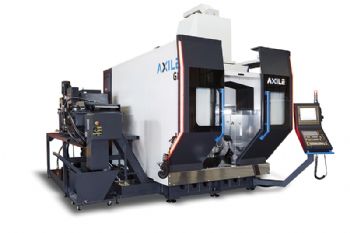
Sheffield-based TW Ward CNC Machinery Ltd (
www.wardcnc.com) will be well represented at EMO by a number of the company’s principals. For instance, two of the five vertical machines being displayed by Hartford (Hall 27, Stand F50) incorporate features that represent significant advances for the Taiwan-based manufacturer of vertical machining centres. The TGV-1612 will be shown with the fourth version of Hartford’s Hartrol Plus control technology. This latest-generation CNC incorporates Smartcentre functionality and multiple apps designed to improve operation, plus a ‘manufacturing executive’ system that allows production status monitoring via portable devices. Elsewhere on the stand will be the S-Plus production centre, which will be enhanced by Robocell robot handling (Hartford’s latest Industry 4.0 initiative) for unmanned ‘lights out’ operation.
Another Ward CNC principal, Soraluce (Hall 13, Stand B36) will also be using EMO to showcase its continued emphasis on encouraging and creating digital-manufacturing scenarios. Visitors to the stand will be able to discuss the Soraluce digital strategy, which includes a data system that uses cloud computing and big data technologies in machine data-driven analy-tics tools to monitor machine status and condition. Meanwhile, Advanced HMI is a utility suite on the Heidenhain TNC 640 CNC that presents a user-friendly interface via soft keys, customised diagnostic masks, manufacturing cycles, dynamic collision monitoring and advanced tool management.
Regarding Soraluce hardware, the TA-A35 bed-type mill, FM-T 4000 multi-tasking mill-turn centre and FR-W 18000 floor-type milling/boring machines will be on show, complemented by DAS+ — an enhanced version of the company’s Dynamics Active Stabiliser system. DAS+ offers spindle-speed tuning, where the machining process is monitored to provide the best cutting conditions for each particular operation.
Five machines will be displayed by Takisawa Taiwan (Hall 17, Stand B54), including the new MX-800 twin-spindle twin-turret turning centre. This machine is constructed on a horizontal box-type base to minimise thermal deviation
and maximise machining accuracy. The machine design also increases the spacing of the linear guideways on the X, Y and Z axes, to boost stability and permit high-speed cycles.
With twin facing T15 turrets and twin spindles, plus a C axis for simultaneous second operations, the MX-800 is suitable for multi-task machining in a single set-up. The machine has twin 65mm-bar-capacity spindles, a maximum turning diameter of 230mm, a distance between centres of 1,100mm, and a turning length of 250mm. A built-in robot or gantry system can also be supplied.
A trio of cost-effective two- to four-axis lathes will be displayed by the Spanish company Pinacho-Metosa (Hall 16, Stand A23). Ward CNC says that now available in the UK are the two-/three-axis ST series and the up to four-axis (with C axis) STH series of semi heavy-duty turning centres capable of in-cycle milling (via Y-axis capability). On show will be an STH 400 and an STH 500. STH machines offer bed lengths up to 5,000mm, 17kW spindle drives, feed rates of 7,000mm/min, and 10m/min traverse rates in both the Z and X axes. The Pinacho ST series comprises four main models — the ST-180, ST-225, ST-285 and ST-310 — with each machine type offering varying bed lengths up to 3,000mm.
Recently made available in the UK by Ward CNC, the high-speed Axile overhead travelling-gantry five-axis vertical machining centre will be shown by the Taiwanese manufacturer Buffalo Machinery (Hall 27, Stand A46). A pair of Axile machines will be included in the display. The G8 model features a Kessler 800mm-diameter table for workpieces weighing up to 1,300kg, a work envelope of 670 ¥ 820 ¥ 600mm, a positioning accuracy of 0.008mm, and a repeatability of 0.004mm. The linear axes feature direct-servo-driven double roller-type linear guideways and linear-measurement feedback scale. In addition, the Y axis has twin left-hand/right-hand linear guideways, while the Z axis incorporates a three-guideway design for enhanced rigidity and cutting performance. The maximum feed rate in X, Y and Z is 60m/min.
The stand will also highlight Buffalo’s emphasis on Industry 4.0 and its smart machining technology; this offers functions for monitoring machine performance and compensating, where necessary, to improve machining accuracies
and productivity.