The Hurco machining centre on the shopfloor in StonehouseGloucestershire-based
de Havilland Engineering Group offers a comprehensive service for the supply of small to large metal fabrications. Due to the wide variety of work the company undertakes at its facility in Stonehouse, it is split into several divisions, allowing it to manufacture its own products in addition to providing a variety of sub-contract fabrication services.
Heavy fabrication contracts cover industry sectors including oil and gas, water, and site installations, as well as the marine engineering, aerospace, wind turbine, hydrogen generation and recycling industries. Separate departments cover fabrications for food processing, precision engineering and a number of safety products.
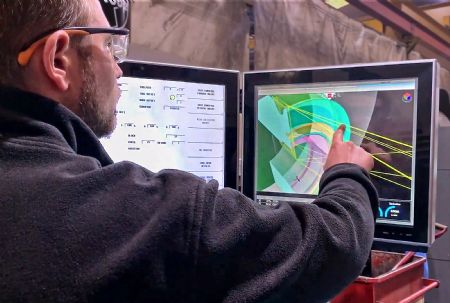
As a result, the range of materials processed is huge, from light plastics including PEEK, PTFE and acetal to cast iron and tough steels such as stainless and Super Duplex.
The latest investment in CNC metalworking capacity by de Havilland is a pair of machine tools from High Wycombe-based
Hurco Europe Ltd. First to arrive was a TM10i two-axis lathe with an 81mm spindle bore, fitted with a Hydrafeed MSV80 bar magazine. Maximum turning diameter and length are 450 and 760mm respectively.
Two weeks later it was followed by a VM20i three-axis vertical machining centre with a 1,016 x 508 x 508mm working volume. Both machines have a Windows-based control system with Max 5 conversational programming software.
Lewis Chandler, lead operator of the machines (pictured above programming the Hurco lathe at the Max 5 control), said: “The capacity of the machines is large considering their small footprint and the price point for what they are giving us has worked out really well. The conversational programming is very easy to use. It asks you what you want, you type in the figures and it draws it up for you automatically — it is brilliant.”
He added that most machining cycles at de Havilland Group are generated directly at the controls. In the past they used G-code programming, which requires a lot of calculations and long-hand typing and as a result it was becoming more and more difficult to recruit operators with the relevant experience.
Menu-driven programming and mobile phone-style manipulation of images on the touch screen, however, are intuitive for most people. Moreover, having a lathe and a mill with the same easy system for creating machining cycles makes training new operators much easier and they are able to swap seamlessly between machines. Programming is nearly all done at the controls, although a little is carried out off-line.
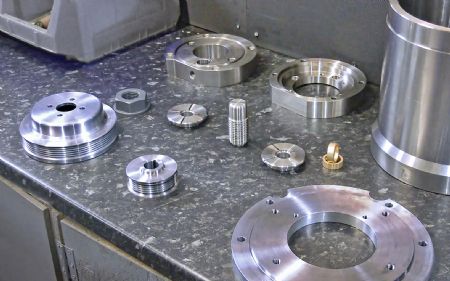
Mr Chandler concluded: “The machining centre has a 10,000rev/min, 15kW spindle, which is high for this size and class of machine and not very common unless you pay extra for it. It enables efficient machining of aluminium, plastics and lighter materials.
"In addition there is a lot of torque at the low end of the speed range, allowing us to tackle difficult materials such as tougher steels and Super Duplex productively. We occasionally push the machine quite hard and it always responds well.”