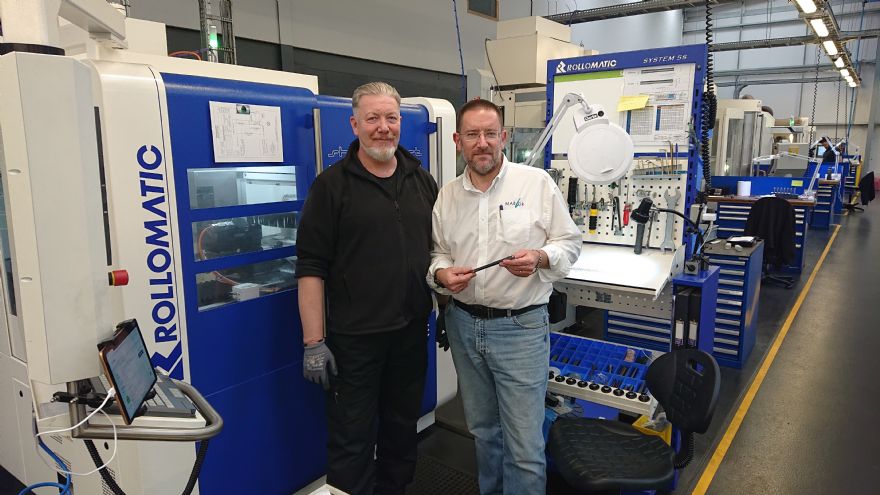
Peterborough-based
Marlor Tooling, a specialist in the design and manufacture of solid-carbide cutting tools that was established 50 years ago by George Taylor, has invested in a Rollomatic ShapeSmart NP3+ CNC tool-grinding machine. It was supplied by Coventry-based
Advanced Grinding Solutions (AGS).
Mr Taylor, who was an engineer at the nearby
Perkins Engines plant, saw an opportunity to offer a variety of sub-contract engineering services to the company, and a strong relationship developed — one that remains today.
Mr Taylor’s son Kevin started up the tool-manufacturing side of the business around 25 years ago; and while the company has since moved several times to larger units on the same industrial estate, the family ethos of continual investment in the latest technology remains the same today as it was 50 years ago.
Marlor now has a ‘state of the art’ production facility with 12 CNC tool-and-cutter grinders, along with various other CNC machines — including those for undertaking EDM, drilling and inspection work.
Moreover, the company is somewhat different to most UK tool manufacturers in that nearly all of its sales are to other tooling companies, with very few directly to end users.
Marlor’s works director Martyn Cross said that to overcome a production bottleneck the company looked at a number of CNC cylindrical grinding machines, but did not initially find one that suited its particular requirements with regard to producing cutting tool blanks efficiently — short set-up times and the flexibility to accommodate small to medium-size batches.
However, after seeing the ShapeSmart NP3+ when it was exhibited for the first time in the UK on the AGS stand at
MACH 2018 — followed by a later full demonstration, Mr Cross and his team decided that it was the best machine for their requirements and placed an order.
Marlor had initially considered the simplest machine configuration that would solve many of its manufacturing problems, but after seeing how quickly blanks could be programmed and ground after manual loading — or quickly set up for unmanned running with automatic loading — the company took a different approach.
Out went the initial plan of primarily manufacturing small batches of special blanks, to be replaced by looking at moving operations from other machines to maximise the use of the SharpSmart’s easy-to-set automatic loader for ‘lights out’ manufacturing and producing low-quantity special tools during the day.
Multiple benefitsMr Cross says that while the quality, surface finish and repeatability of parts produced on the Rollomatic machine are “second to none”, the extended wheel life and dressing frequencies have been “a revelation”.
Furthermore, cycle times have been dramatically reduced, with Marlor citing one example of a long through-coolant drill for an aerospace application that used to take 7min to manufacture but now takes just 2min.
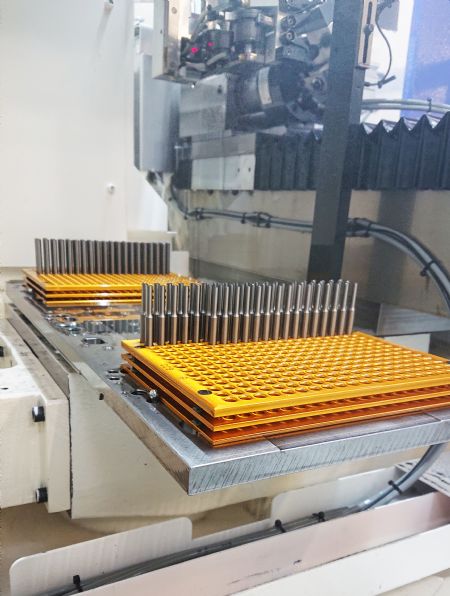
In quantifying improvements in quality, the company has found that the Rollomatic machine easily holds a tolerance of 3µm on diameter when producing even large batches of tools.
The difficulty of finding skilled engineers was another justification for Marlor purchasing the SharpSmart NP3+ machine.
Mr Cross said that after an operator who was unfamiliar with CNC grinding went to Rollomatic for training, he was using the intuitive Rollomatic P4Smart software to grind complex blanks — unassisted — within two weeks.
Rollomatic’s ShapeSmart machines are designed for grinding tool blanks and similar stepped cylindrical components using the method of peel grinding. This new generation of cylindrical grinders has been improved to offer fast set-ups and superior grinding quality — including both rough and finish grinding — in a single automatic operation for diameters up to 25mm.
A Renishaw probe handles length positioning, while a Marposs gauge is available for the post-process gauging of diameters, enabling tool concentricity of less than 0.001mm.
Mr Cross says that Marlor has come to rely on the Rollomatic machine in the months since it was installed, and adds that he cannot believe how the company had managed without one for so long.
“The three-year parts and labour guarantee, along with the excellent technical and service support, further confirm that we have bought the best grinding machine for our requirements.
“It has contributed to halving production lead times, allowed a rapid response for urgent jobs that need CNC cylindrical grinding and enabled us to bring the grinding of all tool blanks in-house.”