up times, thanks to the machine’s ability to accommodate 12 parts.
Xtrutech is a specialist in the design and process optimisation of twin-screw extruders, which are used extensively for mixing, compounding or reacting polymeric materials. The company also supplies its own range of spare parts, including screw elements, barrel housings and liners.
The manufacture of these replacement components, including producing the critical bore in the screw elements, is performed on the new Sodick A400L from Coventry-based Sodi-Tech EDM Ltd (
www.sodi-techedm.co.uk).
Prior to installing this new machine, Xtrutech had relied on four second-hand EDMs; however these were becoming increasingly unreliable.
All twin-screw extruding machines feature different figure-of-eight bores, and it is this feature that the AG400L produces through the hardened steel barrel liners.
Co-founder Richard Johnson said: “Screw elements rotate in the barrel at around 12,000rev/min, often at temperatures in excess of 300°C.
Cold resin or polymer, often containing an abrasive filler, is then introduced. As a result, screw elements become worn and often require replacing after 6-18 months.
“The biggest benefit of the new Sodick AG400L is the time savings it offers; after eight months, our studies show that it is 2.6-times faster than our earlier machines. Furthermore, we sometimes set-up six parts at a time, whereas we could only make one component at a time using our old EDMs.
“If we leave the AG400L running unattended overnight, we will often set up 12 parts — two per station.”
Mr Johnson added: “ We have major competitors in Germany, India and the USA, and around 60-70% of our output is for export markets —with the biggest user of replacement screw elements and barrel liners being the thermo-plastics industry.
“The AG400L has made us more competitive against companies manufacturing screw elements in other parts of the world.”