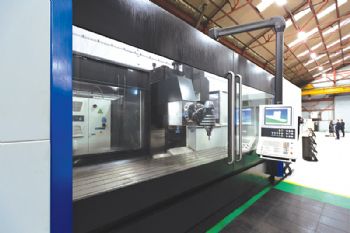
TPG Engineering, the Dukinfield-based specialist manufacturer of heat exchangers and condensers — and a major Tier Two supplier to prime contractors in the industrial, energy, process and defence sectors — has established an integrated manufacturing centre that is “one of the most advanced facilities of its kind in North West England”, with an investment of almost £2 million in machines, facilities and personnel.
The centre was initially designed for the production of high-specification heat-exchanger-tube plates for a major nuclear power project won in 2016, but it can accommodate a variety of large-capacity and demanding work.
TPG’s project director, Darren Sadler, said: “The combined capability of the machines we bought is ideal for the production of physically large and highly accurate workpieces.
“These are predominantly in titanium, as well as other exotic and hardened materials; and with the tight tolerances that can be achieved, we can produce parts that are fit for nuclear-engineering clients throughout the world.”
The company has installed a Soraluce TA-A35 travelling-table mill-bore centre and a Hankook VTC 200 E vertical turning lathe (VTL).
The Soraluce machine has a work envelope of 3,500 x 1,250 x 1,200mm and accommodates components weighing up to 7,800kg, while the Hankook VTL has a 2,500mm-diameter table capable of accommodating workpieces up to 2,000mm in diameter and weighing up to 12,000kg.
Mr Sadler said: “Importantly, very few companies — other than OEMs — have a VTL of this size, so we are very well positioned to handle large components.

“Moreover, the 28kW Soraluce, with its 40-tool ATC and 4,000rev/min automatic-indexing — in 2.5deg increments — machining head, is invaluable when it comes to producing the ‘PCD pattern’ of holes on exchanger plates. These holes can vary from 13 to 16mm in diameter.
“The power of the Hankook VTL also helps to set us apart from our competitors.
For example, it features a 55kW table drive, a high-torque 22kW milling spindle, a 9kW C-axis drive, and 7kW drives for the X and Z axes. Furthermore, there is a 24-tool ATC — 12 positions for turning tools and 12 for milling tools.”
The two machines were supplied by both manufacturers’ exclusive UK and Ireland agent — Sheffield-based TW Ward CNC Machinery Ltd (Ward CNC —
www.wardcnc.com).
Adjacent to these machines — housed in its own clean-room — is a large-capacity co-ordinate measuring machine. This facility is complemented by TPG’s other manufacturing services, which include fabrication and welding, as well as assembly.
Mr Sadler says: “With these new machines, we are moving forward in two ways: existing work can be elevated to higher levels of quality, due to the accuracies and tolerances that are achievable; while the machines’ expansive work envelopes enable us to accommodate additional, larger workpieces.”
New challenge
With extensive experience in aerospace manufacturing and aerospace design engineering, Mr Sadler joined TPG with the remit to “elevate the company’s capabilities to include the efficient machining of large and often complex workpieces in difficult-to-machine materials — to high levels of accuracy.
TPG has an established history in the oil and gas industries and was ready to progress — and not just with existing customers. The company was aiming to become a major player in the nuclear sector for large-capacity machining.”
TPG worked closely with the Nuclear AMRC, which advised the company on the type of machines best suited to its requirements, after being presented with specifications for a series of typical parts that required vertical turning, milling and boring.

For maximum flexibility, two separate machines were suggested — a VTL and a mill-bore centre.
Mr Sadler said: “The new machines and the Nuclear AMRC have also provided us with new lessons in tooling and machining methods — plus creative process solutions.
“On certain components — and depending on material type and thickness — we are using speeds and feeds that are different to our norm; in some cases, we are drilling depths up to 14-times diameter rather than our traditional eight-times — and still maintaining the required accuracies.
“Moreover, both machines feature high-pressure coolant — at 70 bar.
“The new machines are also encouraging us to look at the complete manufacturing process and effectively re-define how we manufacture tube sheets.
“The first use of these machines was on the company’s new two-year £1.5 million contract with GE Oil & Gas.”
In conclusion, Mr Sadler said that the aim of TPG’s advanced manufacturing centre is to “differentiate ourselves” by establishing a facility that enables even the most complex heavyweight components to be produced quickly, while meeting demanding safety and quality standards.
“These components will, by their nature, be processed in small batches, and we are uniquely positioned to be able to handle these in the most efficient way.
“Our investment in the advanced manufacturing centre effectively future-proofs what we are doing.”