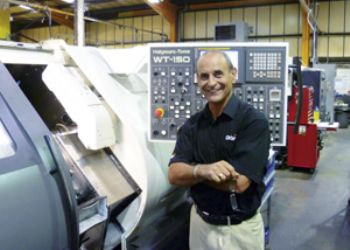
After purchasing its premises, Portsmouth-based sub-contractor DKW Engineering has been focused on the future — upgrading facilities, re-branding the company and investing in new capital equipment.
Over the past 18 months, a £500,000 investment programme has seen the company add two multi-axis turning centres, including a Nakamura-Tome WT-150 twin-spindle, twin- turret lathe. Most recently, it has added a Feeler VMP-580 three-axis vertical machining centre fitted with a Lehmann TF-507510 two-axis positioner that allows 3+2-axis machining. This takes the company into the realm of five-sided machining in one set-up and opens up the future possibility of full simultaneous five-axis machining. The Nakamura and Feeler machines were supplied by Turning Technologies UK and Feeler UK respectively — both members of the Southam-based Engineering Technology Group (www.engtechgroup.com).
Nick Iacobucci, managing director of family-owned DKW Engineering, says: “We had previously leased our premises, so it was a major decision for us as to whether to stay there or not; but having been able to purchase them has allowed us to target other things that we wanted to do.
“We are not just upgrading the building but also re-branding the whole company — our business cards, our Web site, the outside of the building and the internal facilities. Our objective is to bring us bang up to date. In simple terms, I want my shopfloor to look like a machine tool showroom.”
Latest technology
He says that the building has been a pretty heavy investment, but equipment has been a focus too. “Without question, the only way to maintain and increase your business is to have the latest technology. We have always been very proud of producing high-quality components, but you can only do that if you have the right equipment and the right people. Moreover, the combination of the latest equipment and a good working environment allows us to attract the right personnel.
“We had been looking at upgrading our machining facilities, and at the last MACH exhibition I was very impressed with the specification of the Feeler range, so much so that we agreed to buy one of the machines that the Engineering Technology Group had on its stand. It was already configured in a 3+2 format with the Lehman rotary table. Accuracy, quality and speed of machining have been improved dramatically, compared to our existing equipment. We have used the 3+2 capability quite happily, and that has improved the finished products we are making on it.”
The VMP-580 is a three-axis BT-40 machine with a 12,000rev/min spindle and a work envelope of 580 x 420 x 510mm. It has a 24-tool magazine with a 2sec tool-to-tool time and rapid feed rates of 48m/min in X, Y and Z. The machine uses a Fanuc 0iMD control and is supplied as standard with a fourth-axis interface. Compared to a full five-axis machine, the Lehman 3+2 configuration gives the option of five-sided machining (Lehman estimates that 90% of all processes carried out by five-axis machining centres are pure five-sided processes for which three-axis verticals with fourth- and fifth-axis options are effective). Furthermore, the Lehman unit can be easily removed if three-axis machining is sufficient, leaving the entire machining area available for large and bulky workpieces.
Mr Iacobucci says: “We are using the 3+2 configuration to position the part so that we can machine five sides of a component in one go and reduce set-up time. Where we previously required maybe two or three operations to do various types of milling or drilling on, say, a valve block, we can now just do it by swinging from one orientation to another.”
He says that the next step on from 3+2 machining may be to move to simultaneous five-axis machining on the Feeler, which will require an upgrade to its CAD/CAM system. “We are taking it step by step. It is a development process from our point of view, but it does give us that facility; and if we get a job that justifies the software upgrade, we will do it.”
Enhanced turning

DKW’s previous investment in the Nakamura WT-150 turning machines was made as part of its focus on increasing capacity and capability in the bar diameter range 50-65mm. As with the Feeler machine, one of the objectives was to reduce set-ups and get parts off in one set-up.
Mr Iacobucci says: “That’s what we do on our sliding-head machines, and this latest investment moves this approach up the size range. With the Nakamura’s twin spindles and twin turrets, there are so many operations that you can do on it. We wanted consistent production coming off the machine, and we are more than pleased with the performance the Nakamura has given us, especially from a quality point of view.
“When I look for a replacement machine, it is rarely because the old one is worn out; it will normally be a question of upgrading to the latest technology. That is what we have always done, and we wait until we can afford the best machine; I don’t believe in buying anything else.”
He says that investment is a critical aspect of DKW’s business — not just in machines but also in staff, apprentices, facilities and, in particular, customer care. Most of the company’s customers are in the UK, but it does export to the USA and Europe, as well as a small amount to China. The industry sectors covered include aerospace, nuclear, petrochemical, electronics and sensors, with 70% of the work in stainless steel. One of its recent high-profile jobs was machining the Spirit of Ecstasy figure for Rolls-Royce cars.
Mr Iacobucci prides himself on the fact that 90% of new business comes through referrals; indeed, the company has long-term contracts with most of its customers. “We are very much a family company, and it is our intention to continue to grow by investing in the facilities and equipment to do so.”