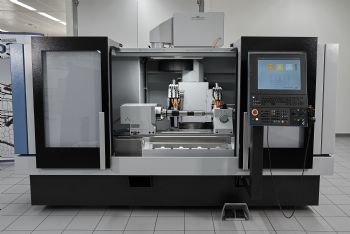
A new universal cylindrical-grinding machine from the Swiss company Kellenberger & Co has been designed to provide ‘excellent value at the entry level’ while offering reliability, precision and high productivity — plus intuitive programming capabilities.
Available in the UK from Rugby-based Jones & Shipman Hardinge Ltd (
www.jonesshipman.com), the Kellenberger 10 (K10) uses many components and sub-assemblies from the established K100 machine, coupled with the latest programming technology.
The Kellenberger Blue teach/programming software (accessed through a Fanuc
0i-TFP CNC system with a 19in touch-screen) enables semi-skilled operators to use the machine.
The standard machine can accommodate workpieces that are up to 1,000mm long x 400mm in diameter, with a maximum weight of 100kg.
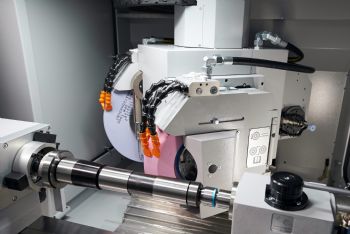
The table is also a proven Kellenberger design with the “full-length wheel-dressing interface located on its rear to reduce re-tooling work and extend the wheel dressing possibilities”.
The machine features X- and Z-axis strokes of 365mm and 1,150mm respectively, with low-maintenance high-precision linear guides on the X axis and V-flat sliding guides on the Z axis; both axes are equipped with optical absolute linear position measuring systems.
Meanwhile, the B axis is designed as an automatic indexing axis (1deg Hirth gearing) with a +30deg/-210deg swivel range.
The K10 allows users to greatly expand or customise its capabilities by offering a range of optional equipment, such as a second external grinding wheel, larger grinding wheels, a tailstock, gap control and balance sensors, as well as measurement control via probing.
For optimum productivity and flexibility, the universal grinding head can be equipped with two 500/400mm-diameter OD grinding wheels, while high-frequency grease-lubricated ID grinding spindles with direct drive are available in two speed ranges (6,000-40,000rev/min and 10,000-60,000rev/min).