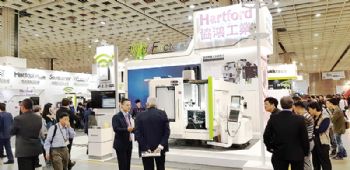
The 2017 Timtos was hailed a resounding success, smashing all previous records, but when the 2019 show ended on 9 March, the organisers — Taiwan External Trade Development Council (TAITRA) and Taiwan Association of Machinery Industry (TAMI) — were able to confirm that records had been broken yet again. This success was helped in no small part by the opening of a new hall (known as TaiNEX 2) that makes the Taipei Nangang Exhibition Centre the largest exhibition venue in Taiwan.
The 1,230 exhibitors from home and abroad (1,100 in 2017) occupied some 7,000 booths (5430 in 2017) and attracted 53,777 visitors overall.
Of these, 7,511 were from overseas (an increase of 2.3% on the 2017 show), with the top 10 countries being China (1,652), Japan (754), India (538), Malaysia, South Korea, Thailand, the USA, Russia, Singapore and Turkey.
In addition to attracting visitors, the show also generated significant amounts of business. Chin Fong — which was demonstrating an ‘intelligent’ metal-forming production line with integrated robotic arms, a ‘cloud platform’ and remote monitoring — had received orders for 20 machines by the end of the fourth day of the six-day show, along with serious enquiries from potential customers based in Vietnam, India, Egypt, South Africa, Switzerland, Brazil and Japan.
Meanwhile, the Taiwanese press manufacturer SEYI, which unveiled a number of presses targeted at the automotive market, “made contact with buyers from all continents” and received 20% more enquiries than two years ago, while EDM manufacturer Excetek received orders for more than 20 machines and enquiries from European, Indian and Malaysian buyers.
The show was particularly popular with overseas buyers, with one from Portugal buying a five-axis machining centre and 10 grinding machines, while a buyer from Belgium who has visited the last five
Timtos shows said 80% of the machines at his company were made in Taiwan.
Meanwhile, TAMI chairman Alex Ko emphasised the importance of the event as a place for recruiting the best talents, highlighting the fact that this year’s show attracted 7,200 students from 53 schools.
‘Smart manufacturing’
A first for this year’s
Timtos was the ‘AR Experience Zone’, which used augmented reality to demonstrate the structures of metal-forming machines and show how AR applications, together with production management systems and remote management, can be combined in the build of ‘smart’ production lines — coinciding with the show’s core theme of ‘Industry 4.0, Smart Manufacturing’.
Last year, TAMI published an Industry White Paper about smart machinery, its aim being for Taiwan to be the world’s capital for producing smart machines.
Meanwhile, according to a four-volume report by HSRC — Global Industry 4.0 Market and Technologies 2018-2023 — the Industry 4.0 market is projected to reach $214 billion by 2023, dominated by global technology giants including Alphabet-Google, HP, Samsung, IBM, NEC and Microsoft.
Writing in one of the Timtos daily show reports, International Metalworking News for Asia said that “Industry 4.0 holds immense potential, with Smart factories allowing individual customer requirements to be met and even one-off items to be manufactured profitably; and with end-to-end transparency of the manufacturing process available, there is access to optimised decision making”.
As reported in
Machinery Market 24 January 2019, a ‘Smart Machinery Promotion Office’ was established in Taichung in 2017, to help Taiwanese companies with R&D in the technologies associated with digitalisation; this led to the forming of the ‘Intelligent Manufacturing Pilot Production Site’ (IMPPS) early last year, the aim being to demonstrate full-scale ‘intelligent’ manufacturing and to help industry make the transition to ‘smart machinery’.
IMPPS also has the ability to provide total solutions for machine design, process development and software systems — and it has an impressive line-up of international partners.
These include Dassault Systems, Siemens, Mitsubishi, Rockwell and Microsoft, which are showing their latest technologies at the facility and using it as a base to “collaborate on total solutions for industry”.
Intelligent manufacturing
At
Timtos, Taiwan Takisawa highlighted TiMES (Takisawa intelligent manufacturing execution system), which it is using to co-ordinate its entire production process, as well as quality and inspection. The company says it has “digitalised every process in order to maintain a transparent factory and allow for each detail to be traced and optimised. This includes the progress of orders, storage in the factory and minimising preparation time before manufacturing”.
YCM (Yeong Chin Machinery Industries Co Ltd) — represented in the UK by Yeovil-based YMT Ltd (
www.ymtltd.co.uk) — also reflected the exhibition theme of smart manufacturing with i-Direct, its latest IoT solution.
This is designed to connect all factory equipment — including CNC systems, machines and even manually operated equipment — to provide real-time analysis of “live data from the production environment”.
YCM says this system allows plant managers to track production status, manage factory utilisation and monitor overall equipment effectiveness — plus identify bottlenecks and continuously improve productivity. Like many Taiwanese machine tool and equipment manufacturers YCM has also been developing ‘intelligent functions’ in its machines “to optimise the performance and life of the equipment”.
For example, ‘intelligent’ spindles and drive systems are designed to automatically enhance machining time while minimising machine vibration and thereby achieve the best surface finish and tool life. Such intelligent functions will also monitor ‘machine health’ to allow for scheduled maintenance and prevent sudden equipment failure.
Industry 4.0 — along with ‘Machine Intelligence and AIoT’, Additive Manufacturing, ‘Innovation in Aerospace Manufacturing’ and ‘Automotive Manufacturing Revolution’ — was also one of the themes at the Timtos Summit.
This saw top executives from the likes of ABB, Airbus, Bosch Rexroth, Dassault Systemes and DMG Mori offer insights into the latest trends and technology development.
For example, when discussing automotive automation, ABB’s regional manager said that intelligent manufacturing is not replacing employees but solving problems on production lines, automating repetitive actions and allowing employees to no longer only repeat ‘mechanised actions’.
Industry data
Speaking about Taiwan’s machine tool industry, TAMI chairman Alex Ko said that since more than 70% of the country’s machine tool products are exported (these exports amounted to a shade more than $3,656.106 million in 2018, up 9.50% on 2017), the industry is “reliant on the global economy.
“Capital expenditure has tightened since the fourth quarter of last year, and the trade dispute between the USA and China — along with the effects of Brexit — is holding back the economy; and while the second half of 2019 is looking more promising than the first, the trade dispute heightens the need for companies to set up second production locations abroad, especially in light of the business opportunities in Vietnam and India.
“We expect the show to generate orders worth about $1.6 billion this year; and with a favourable second half to the year, we expect the industry to achieve an overall annual growth of 5-10%.
“Furthermore, in response to the ever-changing global economy, we expect that the government will protect the export of Taiwan machines; we also hope that the Central Bank will activate the defensive depreciation mechanism to avoid the impact that the Taiwan dollar exchange rate has on machine exports — and that the government can create a category for machinery that will allow relevant companies to be listed on the stock market.
“Meanwhile, we expect that the Legislative Yuan will pass the draft revision of ‘industry innovation regulation’ and include ‘smart’ machines under the items qualifying for investment tax credit, and thereby help industry to increase its competitiveness.”
In 2018, China remained Taiwan’s largest export market, with a value of $1,154.886 million, followed by the USA ($477.865 million), Turkey ($159.157 million) and India ($158.042 million).
Vietnam and Germany were seventh and eighth in the rankings; the UK was fifteenth ($62.549 million).
Highlighting ‘excellence’
The 14th Taiwan Machine Tool Industry Awards, for which there were 43 entries this year, also echoed the
Timtos theme of Industry 4.0 and Smart Manufacturing with a category specifically configured to reflect this — ‘Intelligent machine tools or key components for all CNC machine tools’.
The special award in this category was won by YCM for its UX500P five-axis mill/turn machining centre with APC — a machine designed to meet the high-accuracy requirements of aerospace applications.
With high levels of rigidity and torque, it can machine heat-resistant metals such as titanium and Inconel while increasing tool life.
This machine also features the company’s latest iPros MX ‘intelligent’ CNC system, which includes ‘smart’ functions designed to automatically optimise machining efficiency, maximise tool life and monitor the machine’s ‘health’ in real time.
The company also won the Grand Champion Award in the Machining Centre category for its NFX800B-MPS Intelligent flexible machining system.
The Grand Champion Award in the CNC lathe category was won by Goodway Machine Corp for its GTW-1500 (turret/gang tool) multi-axis turning centre, while the Grand Champion Award in the Other NC Machine Tools category went to Ching Hung Machinery & Electric Industrial Co Ltd (CHMER) for its RV835L Intelligent linear-motor-drive wire-cut EDM.
CHMER also won the Supreme Excellence Award for its HD886L ‘high-speed milling compound EDM machine’.
Double-column machines
Being shown by Pinnacle — represented in the UK by Axe & Status, Milton Keynes (
www.axestatus.com) — was a DU1412 double-column machining centre.
Marketed in the UK under the Target brand, this five-axis machine features substantial Meehanite castings, X- and Y-axis strokes of 2,200 and 1,400mm respectively, a twin ballscrew drive (with double scales) for the Z axis, and heavy-duty roller-type linear guideways on the three linear axes.
Moreover, the main table has an integrated 1,200mm-diameter rotary table with a direct drive, a maximum rotational speed of 600rev/ min, a maximum load capacity of 3,000kg and a minimum indexing increment of 0.001deg.

The oil-cooled 45deg swivelling spindle head (-30deg/+180deg) features a direct-drive motor (19kW continuous/23kW at 60%), an HSK T63 tool interface, a maximum speed of 15,000rev/min, a maximum continuous torque of 93Nm and a minimum indexing increment of 0.001deg.
There is a 30-tool arm-type ATCas standard (options for up to 80 tools with a chain-type magazine), and control is via a Heidenhain TNC640 CNC system.
Pinnacle says the DU1412 has been designed for machining a wide range of complex parts in a variety of industries, including aerospace, shipbuilding, IC engine parts and precision moulds and dies.
Also showing a double-column machining centre was Kafo, which is represented in the UK by Rugby-based TDT Machine Tools Ltd (
www.tdt-machinetools.co.uk).
The PV-68 model being demonstrated features a stress-relieved cast thermo-symmetric structure designed (using finite element analysis) to optimise accuracy and avoid thermal deformation. The work envelope is 1,100 x 610 x 460mm, and the 1,250 x 610mm table has a maximum load capacity of 1,000kg.

As standard, the direct-drive 18.5kW BBT-40 spindle is rated at 15,000rev/min (20,000rev/min is available as an option); tool magazine capacities of 24, 30 or 32 are available. CNC systems from Siemens, Fanuc or Heidenhain can be specified.
New from Victor, which has a UK subsidiary in Rochdale (
www.victorcnc.com), was a five-axis machining centre featuring a roller cam mechanism for the swivelling trunnion and a 630 x 500mm rotary table.
The work envelope on the Vcenter AX630 is 700 x 500 x 500mm, the rapid-traverse rate for each of the linear axes is 48m/min, and the 11kW spindle has a maximum speed of 12,000rev/min (15,000rev/ min optional). Control is either a Fanuc 0i-MF or a Heidenhain TNC620.

Also new from Victor was the Vcenter-P76 with an auto pallet changer offering 720 x 400mm pallet capacity and a pallet exchange time of about 7sec (13sec chip to chip).
The machine itself has a work envelope of 760 x 500 x 510mm, an 11kW 12,000rev/min BBT-40 spindle (15,000rev/min is an option) and a maximum cutting feed rate of 20m/min.
Pallet changing
Automatic pallet changing was also a feature of the DMH-630 horizontal machining centre from Dah Lih, which is represented in the UK by Sheffield-based Ward Hi-Tech Ltd (
www.wardhitech.co.uk).
An upgraded variant of the DMH-500, this machine features a ‘high-performance’ BBT50 spindle, rapid-traverse rates of 40m/min (as opposed to 24m/min on earlier models), and a high-speed servo-driven pallet changer.
Ward Hi-Tech says the configuration of this machine as a moving-table type (rather than a moving-column type) means that some large parts — up to 1,200mm long — can be accommodated on the 630mm pallets. The control choice is Fanuc 31i or Fanuc OiMF.
Also new from Dah Lih was the DCMX5X-3228. A double-column moving-table machine with X- and Y-axis strokes of 3,200 and 2,800mm respectively, this offers a full five-axis machining capability via an 18,000rev/min HSK63 spindle unit with a ±100deg B axis and a ±220deg C axis. The show machine was controlled via a Heidenhain CNC system.
Other five-axis machines available in the UK via Ward Hi-Tech include those in the ASM/ASM-FD series from Taichung based Vision Wide Tech Co Ltd.
Available with single or twin pallets, these high-speed machines have been designed to offer high levels of precision and performance for both milling (ASM series) and mill-turning applications (ASM-FD series, with table speeds up to 350rev/min).
The work envelope is based on X-axis travels from 1,000 to 1,620mm, plus Y and Z travels of 1,260 and 1,050mm respectively; the rapid-traverse rate is 40m/min, and the maximum feed rate is 24m/min.

The spindles on ASM machines have an HSK-A100 interface, a 10,000rev/min maximum speed and a power rating of 57/75kW (S1/S6). The largest model in the range is available with a 7,000rev/min high-torque spindle.
ASM-FD models have an HSK-T100 spindle interface and power ratings of 42/53kW. Control is via a Heidenhain TNC640 CNC system with DCM (dynamic collision monitoring). A Siemens 840D SL controller is available as an option.
Another company focusing on five-axis machining — this time with a fixed-table twin-column travelling-gantry configuration (referred to as a box-in-box symmetrical design) and linear drives — was Ken Ichi Machine Co Ltd. There are three machines in its CompactB series: these have X-axis travels from 1,600 to 2,200mm; Y-axis (cross travels) from 2,500 to 3,200mm; a Z-axis travel of 1,250mm; and tables from 2,500 x 1,600mm to 3,200 x 2,200mm.
The maximum traverse rate for the three linear axes is 60m/min, with linear motor drives for the X and Y axes and a double ballscrew drive for the Z axis. There is an HSK A63 tool interface on the two smaller machines and an HSK A100 on the CompactB 3222.
Vertical grinding technology
The latest developments in vertical grinding technology were being shown by Palmary Machinery Co Ltd, which — like most Taiwanese machine tool manufacturers — is based in Taichung.
New is the company’s VIG-50, which features a vertical workpiece orientation and a ‘built-in type’ 15kW oil-cooled wheel spindle (2,700-15,000rev/min with HSK-E63 tool interface) that can be tilted to 22.5deg for end-face grinding applications. Also featured are an automatic tool change system (for up to six wheels) and an automatic dressing device.
Particular features of this machine include a honeycomb-style tubular-type machine bed and a cross-guideway structure (these have been designed to optimise both machine rigidity and stability), along with a coolant facility that is isolated from the machine bed so as to minimise the possibility of heat deformation.
Control is via a Fanuc CNC system that includes a gap control function, while options include a 500mm-diameter magnetic chuck, a hydrocyclone coolant separator and an oil cooler.