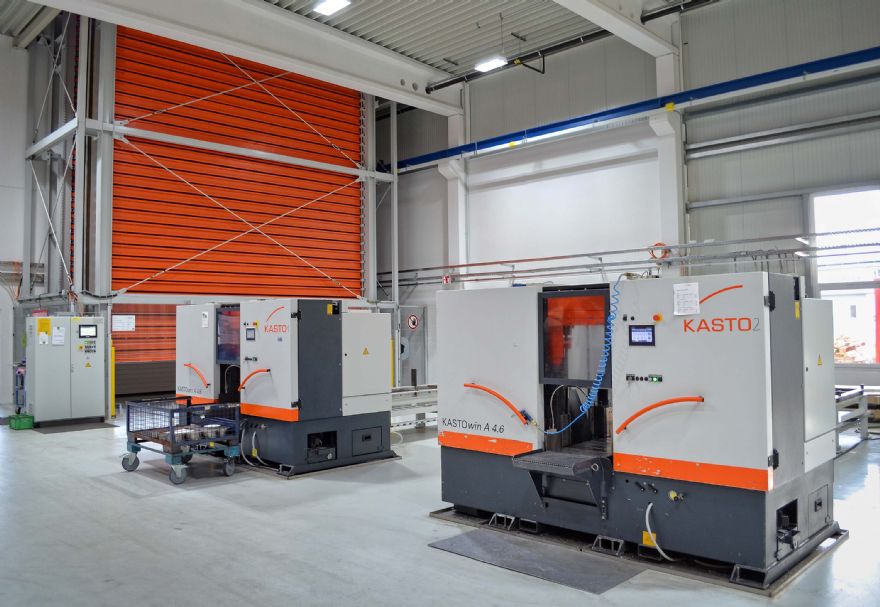
Bavaria-based contract machining firm Microart specialises in the production of components in small and large batches to very tight tolerances. The 25 five-axis machining centres and 14 turn-mill centres operate largely unmanned, 24/7 at the company’s facility in Roding, due to extensive use of automation and networking.
Founded in 2007, Microart has become one of Germany’s fastest-growing sub-contractors. It currently has 186 employees and an annual turnover of around €14 million.
Due to the high level of precision that needs to be achieved, much of the shop floor is temperature controlled. To ensure that billet material is supplied to the machine tools efficiently and at a constant temperature, the company has invested in a UNITOWER tower storage system and two automatic KASTOwin A 4.6 bandsaws from German manufacturer, Kasto.
All three are adjacent to one another at one end of the factory and the roller door through which new material arrives is carefully managed to ensure it is opened only when necessary and for the shortest possible time.
The cutting range of the saws is 460mm, large enough for most of the material machined by microart. The stock processed on the saws is stored in the 15.6m high tower, which has space for 100 cassettes that hold material up to 6.5m long.
Two types of cassette are used with heights of 160 and 300 mm. Up to 2.5 and 3 tonnes can be loaded into each cassette type respectively. The load carriers are handled by a storage and retrieval machine (SRM) to deliver stock to the operator at ground level. Access times are short and the handling of bulky materials is made easier.
Previously, Microart staff had to laboriously store and retrieve long goods manually, but now they only have to push a button. The SRM automatically finds the relevant storage location thanks to the KASTOlogic warehouse management system.
After employees receive order data, they call up the required material via a touch screen and the cassette is delivered to the retrieval station. The stock is then handled manually or with the assistance of an overhead crane onto the input conveyor of one of the saws.
Microart managing partner Dr Alexander Artmann said: “The tower storage system and two automatic bandsaws run very smoothly. These investments have enabled us to set important milestones with regard to our corporate goals of automation, productivity, flexibility and quality.”
Managing director Michael Kerscher added: “If there is a slight malfunction of the equipment, it is usually fixed easily and quickly by remote maintenance but if it is really necessary, a Kasto engineer arrives at our factory in next to no time.”