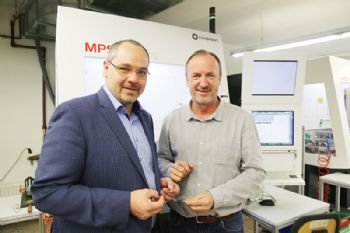
The Austrian premium eyewear manufacturer Silhouette International was founded in 1964 on the basis of a simple idea: glasses should not only be a practical visual aid but also “an accessory for better vision and appearance”.
This idea still drives the company, which has not been afraid to adopt new manufacturing technologies — including laser welding systems that allow it to produce particularly advanced designs.
Silhouette had a ‘groundbreaking’ year in 1999 with its 1.8gm Silhouette ‘Titan Minimal Art’ (TMA) — the first screw-less and hinge-less eyewear made of titanium.
It was an instant success, and to date more than 12 million have been sold world-wide.
Moreover, TMA was approved for space flights in 2000; the absence of screws and hinges minimises the risk of free-floating objects inside space helmets, breathing apparatus and within the spacecraft.
To date, the TMA has been used astronauts on over 30 space flights.
Since the introduction of the TMA, Silhouette has applied this same hinge-less approach to many other designs.
In terms of manufacturing technology, this drives several requirements.
First is the ability to join a variety of materials, including titanium and specialised alloys. Next is the ability to produce joints that are aesthetically pleasing and virtually invisible — and cannot be felt.
Finally, it also necessitates joints that give excellent flexibility and high strength — plus the ability to be cycled (folded and opened) numerous times without a change in shape or degradation in mechanical strength.
With these technical requirements in mind, Silhouette searched for a supplier that could support both the development of the manufacturing processes and provide the actual production equipment; and early on, the company decided that it would move from traditional resistance welding to laser welding, in order to meet stringent quality and throughput requirements.
During this search, Coherent emerged as a favourite among potential vendors for several reasons.
Coherent (
www.coherent.com), which is based in California and has offices world-wide (it is represented in the UK by GVUK Design Ltd), was one of the few companies that could readily supply the entire package — laser, all associated opto-mechanics, part handling and software.
From the outset, the company was also willing to participate in developing the process, lending its substantial laser expertise to a company that did not have much experience with the technology.
Prototype work
The first Coherent laser welding systems acquired by Silhouette were manual models used for prototype construction and repair work; the success of those led to the purchases of the Coherent MPS (Modular Processing System) Rotary for laser welding, adapted specifically to Silhouette’s needs.

The MPS Rotary is an automated turn-key system for metal welding, cutting and drilling; in Silhouette’s case, it incorporates a Coherent 200W fibre laser (StarFiber 200), plus a combination of scanner optics and travel that provide a variable working field.
The system is completely enclosed (Class I laser) for operator safety, and various options (including integrated machine vision) are available.
The system also features a rotary indexing table that allows part loading/unloading while processing is being performed.
Moreover, user-friendly software allows the system to be used by unskilled operators with a minimum of training.
For example, the system automatically detects the type of part that has been loaded and then calls up the correct processing program.
Silhouette engineers typically change job parameters on a daily basis to support their specific production requirements, and the MPS Rotary software has proven responsive enough to support this schedule.
Silhouette runs the system five days a week, two shifts a day.
The move from resistance welding to laser welding has been a tremendous success for Silhouette, delivering an overall cost saving of about 80%; laser welding has also proven to be better suited to automation — and has delivered a substantial increase in production throughput (part of this is due to shorter set-up times).
Overall, the Coherent MPS Rotary has reduced tooling and manufacturing costs, because multiple process steps are now performed in one machine, resulting in improved energy savings, sustainability, and productivity — plus the quality of the welds is superior (the welded parts themselves demonstrate high strength due to lower heat input into the part, and the elasticity of the welded joint is better).
Design flexibility
David Illitz, process manager (raw-part production), said: “While we are always striving to produce more unique and fashionable designs, wearer comfort remains a top priority.
“This creates engineering challenges for us in terms of material limitations. Laser welding, which delivers highly precise and very repeatable results, has been a key factor in enabling us to bring cutting-edge designs into production successfully.
“Furthermore, the flexibility of laser processing gives us confidence that we will be able to keep using this approach for many years to come.”
The MPS Rotary also includes Coherent’s SmartWeld technology.
This incorporates what the company refers to as ‘beam wobble’ — rapid motion of the beam during the welding process.

Instead of simply moving along a weld seam, the beam may ‘trace out’ circular, elliptical or even zig-zag patterns, executing motion both along and perpendicular to the weld seam, resulting in a higher-quality and more reproducible weld because the beam motion enables more flexible and precise control of the heat distribution produced by the laser.
For example, a relatively large SmartWeld pattern can be used to pre-heat the material before it is completely liquified, or to cool it down slowly after melting.
The former can prevent bubbling and turbulence in the melt pool, which produce spatter and inconsistent results, while the latter can eliminate cracking as the material cools.
SmartWeld can also be used to alter the normal ‘Gaussian distribution’ (highly peaked in the centre) of the applied laser energy.
Reducing the effective intensity at the centre of the laser pattern can reduce melt-pool turbulence by allowing ‘vapour expansion’ to occur in a more controlled manner, again leading to improved process consistency.
Another benefit of SmartWeld is that it allows bridging of larger gap widths in the welded parts.
This reduces fit-up tolerance, which speeds up production and lowers costs.
Mr Illitz added: “Silhouette currently produces about 2.2 million glasses per year.
“We need production equipment that not only supports this volume but also delivers the quality we need in a way that still keeps us cost-competitive — plus our production methods must be flexible enough to support a rapid and relentless design cycle that is a prerequisite to maintaining market success in any type of wearable fashion.
“The MPS Rotary has proven itself capable on all these fronts.”