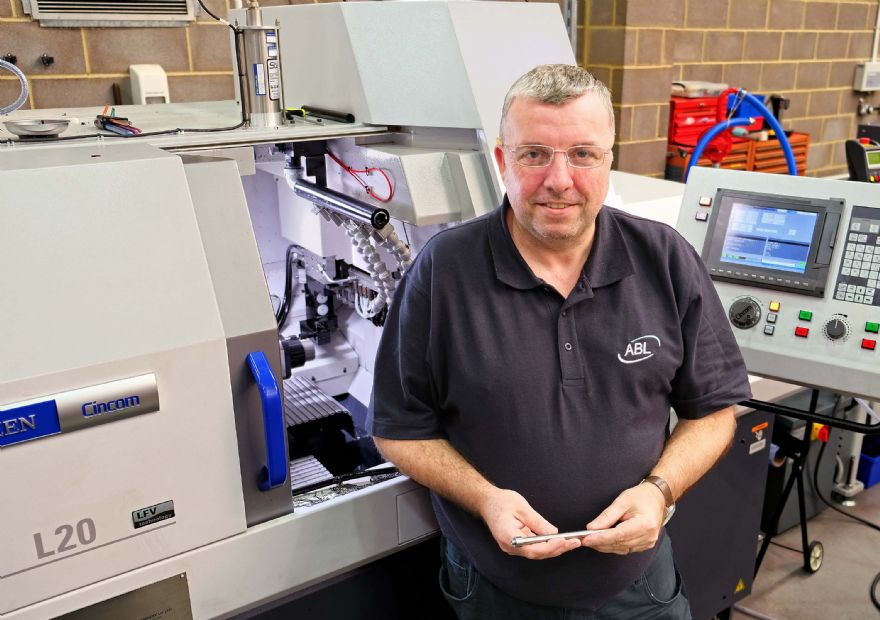
The first sliding-head turn-milling centre to be installed at the Ferndown (Dorset) factory of
Air Bearings Ltd (ABL) is a Citizen Cincom L20-VIIILFV.
Installed in June 2019, this machine has allowed ABL to bring in-house the production of nearly all shaft-type components, saving around £8,000 per month previously spent on sub-contract Swiss-type turning and enabling the L20 to pay for itself within 18 months.
Speeds up to 350,000rev/min are attained by ABL’s air bearing spindle units, which are used globally in machinery for semiconductor wafer slicing, printed circuit board drilling, and micro-machining applications as diverse as the manufacture of polymer lenses for cataract operations, the edge grinding of toughened glass for mobile phone screens, watch component manufacture and the milling of coining dies.
The high rotational speeds require that sub-micron tolerances be held on some turned bores and other features of component parts of the air bearing assemblies. This in turn means that operations prior to diamond turning and grinding of the bore and outside diameter of the bearing itself must also be very accurate to meet pre-finishing requirements.
In its pre-finishing department, ABL operates: two vertical machining centres; seven two-axis ‘chuckers’; two multi-axis bar-fed fixed-head lathes; and now the Citizen L20 slider from Bushey-based
Citizen Machinery UK Ltd.
To meet the levels of precision required to ensure rotational motion of the air bearing spindle to within a couple of microns, ABL only buys ‘top-end machine tools’, as achieving the tolerances and finishes specified for the shaft assembly with its six key parts is especially critical.
Sub-micron accuracyDave Stacey, the company’s senior production controller, said: “Take the collet, for example, which is produced from 13mm-diameter tool-steel bar. The concentricity of the front bore to the taper is tied up to 30µm TIR (total indicator reading), while the dimensional tolerances on diameter and length need to be within 50µm, or sometimes 25µm to allow post machining to sub-micron accuracy — plus there is a 6µm limit in the bore.
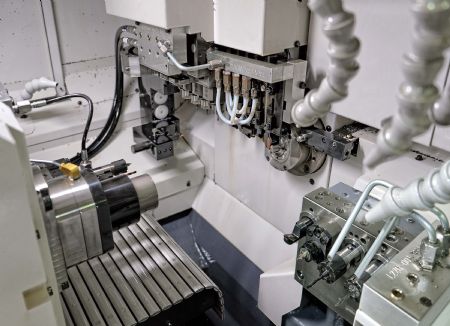
“Before our decision to use sub-contract services, these collets were machined in-house in two operations: turning and boring on a fixed-head lathe, followed by the drilling of eight radial holes on a machining centre. This time-consuming process meant that our pre-finishing department only produced the quantity that was needed, which could be as low as 15-off, yet external heat treatment and stress relieving before final finishing still cost £250 a time, irrespective of component quantity.
“Now, with single-hit turn-milling of the collets on the Cincom L20, we run off typically 500, representing three months’ supply, at a fraction of the cost of sub-contracting them out, added to which we can take full advantage of the fixed-cost heat treatment service.”
It is a similar story with the other rotational components in the shaft assembly of an air bearing spindle, such as the EN57 stainless-steel collet studs and guide pistons, of which there are six variants. All are produced more economically on the slider, as they involve classical Swiss-type turning from bar less than 13mm in diameter.
The largest part produced on the Cincom L20 is a 250mm-long push rod that is turned from 16mm-diameter silver-steel bar down to a diameter of 7mm in one pass. Taking a 4.5mm depth of cut in this high-carbon steel over much of the component’s length is an application that highlights the benefits of Citizen’s patented LFV (low frequency vibration) chip-breaking software in the Mitsubishi control.
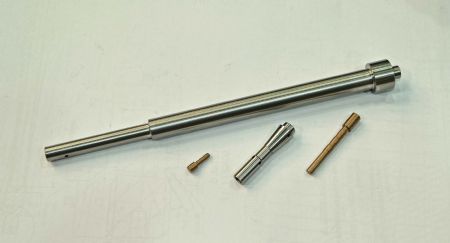
LFV allows what would normally be long, stringy swarf to be broken into shorter lengths, thereby avoiding ‘birds-nesting’ around the component and tool and the need to repeatedly remove the swarf from the machining area by hand.
Mr Stacey added: “Economy of production is greatly increased, as there are no stoppages for swarf clearance and the lathe can be left to run unattended. Furthermore, the absence of chatter improves the surface finish on machined components — and LFV may be switched on and off during a cycle by G-code command. Moreover, this Cincom lathe is so fast at producing rotational parts from bar, even with the larger batches we are running, that the machine is often waiting for work during the day.
“We are therefore looking at putting classical fixed-head work onto the machine, parts that are shorter compared with their diameter, which will provide an opportunity to bring further sub-contracted turning in-house. For this purpose, the ability to run the Cincom L20 in guide bush-less mode will save material — and costs — by shortening the minimum bar remnant.”