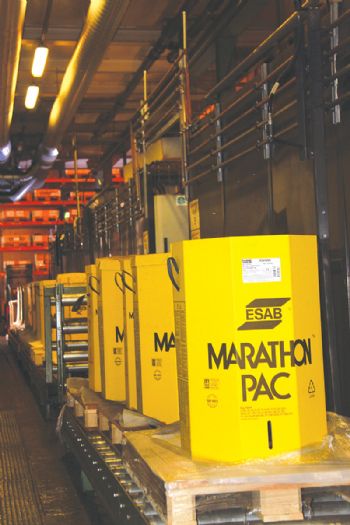
Kverneland Group is a leading international developer, manufacturer and distributor of agricultural machinery and services.
At its factory in Klepp (Norway), the company produces ploughs that are renowned for their longevity, thanks largely to the steels that it uses and the company’s in-house hardening processes.
‘State of the art’ automation ensures that productivity is high, and Kverneland (
www.kvernelandgroup.com) continually invests to ensure that it remains a world leader in plough production.
One recent development has been an upgrade for six robotic welding cells to use Esab’s ‘endless wire,’ which has resulted in improved productivity and significant cost savings.
The six welding cells are now consuming Esab’s (
www.esab.com) Filarc PZ6105R 1.4mm welding wire at a combined rate of 120 tonnes per year; previously, Kverneland was using Esab’s Marathon Pac bulk drums of welding wire, which contain far more wire than conventional spools.
However, the recently added ‘endless’ technology features a portable butt-welding device to join the end of one Marathon Pac drum to the start of the next, so the robotic welding operation is never interrupted.
Kverneland can now leave the robot cells running unattended overnight, which is saving the company up to £15,000 per year.
Furthermore, Kverneland no longer has to scrap the wire at the end of the Marathon Pac, which it previously had to do sometimes in order to avoid the wire running out mid-weld; this elimination of waste results in another direct financial saving.
In another project to help maximise the productivity of its robot welding cells, Kverneland invited Esab’s Value Added Engineering (VAE) team to undertake a study.
Kverneland team leader Odd Lorentz Pettersen said: “The VAE team analysed the welding process for each segment of the welds and undertook tests at the Esab Process Centre in Gothenberg.
“They then made recommendations for the robot welding speeds, so that we could reduce the cycle time without compromising quality.
“All six robots are different, and they all perform slightly different welding operations, so the VAE team had to look in detail at all six robot cells. As a result, we are now making further savings of about £20,000 per year.”
Kjetil Hansen, a sales engineer with Esab Norway, said: “Kverneland is always interested in looking at new ways to do things, so as to remain at the forefront of plough production, and our VAE project showed what can be achieved when you take a fresh look at an automated or robotic welding operation that you think is already efficient.
“We will continue to work closely with Kverneland to ensure that their welding equipment, consumables and processes are optimised for their production requirements.”