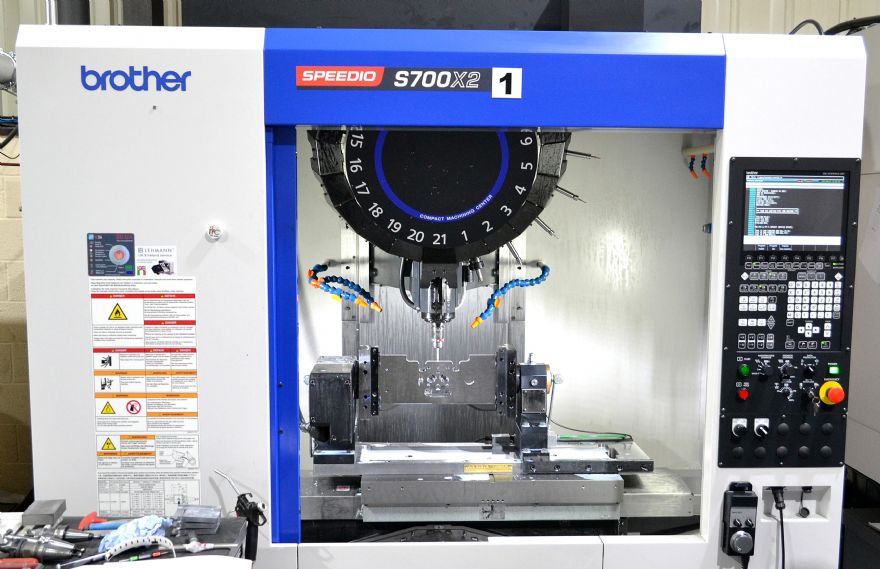
Established in 1947, Andover-based
MRT Castings specialises in the manufacture of high-quality aluminium die castings. In addition to regularly investing in the most up-to-date casting technologies, over the past 70 years the progressive family business has introduced a range of complementary end-to-end services.
Along with ‘state of the art’ high-pressure and gravity die casting, the company now provides first-class tool making, surface finishing, mechanical assembly as well as a comprehensive CNC machining capability.
The mainstay of MRT Castings’ impressive machining facility are its collection of highly efficient Brother CNC vertical machining centres (VMCs) supplied by
Whitehouse Machine Tools Ltd.
MRT’s policy of standardising on machines from a single supplier provides enhanced flexibility as both operators and products are interchangeable between machines. Additional benefits include the use of standardised fixturing, tooling and CNC rotary tables.
Having previously used two well-known brands of CNC rotary tables, following advice from Whitehouse Machine Tools, the company’s most recently installed Brother VMCs were specified with the addition of pl Lehmann CNC rotary tables.
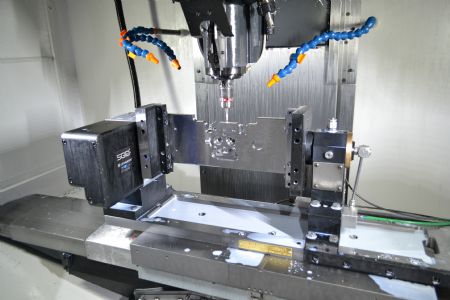
Phil Rawnson, MRT Castings managing director, said: “MRT Castings is able to support our customers from initial ideas, through product development and design for manufacture stages, to full production and logistics.
“Our extensive in-house CNC machining facilities are at the very core of our operations. To help ensure short lead times and the manufacture of premium quality products we use a range of Brother machine tools, the fastest machining centres available.
“Such is the quality and cost-effective nature of our CNC machining provision, in addition to machining die castings that are produced in our own foundry, we also machine components cast by other companies.
“As we usually perform small- to medium-size production runs on a diverse range of products, we need each of our machine tools to deliver the best possible levels of flexibility, we also strive to maximise machine utilisation times and to minimise set-up times. Over several years, our use of rotary tables has made important contributions in these areas.
“As many of the components we manufacture are relatively complex, without the use of rotary tables we would need to perform two or three different machining operations on them, rather than the ‘one-hit’ machining that we carry out.
Also, the ability to finish machine parts in a single cycle means that we don’t face the issues related to the accurate relocation of workpieces for subsequent machining operations.
“Over the past 12 months we have been involved in the casting and machining of critical parts that were urgently needed for medical ventilators. To enable us to keep pace with this extremely challenging production schedule we brought the planned purchase of six Brother VMCs forward — bringing our current Brother VMC count up to 25 machines.
“To provide highly efficient four-axis capabilities, each of our latest six Brother VMCs were specified with the addition of pl Lehmann CNC rotary tables.
“As the use of rotary tables and the fourth axis they deliver is central to our machining efficiencies and having previously used other brands, we were advised by Whitehouse Machine Tools to choose the Lehmann rotary tables which has provided us with a range of advantages.
“Despite our Lehmann rotary tables being extremely robust and able to perform all of the tasks we require, when compared to our previously used rotary tables, they are relatively small. Their reduced footprints mean that, when mounted inside our Brother vertical machining centres (VMCs) they take-up a minimum area.
“In addition to releasing machine bed space for other workholding, the reduced size of the CNC rotary tables means that when they are not required, they can often be left inside our VMCs when other machining jobs are being carried out.
“Additionally, the reduced height of the rotary tables helps to increase the available working volumes of our machines. In addition to benefitting from the quality of Lehmann’s products, we have received excellent installation and interface help from both Whitehouse Machine Tools and Lehmann’s UK service agent.”
Advanced productsLehmann has been involved in the design and manufacture of high-quality rotary tables for over four decades. The in-depth expertise gained throughout this time is reflected in the quality of the company’s advanced products. To help reduce parts and to enable the availability of Swiss quality at a cost-effective price, Lehman rotary tables are based on an innovative modular design system. This highly efficient arrangement enables a wide range of CNC rotary table options to be made available to meet customers’ diverse needs
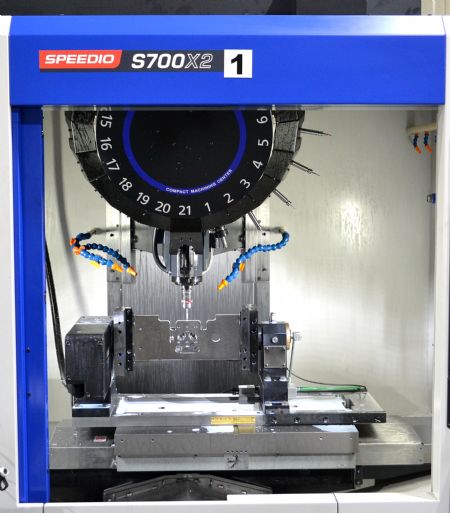
Four basic sizes are available — 507, 510, 520 and 530mm, with centre heights from 110 to 240mm. Due to the company’s modular design approach, from these size options it is possible to offer more than 170 different rotary table variants.
Models are available from basic single-spindle 4th axis units to 4-spindle tilting rotary tables with 4th and 5th axis capabilities. Now, rather than compromise and obtain a rotary table that represents a close-match to a machining requirement, Lehmann customers are able to take delivery of a high-quality CNC rotary table that exactly corresponds to their specific needs.
In addition, the company’s modular design system means that the purchase of a well-engineered CNC rotary table represents a safe, future-proof investment. For example, if a customer’s manufacturing requirements change, instead of investing in a new rotary table, their existing Lehmann CNC unit can be easily modified and adapt to changes of use.
A standardised spindle arrangement allows the use of an extremely wide range of workpiece clamping systems. As a result, in addition to standard workholding being set-up for an initial workpiece range, the system can be quickly converted to accommodate other workpieces.
Lehmann’s CNC heavy-duty CNC rotary tables have earned a global reputation for their outstanding performance, quality and longevity. Further aiding efficient, precision machining, the company’s robust products benefit from excellent clamping torque, load weight capabilities and accuracy specifications.