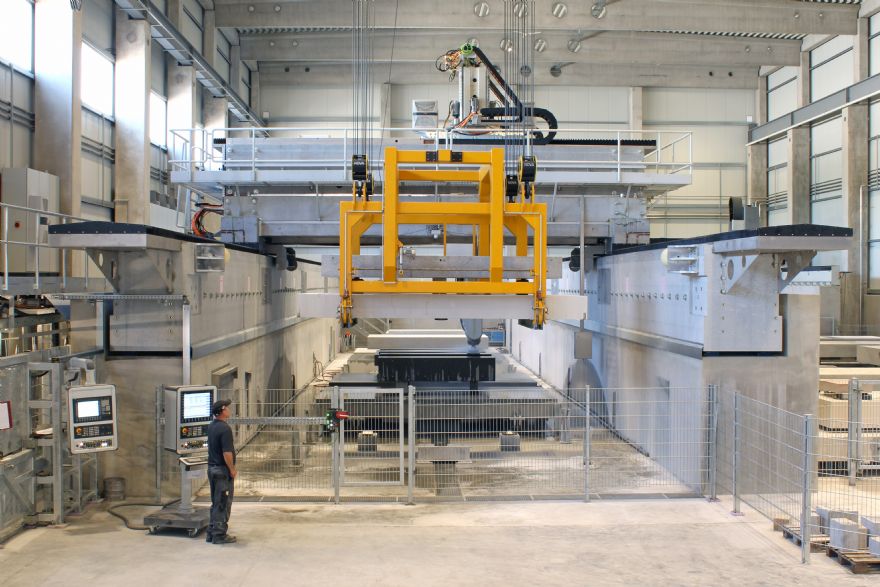
Germany-based
Reitz Natursteintechnik KG which has a facility in Asslar, Hesse, and employs around 140 people, can trace it origins back to 1946, when Herrmann Reitz began extracting raw stone from his own quarry. When his son Friedel Reitz joined the company, gravestone production was started in 1958 and continued from 1984 with third-generation family member Egbert Reitz.
However, it was industry’s introduction of granite surface plates that fundamentally changed the business model and led to the founding of
E Reitz Natursteintechnik eK in 1986. Today, Christopher Reitz, the fourth generation and current managing director, is furthering the development of the company and its products.
Christopher Reitz said: “Today’s machine components from Reitz combine the million-year-old material stone with cutting-edge technology. For over 35 years, we have been manufacturing precision components from granite and offering not only system assembly but also custom solutions and complete systems — all from a single source, from idea to commissioning. Our customers are mainly from the semiconductor, optics, general mechanical engineering, automation, metrology, printing, and medical technology sectors.
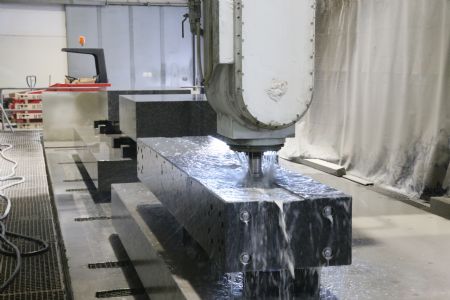
“We have been experts in processing natural hard stone for over 60 years, and it is a tradition that we are proud of and feel committed to. In mechanical engineering, especially in machine tool construction, achieving top precision and performance is essential for staying competitive, and it is here that machine beds play a key role.
“Due to its physical properties, granite offers clear advantages that neither steel nor mineral casting can match, namely intrinsic stability, temperature resistance, vibration damping, and guidance accuracy. Hence, granite the ideal material for precision machines and is widely used in measuring and test stands as well as coordinate measuring machines for components such as surface plates, tables, and machine frames.”
Mr Leitz said most of the company’ granite comes from South Africa, Spain, France, and Austria, delivered as pre-cut slabs or as raw blocks that are subsequently cut in-house. “The workpieces vary in size, although the largest we ever made was 13 x 1.5 x 1m and weighed about 65 tonnes; and to process such blocks precisely, we rely almost exclusively on machines developed and built in-house — four gantry-type milling machines and two five-axis gantry machines, all controlled by Siemens 840D CNC systems.”
Program simulationMr Leitz said that to ensure safe, fast, and precise granite machining, the company uses simulation software from
Vericut, which has subsidiaries worldwide. “Granite is a natural product, so the surface is never perfectly flat. To prevent tool collisions during processing, we developed a process with Vericut that virtually eliminates this risk.”
Stephan Meurisse, marketing manager at Vericut Deutschland, added: “Downtime, damaged tools, costly collisions, unusable parts, long setup times, wasted material all cost time and money. Vericut helps our customers avoid these time and cost traps. Vericut has been the industry leader in NC simulation, verification, and optimisation for all types of CNC machining, as well as additive and hybrid manufacturing, since 1988. The software eliminates the need for manual set up, saves valuable operator time, and protects machines.”
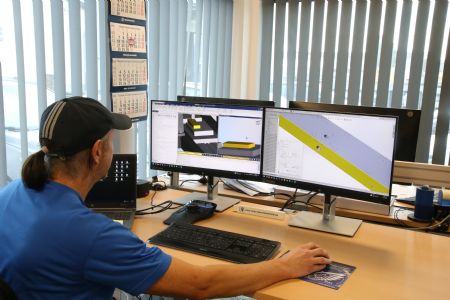
René Maschlanka, who is responsible for sales and project management at Reitz, said: “Granite blocks up to 13m long are typically delivered 3-5mm oversize. They are then machined to a flatness of 20 to 5µm; and since granite is very hard with a Mohs hardness 6 to 8, only 0.1mm of material can be removed per cut.
“After visual inspection, the operator selects a measurement point pattern, generating two automatic measurement programs in the CAM system. The first determines the block’s position, and the second maps its surface, both via probing cycles.
“The returned measurement points describe the actual surface condition, and from that data a machining program for a precise cuboid is automatically derived, then simulated in Vericut before execution. The finished cuboid is then drilled for guide rails, drives, spindles, sensors, and attachments; and after stainless steel thread inserts are glued in, the component is sent to the climate-controlled precision lab for final machining. These final programs are also validated with Vericut.”
Special CAMMr Maschlanka continued: “We use a special CAM system for granite processing, and we built the interface to Vericut ourselves. The system lets us precisely capture the position and shape of the workpiece and simulate automated steps without manual set up, while the simulation helps detect unnecessary movements, clamping errors, and wrong tool usage before they happen. Our programmers and operators are far more relaxed, knowing their programs will run safely, with no crashes.
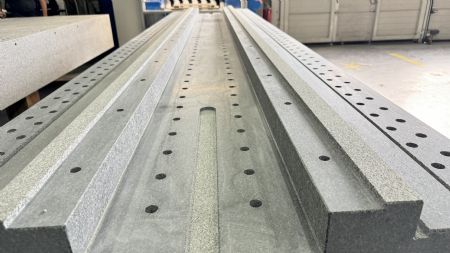
“Some machining processes at Reitz can take over 40hr; and while previously an operator had to stand by the entire time, they now run the simulation on a PC, press start, and only check in occasionally, with the integrated Vericut Reviewer showing us when that approach makes sense.”
Mr Meurisse added: “Vericut Reviewer allows users to interact with the simulation file, offering the ability to rotate, pan or zoom on any Windows PC or tablet, and thereby help build trust in new processes. Operators, shopfloor staff, or engineers can review simulations and confirm the project is correct before running it on the machine.”
Mr Maschlanka concluded: “Our staff love the Reviewer. It shows the full machining sequence, highlights critical steps, and helps with preparation like planning supports, tools, and clamping. Moreover, thanks to Vericut, tool breakage and collisions due to programming errors are a thing of the past at Reitz Natursteintechnik.”
Vericut’s Mr Meurisse added: “It was also an exciting and educational project for us. Normally, we work in metal machining, not granite, but this project shows how Vericut can safely and efficiently handle even multi-tonne granite blocks.”