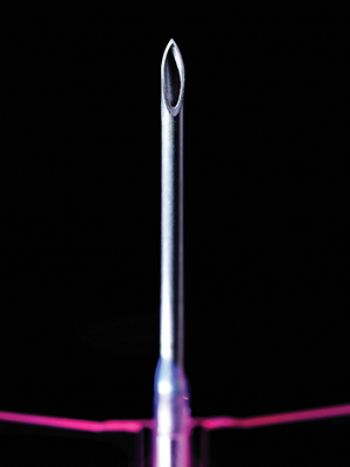
Developments in industrial metal-forming and welding processes sent the price of hollow stainless-steel hypodermic needles plunging during the middle of the last century.
This meant that doctors and hospital staff could afford to use needles once and throw them away, instead of having to sterilise and re-use them time and again.
Indeed, this advance in hygiene probably saved almost as many lives as the medication that the needles are used to inject; and while no official statistics are available, it is estimated that around a billion hypodermic needles are thrown away every day, turning the small price of a needle into a hefty sum.
Ralf Egerer, director of Machine and Cryogenic Systems at Nexans in Hannover, says: “Medical technology is expensive — even for what appears to be a cheap product — and we are working to reduce the costs. Our aim is to halve the price of hypodermic needles in the near future.”
He intends to achieve this goal using Nano Wema, a machine at Nexans that rolls extremely narrow stainless steel strips into ultra-thin tubes and then welds them with a laser beam from Trumpf (
www.trumpf.com).
Although Nexans is primarily a cable manufacturer, Mr Egerer says it is not such a great leap from cables to hypodermic needles. “To shield the wire bundles inside deep-sea cables against the effects of water pressure, we wrap them in thin-walled sheaths made of copper or aluminium, so we are used to producing long thin metal tubes. With NanoWema, we have managed to refine the process so we can make even narrower, finer tubing.”
The NanoWema process starts with the machine unwinding a thin 5km strip of metal from a spool and applying lubricant to it before form-rolling the metal into a perfectly round, open tube with the outside edges of the strip lying parallel and side by side. The gap between the edges is so fine that the Trumpf TruDiode laser has to be incredibly precise, focusing its beam to an accuracy of 0.2mm.
Instead of tracking the seam with the laser, Nexans developed a system for mechanically fixing the gap in place so that it is forced to pass exactly through the beam’s focal point. The machine then pulls the tube-shaped metal strip through a closing die, allowing the laser to weld the 5km-long seam from above in one go, without once having to adjust its focus.