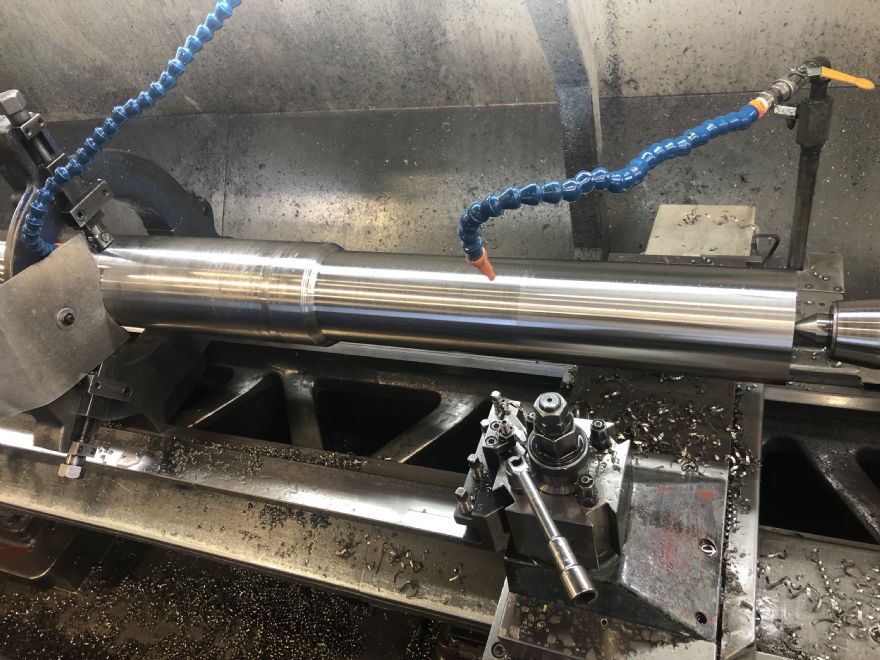
As a world leader in fluid engineering technology such as pumping, agitation, mixing, separation and application technologies,
Sulzer has a responsive network of 180 manufacturing facilities and service centres around the world.
With more than 25 service and manufacturing facilities in the UK; a reliable and reputable supply chain is critical for this OEM and service provider – and this is why Sulzer recently committed to a three-year contract with metalworking and MRO specialist
MSC Industrial Supply Co (MSC).
Driven by quality, innovation and continuous improvement, Sulzer made the bold move to change its supplier during the pandemic, and it was only a matter of weeks from signing the contract before MSC was identifying significant potential savings for Sulzer — a task it had to carry out ‘virtually’ due to the Covid-19 lockdown restrictions.
The initial phase of the contract will see MSC implement vending solutions into two of Sulzer’s largest UK manufacturing sites in Birmingham and Leeds with bespoke solutions being gradually introduced at Sulzer’s remaining UK sites.
The strategy of primarily focusing on the manufacturing sites is because this is where the most significant cost savings can be achieved through lean manufacturing and continuous process improvements.
During his initial and socially distanced site ‘walk-around’, MSC’s application engineer Stuart Wiezniak was introduced to the Sulzer Leeds machine shop and staff and the early conversations identified concerns over a new project that was turning a 4m long inconel shaft for a new high-pressure pump product line for heavy industrial applications such as the offshore industry.
Currently turning hundreds of 3 to 4m long Super Duplex shafts, the introduction of Inconel for a new product line raised concerns for Sulzer. With hundreds of shafts annually turned on its 1998 DSG and 1990s Harrison turning centre, Mr Wiezniak had few concerns over the performance of the machines.
“The older machines have construction and rigidity that far outweighs most modern machine tools, so we had the perfect foundation for trialling MSC’s extensive range of tools. We selected a couple of premium carbide grades for Inconel machining, achieving marginal gains on the speeds, feeds and overall cycle times. To attain the ‘step-change’ we really wanted, we knew we had to look at ceramic tooling.”
Paradigm shift in strategyWith the extensive range of Japanese ceramic cutting tools from NTK recently being added to the MSC range, Sulzer adopted a paradigm shift in strategy. For Sulzer, the concern around switching to ceramic tooling was the potential for additional heat and distortion.
The MSC engineer identified the need to change the machine coolant as well as the slide wipers on the lathe bed from nylon to steel to protect the machine bed from the increased swarf temperatures created from high-speed and feed turning.
“With the machine fully prepared for trials, we worked closely with NTK’s Application Engineer Glyn Shaw and Sulzer’s machine operator and programmer Jamie Fieldhouse — it was a genuine team effort to implement a complete shift in machining strategies.”
Despite the stable machine platform, the new coolant and the slide guarding, the trio of engineers realised that the steady rest on the DSG machine needed to be moved from an average distance of 1m from the cutting tool to 350mm, to increase the rigidity and stability for ceramic tooling, which is inherently more brittle and susceptible to vibration than its carbide counterparts.
With an initial batch of five Inconel 625 shafts to be machined from a raw 200mm diameter x 4m billet down to a range of stepped diameters from 100 to 180mm, the shafts required considerable material removal volumes.
Once the primary work of preparing the machine and the rough machining strategies had been achieved, the trials began. Rough machining the shafts to just leave +2mm for semi-finish turning, the best carbide turning results typically yielded a finish machining time of 14hr and 1 min.
This was done through varying strategies and trials that applied cutting depths from 1 to 3mm with cutting speeds of 40 to 50m/min and machining speeds of 80 to 200rev/min.
These times, like all other times recorded by MSC at Sulzer, account for ‘cutting-time only’ and do not include the additional reductions in set-ups and tool changes. Once the MSC, Sulzer and NTK engineers had done the groundwork, the trials began.
Mr Wiezniak explained: “Upon the recommendation of NTK’s Glyn Shaw, we selected the NTK’s Bidemic range of inserts and in particular the JX1 grade with a round RNMG12 insert geometry. This was because the new patented Bidemic range offers better wear and notching resistance compared to whisker ceramic grades that are widely used in the industry.”
“The NTK trials started at a cutting speed of 250m/min, but we found the optimal speed for this job at 370m/min, a massive increase from 40 to 50m/min with carbide. We also increased the spindle speed from 80 to 200rev/min to over 740 to 1,000rev/min depending upon the diameter being turned.
“Cutting with an average depth of 1.5 to 2mm, we reduced the rough machining time on the five Inconel 625 shafts from 14hr 1 min to 2hr 4min per shaft. This yielded a material removal rate (MMR) of 222cm
3/min up from the previous rate of 30cm
3/min. An unexpected benefit was the improved concentricity after releasing the steady rest.
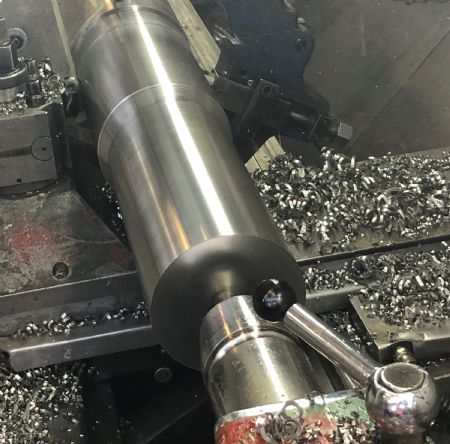
With carbide tools, the rollers were showing a run-out of up to +/-1mm, yet with the ceramic inserts that only increased workpiece temperature by 9°C during machining, the run-out was consistently between +/-0.15 to 0.20mm – not only alleviating Sulzer’s initial concerns on overheat but showing a performance and concentricity improvement.”
Aside from a nominal annual tooling cost increase of less than £1,000, the six-figure financial savings justify the tool cost increase.
Mr Wiezniak continued: “From discussions with Sulzer, it has already identified more than 170 forward orders for the next 12 months for this particular pump. Based on our accurate CAM and cutting tool data, we project that we will reduce annual machining costs by 85%, reduce machining times by 85% and reduce the cost per part by 8%.
“To qualify this, total cutting hours will fall from 2,380 per annum to less than 350 and this doesn’t include set-up and tool change reductions. This will yield a significant six-figure financial saving for Sulzer on the production of forward order Inconel 625 shafts and the respective pumps.”
With the groundwork and trials already successfully implemented on the Inconel parts, the cutting data has also been adapted for Sulzer’s Harrison large bed turning centre that presently has more than 100 Super Duplex shafts scheduled for production.
Mr Wiezniak added: “While Super Duplex has a somewhat different and softer composition than Inconel, it is still an extremely difficult material to machine. We have already started work on this and are fully confident that we will replicate the ‘seven-times’ overall cycle time reduction from the Inconel parts – doubling our already ‘fantastic’ results.”
Not stopping to appreciate the impressive results that it has already achieved at Sulzer, MSC has already identified further and potentially equally impressive savings on the same shafts on a third alternate machine. With the rough turned shafts finished to +0.3 to +0.5mm, the final process of grinding is conducted on an eight-tonne Churchill BX cylindrical grinding centre.
Mr Wiezniak concluded: “While we are optimising the turning process to minimise stock for finish grinding, we have identified potentially big savings with the grinding of the Inconel shafts. By introducing new grinding wheel technology with the help of Kim Dean from
Tyrolit, we can double the depth of cut from the existing 0.05mm to 0.1mm – effectively halving the 36hr cycle time.
“But taking this even further, we have also identified cycle time savings from reducing non-grinding times with the introduction of a secondary wheel dressing unit to reduce wheel traversing distances and dressing times.”