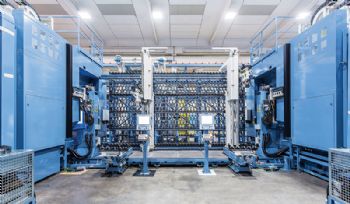
Italy-based machine tool manufacturer MCM SpA was established in 1978 in Piacenza — a historic machine tool manufacturing district in the Emilia Romagna region — and has rapidly built up an international reputation for its horizontal machining centres (HMC) and flexible manufacturing systems (FMS).
The company, which has around 2,500 machines out in the field, currently produces 80 machines a year and expects its workforce to grow to 370 by the end of the year (it was 331 at the end of 2018) — 18% of its staff work in the engineering department, designing tailor-made machining solutions for its customers.
MCM has three production sites in the Piacenza area, subsidiaries in Germany, France, the USA and China, and service partnerships in Spain, Russia, Poland and the UK, where the machines are available through the sole UK agent RK International Machine Tools Ltd (
www.rk-int.com), based in Erith.
Machinery Market was recently invited on a press tour of the company’s main factory to see the latest machining centres and FMS solutions being built and tested for customers in the aerospace, automotive and other industrial sectors. The core business of MCM is its flexible manufacturing systems, featuring high-performance and high-technology content based on MCM’s ‘state of the art’ four- and five-axis HMCs, which can be supplied in a multi-tasking configuration (milling, turning and grinding).
All the key components are based on the company’s exclusive designs and technologies, including the machine structures, spindles, rotary tables, tilting devices, working heads, tool management devices, coolant treatment units, tool and pallet-handling systems and the software control package.
The HMCs offer high rigidity, precision, reliability and the best-possible dynamic performance.
MCM is also renowned as a system integrator, configuring systems that are based on its own machining centres but can also encompass other makes of machine tools, automation systems and unconventional process technologies. Its complete and structured product line enables the customer to develop complex projects with just the one experienced and reliable partner, rather than trying to deal with a raft of different companies.
Four- or five-axis HMCsThere are four ranges in the MCM portfolio of horizontal machining centres: the Clock family, which has an X axis of 800-1,200mm, the Tank Family (1,300-1,600mm), the Tank G family (2,000-3,000mm) and the Jet Five family (3,000mm-plus). All these CNC machines are either four- or five-axis; they are available as stand-alone machining centres, bi-pallet, multi-pallet or FMS solutions. Bespoke systems and a wide choice of accessories are also available.
CEO Gian Luca Giovanelli said: “MCM doesn’t just sell machining centres to customers and walk away. We build relationships and work closely with them to provide an FMS to meet their needs; we also remain committed to helping them to improve their production processes in the longer term. This is why we have many OEM companies in the aerospace, automotive and energy sectors work with us, including leading names such as Airbus, Safran, Leonardo, GE, Siemens AG, Areva and FCA.”
MCM designs, builds and optimises all the main components installed on its machining centres and FMS, so it is in complete control of all installations. This is particularly pertinent when it comes to customisations, reconfigurations and maintenance of its products. The company also offers a direct after-sales service on all its machines.
Engineers can perform effective problem-solving by using a wide range of operating tools, including remote diagnostics from its base in Italy. MCM is also one of the most active European machine tool manufacturers when it comes to R&D — collaborating with universities and research institutes — and it has several patents to its name. The company manufactured its first machining centre, named Progress, in 1979; this was equipped with a horizontal spindle and a wheel tool changer.
It was followed in 1982 by the launch of the Connection, a horizontal machining centre with a built-in four-position multi-pallet system and a wheel tool magazine with tool-holders arranged in two concentric circles. It had a numerical control based on an industrial PC and achieved great success — over 600 machines were installed in a variety of industries during the next decade.
The company designed its first major FMS in 1985; this was for Lucas Girling in the UK, for the manufacture of braking systems. It consisted of 10 machining centres connected in-line by automation elements — and the first supervisory software applied to the production line based on MCM technology.
This led to the establishment of MCE, the IT division of MCM, in order to develop ‘jFMX’ software solutions dedicated to the management of complex manufacturing plants. The jFMX architecture is structured in such a way that it can manage growing plants and complexities up to the co-ordination and centralised management of an entire workshop.
In 1993, MCM unveiled its ground-breaking Clock HP machining centre, which featured a 20,000rpm HSK-63 high-speed milling spindle and fast tool change (less than 1sec). This machine became the new standard of the MCM range and led to the installation of an FMS the following year (at VM Motori) consisting of four machining centres, complete with automation and served by synchronised gantry robots for workpiece loading and unloading. It also featured workpiece feeding via a continuous roller conveyor.
This was followed in 1995 by the first aerospace order — Dassault Aviation chose an FMS consisting of four five-axis Clock 900 Mirror machining cells. The first order from Safran was placed in 1998, for the production of turbine blades by two Clock bi-pallet machining centres.
A five-axis version of the Action machining centre, with tilting head, was launched in 2001, along with a Jet Five family of machines (with linear motors) for the machining of large structural parts, in both titanium and light alloys; this family has proved to be very popular in the aerospace sector.
The first Tank 1300 machining centre was unveiled in 2003, and a version with new size frames and a 1,300-2,600mm X axis joined the range in 2005. MTU Aero Engines received the first Tank 1300 multi-tasking machining centres three years later. 2012 saw the debut of both the five- and six-axis Clock Dynamic machining centres; available in multi-tasking format, these are particularly suitable for the manufacture of small- and medium-size components with complex geometries, such as blades for gas turbines.
The company was acquired by the China-based RIFA Group in 2014 and, while still maintaining full independence, has undergone a period of rapid growth over the past four years, with a projected turnover of 110 million euros expected in 2019 (101 million euros in 2018).
The Clock family of machining centres (800 and 1200) was renewed last year, and MCM has strengthened its presence in the Chinese market by winning an important order from AVIC (Aviation Industry Corporation of China) consisting of 10 Tank 1900s in FMS configuration (mainly for the machining of aluminium alloys) and three Jet Fives (for titanium).
Among the highlights of 2019 so far has been an order from a leading Spanish aerospace company for a custom-designed multi-tasking milling/grinding centre in an FMS configuration containing rails, robot arm on the shuttle, loading/unloading stations, pallet stocking units, EDM machines, washing station and robot-deburring cell (provided by a third-party manufacturer).
A Clock 800 has also been sold to an Italian company that specialises in designing and building machines and making precision components. This is a high-quality small-medium machining centre targeted at sub-contractors that require high flexibility and autonomy of production, especially when machines are configured in multi-pallet or FMS solutions. It has a tilting table and a multi-pallet-10 system consisting of a carousel with seven-pallet stocking units plus one loading/unloading station and a two-position pallet changer.
MCM has also designed a 70 x 15m system for Europe’s largest aircraft manufacturer; it comprises six Jet Five machining centres with 18 pallets, two loading/unloading stations and 10 pallet-stocking units. The FMS will produce structural aircraft parts in titanium alloys. It is a highly customised solution, making full use of the available space — for instance, the tool magazines are positioned on the roof of the machines to save space.
The plant also incorporates sensors and big data analytics principles so the status of the machines can be monitored in real time, with possible degeneration of machine components predicted and down-time avoided. A five-axis Tank 1900 with FMS automation composed of six stocking units for pallets organised in two levels and one loading/unloading station for operators has been sold to France’s leading aircraft parts (structures, engines and landing gear) manufacturer.
A Tank 1900 five-axis multi-pallet-6 has been supplied to a joint venture between a major French aircraft equipment producer and a major aircraft engine manufacturer in the UK. This machine has a tilting head and is equipped with an 18,000rev/min spindle; it was supplied as a turn-key package. The aim of the investment is to optimise the machining strategy for an aircraft engine gearbox.
Modular approachFinally, a five-axis Tank 1300 FMS has been supplied to one of Italy’s major car manufacturers. It is the 21st machine delivered to this customer and completes a line-up of three Tank 1300s in an FMS. This is possible due to the modular approach of the investment; the pre-existing MCM FMS line could be easily improved and enlarged because MCM is the ‘unique’ partner at the factory and has control of the project (with the customer).
MCM is also intending to open a new facility nearer Piacenza in 2019; this will be more accessible for potential customers to visit and see live demonstrations of the MCM machining centre and FMS solutions.
Simon Rood, RK director and general manager, said: “We already represent Robbi, Delta, Melchiorre and Comev in the UK, and we are very familiar with the Italian market. When the chance to represent MCM arose, we felt it was too good an opportunity to turn down. The move to automation in the UK is under way; MCM not only offers a range of high-quality horizontal machining centres, but the range of FMS solutions is also exceptional and can be totally reconfigured when the need arises.
“We feel that there is a significant opportunity here for UK companies to embrace automation and future-proof their productivity levels in the rapidly evolving global market-place. No manufacturing company can afford to be left behind, and MCM can provide a solution for all businesses — big or small.”
From bi-planes to the F-35Italy-based Secondo Mona is a long-standing customer of MCM; it is now run by the fourth generation of the family that established the company in 1903 to sell and repair motorcycles and bicycles. The company is located in Somma Lombardo, very close to Malpensa Airport; its founder (Secondo Mona) was fascinated by the first bi-plane flights from the airport and decided to offer his engineering skills to the fledgling aero-engine industry.
Fast-forward 116 years, and the company now designs and develops fuel systems and equipment, engine equipment, electromechanical actuators, hydraulic manifolds and actuators — all exported world-wide to civil and military aircraft companies, rotorcraft and (more recently) UAV manufacturers. Secondo Mona also manufactures landing gear equipment and complex high-precision ‘make-to-print’ components or sub-assemblies for major aircraft or aircraft engine systems.
Its extensive production facilities benefit from a full range of ‘state of the art’ multi-pallet machining centres, fully equipped laboratories and NADCAP-certified special processes for surface and heat treatment. The company offers a rapid prototyping service, mechanical design, CFD analysis, development and qualification testing. It also offers electronic design and development and has a dedicated test capability.
Throughout its history Secondo Mona has maintained a policy of investing in the latest machines and technologies; since the early 2000s, it has been a key partner to MCM, investing in five HMCs with different levels of automation. The company currently has six machines in operation, including a Clock 700 multi-pallet horizontal machining centre that it purchased in 2005. This was quickly followed by a Clock 12000 MP10 in 2006 and a five-axis Concept 600 MP18 in 2008.
The company then invested in a Clock 1200 MP18 in 2013, a five-axis Concept 600 MP18 and a Tank 1300 TH Mirror FMS in 2015. The Mirror FMS consists of two machining centres with X/Y/Z axes of 1,300/1,400/1,400mm and a continuous tilting head (torque motor), HSK-A100 spindle (18,000rev/min), and a Fanuc 31i-B5 CNC.
The two mirrored machines can share 599 HSK-tools between them, and there is a shuttle pallet system on two levels for up to 28 pallets. The FMS also has two loading/unloading stations and is controlled by MCM’s jFMX supervisory software. Once the pallets are loaded, the FMS needs very limited operator intervention; it can be left to run for weeks at a time.