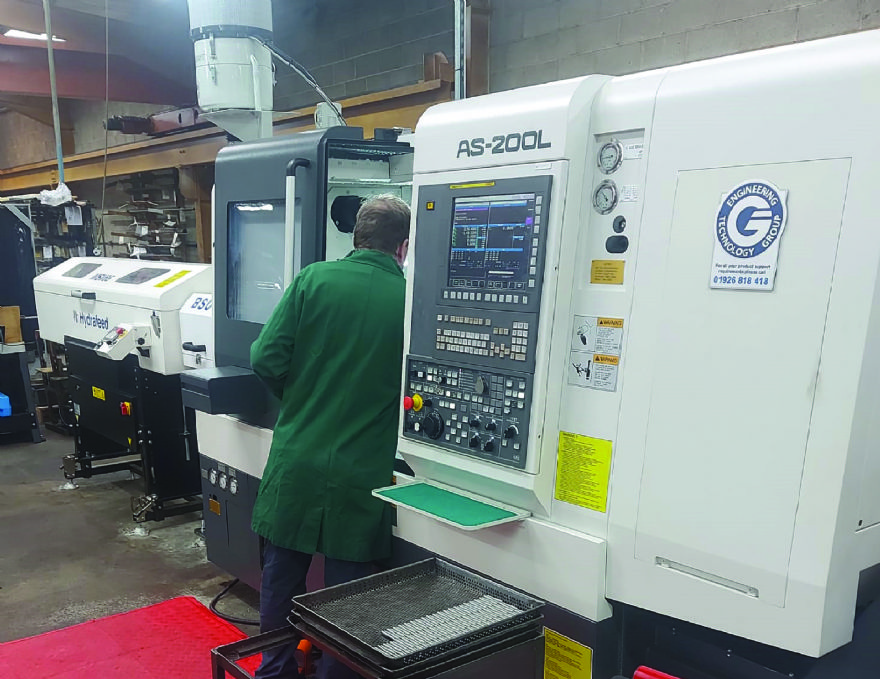
Founded over a hundred years ago, Blackburn-based
Dobson & Beaumont is a precision engineering sub-contractor with a distinct niche — the company is a specialist in thread rolling.
This process cold-forms screw threads to work harden them and optimise the grain flow, which improves the overall thread strength by more than 25% when compared to typical thread-cutting operations.
However, before the process can be undertaken, the company has to machine what are regarded as some of the most challenging materials — including titanium, Inconel, stainless steel, Super Duplex Stainless Steel and Durehete.
Richard Guest, Dobson & Beaumont managing director, said: “Like all sub-contract manufacturers, we were impacted by the pandemic. Fortunately, our niche offering sees our business work for a wide variety of industry sectors, including fasteners, pump and flow control, automotive, motor-sport, oil and gas, petrochemical, marine and defence, sub-sea, wind energy and aerospace. As a result we were not heavily impacted by one particular industry segment.
“That said, the pandemic did allow us to review our processes and ageing plant list and instigate a plan for investing in new technology. We machine a lot of parts in batches that can vary from as few as four to 100-off and more; and because our turning centres were all single-spindle machines, most of our turned parts required secondary operations.
“We knew we needed a twin-spindle turning centre to reduce secondary operations; and following a comprehensive review of the market, a Nakamura-Tome AS200 twin-spindle turning centre was deemed the perfect choice.”
Supplied by Wellesbourne-based
www.engtechgroup.com Engineering Technology Group (ETG), the AS200 uses the same Fanuc programming language as existing machines at Dobson & Beaumont; it was supplied as a long-bed version for parts up to 500mm long, together with a bar feeder and parts catcher.
In the few weeks since it was installed, the machine has reduced the cycle time for a number of parts, including connecting rods that saw the time cut from 2min 10sec to just under 1min — plus the elimination of the secondary turning cycle that had been required to complete the parts. The most dramatic saving has been on the machining of hexagonal-head bolts where the cycle time has been cut from 8min to just 90sec.
Mr Guest added: “We produce a lot of bolts on which we have to machine the hexagonal heads, and this is a perfect example of the savings that we can achieve with the Nakamura-Tome machine.
“The combination of twin-spindle machining, powerful and robust milling capability and automated production through the bar feed and part catcher has made a significant difference on this component — as it will also do on future parts.”
He concluded: “This machine is a step-change in technology for our business, and we will be aiming to move legacy work from existing machines to the new Nakamura.”