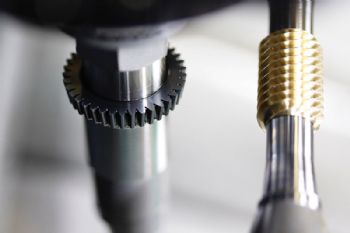
Affolter Technologies SA (
www.affoltergroup.ch), a leading manufacturer of micro-gear hobbing centres for the watch-making and micro-mechanical industries, recently introduced worm-screw power skiving (WSPS).
Managing director Vincent Affolter said: “This cutting-edge technology allows us to finish a high-precision worm in only 6sec, compared with 25sec for worm hobbing. This will considerably increase the productivity and efficiency of manufacturers in the automotive and aircraft industries.”
Many manufacturers in these industries need to produce large quantities of high-precision worms. The WSPS technology focuses on small worms with a module of 0.3 to 1.5. Mr Affolter said: “Such worms are used in car seats or boot lids, for instance. We see a big demand in the automotive industry, but also in other sectors.” says Mr Affolter.
Unlike in worm hobbing, where the hob turns much faster than the workpiece, Affolter inverted the process. “The workpiece turns extremely fast, with two spindles turning up to 12,000rev/min, while the cutter turns much slower.
“Over recent months, Affolter engineers redesigned the well-established AF110 to optimise the WSPS process. The result is a brand-new machine — the AF110 Plus.
"We integrated cutting-fluid filtration and chip disposal systems. This allows us to cope with all the requirements imposed by the workpiece up to module 1.5 and the production of large volumes of chips.”
A prototype of the AF110 Plus will be shown at the trade shows AMB in Stuttgart (13-17 September), Micronora in Besancon, France (27-30 September), IMTS in Chicago (12-17 September), and Jimtof in Tokyo (17-22 November).
Affolter’s agent in the UK is Leicester-based 3A Technologies (
www.3atechnologies.co.uk).