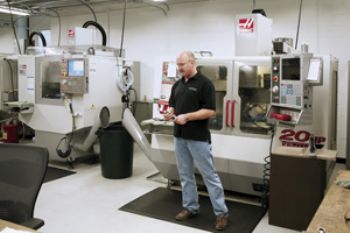
Addressing back problems is a challenge that attracts some of the brightest minds in medicine; and because many orthopaedic solutions are mechanical in nature, it also attracts some of the world's top engineers and machinists.
The American company NuVasive, based in San Diego, California, develops implants that align and help to repair the spine, as well as the tools that allow the use of 'minimally disruptive' surgery to position these implants. To perfect its products, the company relies on a staff of engineers and machinists working closely with medical professionals in its expansive headquarters, which house medical-research facilities, design laboratories and a 'state of the art' machine shop.
Machine shop manager Jeff Castleberry says: "Quite simply, we're a spine company. In one way or another, everything we do here helps surgeons relieve back pain. In this shop, we produce prototypes and proof-of-concept pieces of our fusion implants and surgical tools. The products are eventually manufactured in specialised large-run production shops, but in-house machining is a vital part of our product development, testing and client support."
NuVasive's classic fusion implants are made of precision-machined plates, rods and screws. The devices are generally used to re-align and stabilise the vertebrae on either side of a damaged spinal disc, but sometimes they form a bridge that allows the vertebrae to fuse together. The goal is to reduce pain by preventing the vertebrae from compressing the nerve trunks that radiate from both sides of the spinal column.
Minimising damage

One of the challenges facing the spine surgeon is to cause as little damage to surrounding tissue as possible when inserting and positioning these implants along the patient's spine. The ideal procedure is to make a small lateral 'tunnel' incision, then mechanically expand the small opening to the required larger size by taking advantage of the elasticity of skin and muscle. This 'stretching' technique allows maximum access to the spine with minimum soft-tissue trauma, and that's where NuVasive's novel Maximum Access Surgery (MAS) system plays an important role.
The MAS system comprises a range of proprietary surgical tools, from simple angled screwdrivers and electronic nerve monitors to complex multi-blade expanding retractors; and because the surgeon has to work through a small access point, many of the tools must expand or contract, which makes them very complex.
"This is where our machine shop plays an essential role. We prototype all the mechanical tools used in our special surgery platform, and we often custom-modify these surgical instruments to meet specific individual needs," says Mr Castleberry. "A doctor can write a prescription for a custom-sized tool to exactly conform to the size of his patient, or he may simply ask us for a tool with a bigger handle to more comfortably fit his particular grip. It's up to us to produce the special tools in-house - and quickly."
Mr Castleberry set up NuVasive's initial machine shop in 2001. Space in the 8 x 15ft room was so tight that he had to remove the door and windows to install a manual lathe and a knee mill. The modest in-house machining capability led to faster product development and the rapid introduction of new products; this, in turn, increased the company's market success. Within a year, Mr Castleberry was knocking out walls to gain more room, and upgrading the shop to CNC capability with a Haas VF-2 vertical machining centre (www.haascnc.com). "Even though we weren't in manufacturing, I knew that we couldn't afford to lose a machine, even for a day. Things were happening too quickly! The choice proved to be a good one, and we've standardised on Haas equipment ever since." After out-growing two more 'shops', NuVasive's current 5,000ft
2 machine shop employs six highly experienced machinists and the latest Haas CNC equipment. The machines include a VF-2 vertical machining centre, two Mini Mills and two Super Mini Mills, all equipped with four- or five-axis HA5C indexers. There's also a Super Mini Mill 2 (fitted with a TR-110 trunnion) and two TL-1 Toolroom Lathes. All machines are configured for quick turn-round.
Speed of response

"Cheetah Speed is the motto we work by. Quick product development is very important in this industry; when engineers bring us a print, we must quickly produce something they can hold - usually within hours, not weeks. We rely on the Haas VMCs fitted with rotaries to give us the full four- and five-axis capabilities we need; we count on them to save time by letting one 'single-mount' multi-axis positioning operation handle jobs that would otherwise require multiple ops and multiple set-ups. Since speed of response is most important to us, we work differently to most five-axis shops; we leave our rotaries more or less permanently attached to the machines."
NuVasive's carefully chosen array of 'always configured' multi-axis Haas machines allows the machine shop to start unique jobs quickly, with little time lost to set up; having enough of the 'right' machines is the key. "A lot of our work can be collet-mounted, thus avoiding complex fixturing," says Mr Castleberry. "However, if rotary equipment is in the way, we don't waste time removing it; we simply go to another machine configured in a way that will work for what we're making. To save time, we have about one-and a-half machines for every machinist."
Mr Castleberry says that while some of the company's work looks simple, none of it is easy. "In subtle ways, it's all very complicated. Because virtually everything the shop produces will be used inside a human body and will be handled by surgeons wearing easily damaged latex gloves, square corners and sharp edges are avoided. Indeed, our tools are designed specifically to slide in and out without injuring the patient or the surgeon.
"Everything has round surfaces that typically require finishes of 30 micron or better. We carefully configure our CAM post-processing to take advantage of the 15,000rev/min spindles and high-speed look-ahead capabilities of our Haas VMCs and trunnions. Getting a superior finish straight from the machine is vital to us. It reduces post-finishing, which we must always limit if we are to hold accuracy.
"We do a lot of work in 17-4 stainless; for our purposes, we find it is stronger than 304 or similar materials. Whenever possible, we like to heat-treat the stainless in-house, then machine it hard to get the cleanest finish and most predictable final dimensions. We also work with titanium, some exotic plastics - like PEEK - and occasionally aluminium, mostly for machine fixtures. We avoid reactive materials like brass, and we passivate our stainless and titanium pieces to prevent potentially harmful reactions within the human body."
Optimum cutting data
Although NuVasive's machined parts do not necessarily fit the term 'micro', the tools that it uses often do. "Some of our ball mills are just 0.020in in diameter, and machining titanium with such small tools is especially tricky. Moreover, because small titanium pieces distort when heated, we must produce large chips that carry away the heat; but to get large chips while running high spindle speeds for a good finish, it's necessary to maintain a consistent and high feed rate, even through corners. With complex parts and small tools, this can be a real problem. The high acceleration rates are particularly demanding on the machine, but we find the high-speed look-ahead processing of our Super Mini Mill 2 accommodates these easily.
"Development and custom work keeps us on our toes. Although we standardise equipment and procedures as much as possible, at the end of the day, almost everything we make is unique. Engineers are here in the shop all the time, and 'drop that, go with this' requests are a normal part of the flow. Having exactly the right tools - reliable multi-axis machines, configured and ready to go - makes our type of work possible."