
The most powerful flat-bed laser profiling centre to be installed in the UK is operating at ESP Laser Cutting, a sub-contractor that specialises in producing components from 3 x 1.5m sheet (up to 30mm thick) in a variety of materials.
The company’s purchase of this machine follows the development of a 12kW fibre laser source by Swiss manufacturer Bystronic (
www.bystronic.com), which has a UK subsidiary in Coventry.
ESP describes the productivity of the ByStar Fiber 3015, which was installed in April 2019 at its factory in Rotherham, as ‘remarkable’.
Delivering 20% more energy than the previous most powerful fibre laser (10kW), the new source was expected to be 20% faster at cutting, but ESP’s joint owners — Steve McMillan and Paul Short — say they are typically achieving a productivity increase of one third.
They attribute this partly to the higher power, but also to the design of the new cutting head — and a cutting plan algorithm running in Bystronic’s latest BySoft 7 nesting and control software.
This provides the most efficient route around the nest; it also minimises the risk of cut parts tilting, protruding from the material surface and interfering with the nozzle — thereby avoiding the need to use micro joints and saving even more time when the sheet exits the machine by making the ‘shake-out’ of the parts easier.
On one particular job (the profiling of chain links from 10mm mild-steel sheet), a three-fold increase in productivity was achieved by the 12kW machine.
When these parts were profiled on the ByStar Fiber 10kW machine (still in use at the Rotherham facility), 200 components per hour was the maximum output, as there was not sufficient laser power to use nitrogen as the assist gas.
Oxygen had to be used, requiring the cutting speed to be reduced to achieve an acceptable edge quality.
By contrast, the 12kW machine produces 600 parts per hour, as the higher power allows the use of nitrogen and hence full profiling speed.
There is the added advantage that the cut edges are better — especially on the under-side of the sheet — than when using oxygen, as nitrogen does not react with the sheet material.
ESP uses a profiling speed of 6.9m/min when producing the chain links, although the machine is capable of 150m/min on thin gauges.
An acceleration rate of 2.5g helps to minimise non-cutting time.
‘Early adopters’
Mr McMillan said: “We started ESP 25 years ago with a 1.2kW CO2 laser cutter, buying a second — a 1.5kW model — four years later.
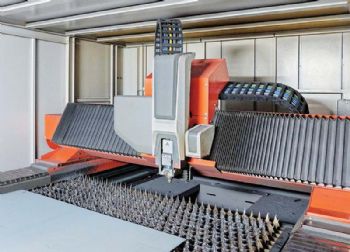
“We were early adopters of the technology and have been using it constantly over the years, witnessing its progression.
“During that time, we have repeatedly part-exchanged our two machines, buying a total of 10, of which the last eight were from Bystronic.
“The three most recent models have been fibre lasers, which have now almost completely replaced CO2 in our industry.
“We noticed a hike in productivity when the 6kW fibre arrived in 2013, and another when the 10kW version was installed three years later; it was the first in the UK.
“However, the 12kW laser cutter is the best machine ever.
“It is unbelievably quick, allowing us to make money even on jobs where we have had to pare back prices to win work — and we can guarantee short lead times as well.”
Mr Short added: “Every increase in power delivers a cleaner cut edge, especially on mild steel, which comprises the majority of our throughput.
“Furthermore, the BeamShaper function in BySoft 7 optimises the shape of the laser beam when cutting heavier-gauge materials on the 12kW machine and produces a finish that is ‘second to none’ on materials above 15mm thick.
“Fibre technology also reduces the running costs considerably, as there are no costly optics to replace; neither is there any need to spend a lot of time and money on maintaining a CO2 machine and its resonator.
“Furthermore, power consumption is dramatically reduced. In 2013, when we were running a 6kW CO2 machine alongside a fibre model of the same power, the former was drawing 100kVA, the latter 33kVA.
“Three years later when we went all fibre, we were saving £4,000 per quarter in electricity costs.
“It started to make a big difference to our profitability, as the cost of power comes straight off the margin you make on a job.”
Confirmed benefits
Both owners confirmed the traditionally quoted benefits of fibre laser cutting compared with CO
2, including three-times faster processing of thin material and an ability to process reflective metals like copper, brass and aluminium without back reflections causing damage to optics.
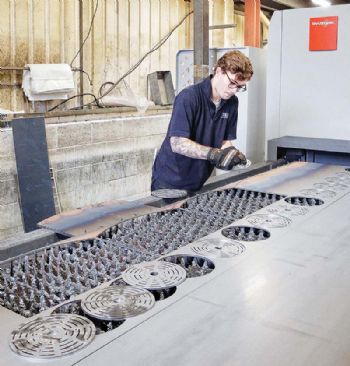
The accuracy of cut is down to ±0.1mm, and the laser power is ‘infinitely’ adjustable.
This means that, at one end of the scale, a 2mm-diameter hole can be pierced through 30mm-thick stainless steel, while at the other, thin materials can be engraved safely.
Summarising the impact that Bystronic equipment has made on their business, ESP’s owners say that back in the mid-90s, during what they term ‘phase one’, they bought two second-hand laser cutters to generate a profit and saved enough money to buy their first new Bystronic machine in 2001.
That was the start of ‘phase two’, moving them into the ‘top flight’ of laser cutting; this phase coincided with the move into the company’s current premises on the Centurion Business Park in Rotherham (double the size of the previous unit).
ESP now has 3,350 customers on its books, of which 1,800 are ‘active’ at any given time.
They span the catering, shopfitting, marine, electronics, aerospace, machine tool and defence sectors.
When asked what the future holds for ESP, they say: “It depends on what Bystronic introduces next.”