Alpine F1 Team’s recent investment in eight Mikron MILL P 500U five-axis machining centres at its design and manufacturing facility in Oxfordshire has had a dramatic impact on the productivity and efficiency of its manufacturing operations and processes.
The F1 team currently has 11 Mikron five-axis machines for machining a range of high-precision, and often highly-complex, metal components for its ‘state of the art’ racing cars and, by October 2021, will have a further 10 Mikron five-axis machines at its disposal, dedicated to machining composite components supplied by Coventry-based
GF Machining Solutions Ltd.
The investment reflects the close, longstanding ‘technical partnership’ arrangement that exists between the two companies which is the longest in the racing team’s history and has, over recent years, seen GF Machining Solutions supply, not only a significant number of Mikron five-axis machines, but also a range of the latest, high-performance AgieCharmilles EDM wire and die-sink machines.
Following a recent investment to upgrade and strengthen its EDM capabilities, Alpine F1 Team’s portfolio comprises of four CUT P 550 (wire) along with a FORM 350 (die-sink) machine.
Almost two years ago, GF Machining Solutions supplied Alpine with eight new Mikron MILL P 500U five-axis machining centres. Four with integrated automatic pallet changers and four without, were installed at the F1 Team’s manufacturing facility in the summer of 2019. They replaced six, older Mikron HPM 450U five-axis machines that were acquired in 2016.
Ian Pearce, Alpine F1 Team’s head of supply chain, said: “The Mikron HPM 450Us are good machines but changing situations and circumstances, within our own manufacturing operations, dictated that they needed to be replaced — as a matter of some urgency.”
Prior to the arrival of the new MILL P 500U machines the team was machining front suspension uprights on its two, larger Mikron MILL P 800U machines.
Mr Pearce recalled: “It wasn’t ideal. Unfortunately the HPM 450U machines’ working envelopes were too small to accommodate the uprights so we had to machine them on the larger MILL P 800U machines instead. This created a problem and a production headache for us because work designated for the larger machines was backing up. It seemed as though every component needed to be machined on a MILL P 800U. As a consequence bottlenecks affecting all aspects of design, development and production were the result.”
Alleviating pressureBottlenecks and F1 are two things that do not easily sit together and to alleviate pressure on its MILL P 800U machines the decision was taken to replace its HPM 450Us with a number of larger capacity, high-performance five-axis machines.
Although a technical partnership with GF Machining Solutions existed, Alpine did investigate the market to identify the most appropriate five-axis machine tool replacements.
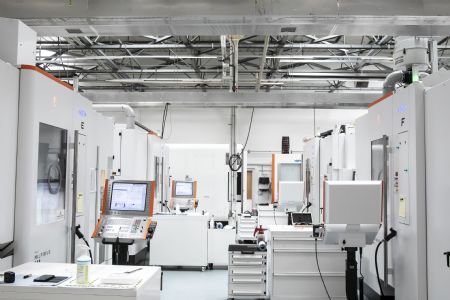
Bruce Foster, Alpine F1 Teams’ metallics production manager, said: “At the start of the process GF Machining Solutions was in pole position for a number of reasons - and not just because of the historical links between us.
”The most important of these include the after-sales service we receive from GF Machining Solutions, its first-class technical back-up and applications support, and, of course, the depth and breadth of its innovative and high-performance machine tool range.”
Mr Pearce continued: “When we investigated the market to replace the HPM 450U machines we were really looking for a smaller version of the Mikron MILL P 800U which are brilliant machines. They are universally liked by operators, programmers and designers and, since installation in 2017, haven’t missed a beat.”
They are used to machine a range of high-performance, mission-critical parts to exacting geometric tolerances and surface finishes including gear inserts, roll hoops, rear suspension uprights.
The MILL P 500Us are larger, faster, more stable and more rigidly designed and built five-axis machines than the Mikron 450Us they replaced. They feature fast rapids (61m/min) and 1.0G acceleration/deceleration rates enable the machines to get down to business fast — helping to reduce part cycle times and improving machine shop productivity.
A gantry-type construction and a trunnion rotary tilting table (with tandem support on its tilt axis) deliver increased rigidity and thermal stability which in turn deliver improved and repeatable accuracies and longer tool life.
Furthermore, the MILL P 500U and MILL P 800U have the same construction, architecture, CNC control (advanced Heidenhain) and kinematics enabling programs to be transferred between them increasing flexibility.
The larger work envelope of the MILL P 500U, in addition to compact build and relatively small footprint, enables it to machine workpieces up to 700mm diameter, enabling the front uprights to be machined on them - relieving the pressure on Alpine’s MILL P 800U machines.
Mr Foster explained: “The uprights are primarily 3+2 machined from solid aluminium on the MILL P 500U machining centres — with full simultaneous five-axis machining taking place when and where appropriate and beneficial.
“Cycle times are about 12hrs (per upright), geometric tolerances across the part are 10µ or better and the surface finish achieved is Ra 0.2µm.”
In addition to the front uprights the MILL P 500U machines, since installation, have been used to machine a range of complex, high-precision parts. One of these is the racing cars’ hydraulic manifold, a high-precision component used to regulate fluid flow in a racing car’s hydraulic system, thereby controlling the transfer of power between actuators and pumps.
They are machined from solid aerospace-grade aluminium to exacting tolerances. Over 85% of the material is removed during the roughing process leaving a complex part exhibiting a number of delicate and intricate features including holes and bores and cross holes.
Over a season 12 of these parts will be machined for each car — 24 in total — and the total machining time per part is well over 100hr making hydraulic manifolds an extremely valuable component — in more ways than one.
The acquisition of eight high-performance machines including four with seven-station automatic pallet changers (APCs) has given Alpine the necessary capacity to machine upgrades and replacement parts required for the current season, and to machine prototypes and parts, and their numerous reiterations for the new cars required for the next F1 season.
Optimising spindle uptimeMr Pearce added: “We had to minimise machine downtime and any disruption to our production schedules, as much as possible when changing over to the new machines. We worked with GF Machining Solutions to develop an installation programme that would optimise spindle uptime.
“The arrival of the new machines also gave us the opportunity to re-imagine and re-visualise the layout of our manufacturing facility to make it more efficient. In effect we have now created four machining cells, each comprising a MILL P 500U with a pallet changer and one without.
“Each cell is run by one operator and, the investment in four machines with automated pallet changers, has given us more or less a 24/7 manufacturing capability, allowing us to run the machines unmanned - during the day and overnight too.”
The investment in new five-axis machine tools and their subsequent impact on Alpine F1 Team’s productivity and efficiency is good news in terms of the new financial regulations coming into force in the sport next season which will limit the amount of money any team can spend on its race cars and on improving their performance during a calendar year.
Mr Foster said: “These are big changes. But, if there are to be limits imposed, it makes sense to make your manufacturing operations and production processes as efficient and effective as possible.
“Our advanced five-axis machine tools from GF Machining Solutions are helping us machine parts faster, better and more economically. The accuracies and finishes we get from the MILL P 500U machines means that parts are coming off them - right first time. There is less scrap and re-working involved. A real win-win situation.”
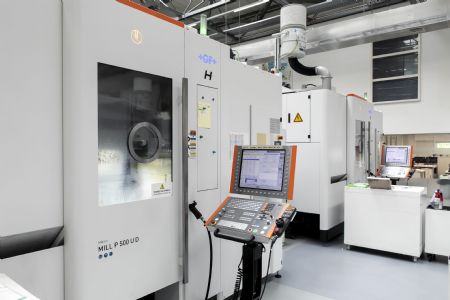
It is often quoted in F1 circles that “at the end of a racing season, an F1 team expects its cars to be running in excess of 1sec a lap quicker than at the beginning.”
Although this may be somewhat apocryphal it is true that they expect their technical partners to pull out all the stops to help improve their performance, on and off the track.
Alpine F1 Team’s use of GF Machining Solutions’ machine tools over many years and, more recently, its investment in the eight MILL P 500U machining centres in 2019, is delivering real productivity and efficiency benefits that will sand them in good stead in the future.
Mr Pearce concluded: “GF Machining Solutions is proactive and attentive. The company has put in the time and effort to really know and understand our business and they are a really valuable partner.
“We are delighted with the eight MILL P 500U and two MILL P 800U machining centres we acquired in 2019 and 2017 respectively. So much so in fact that we have already invested in a third MILL P 800U (for machining metallic parts), and will be acquiring a number of new MILL P 800U machines by October 2021 for machining composites.”