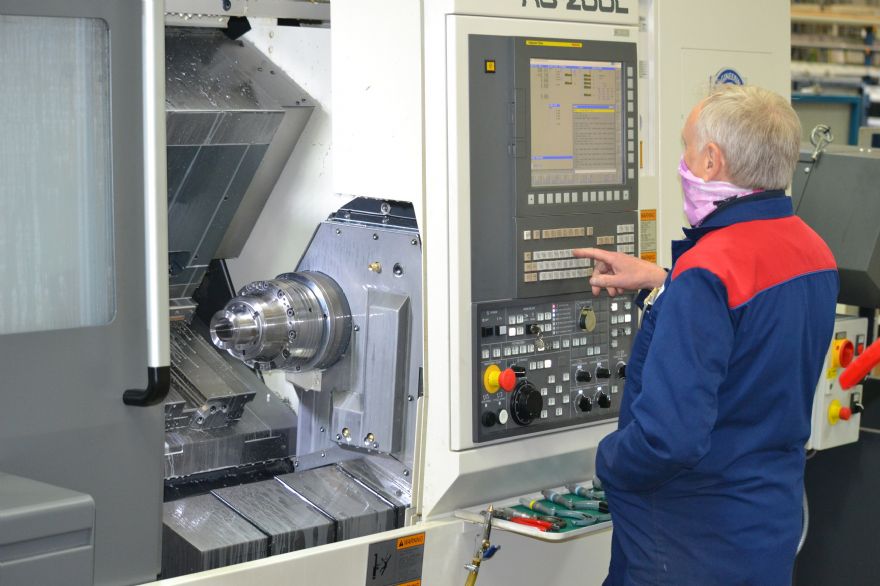
When Cheshire-based
JEB Precision Ltd, a sub-contract manufacturer, won an order to manufacture a complex component for an aerospace air handling system, the company made the decision to invest in a new Nakamura-Tome AS200L-MYS turning centre supplied by the Wellesbourne-based
Engineering Technology Group (ETG) to boost its production capacity.
In 2019, the Northwich manufacturer that primarily produces components for the scientific instrument and aerospace sectors had won a substantial order that initially resulted in the complex aerospace parts being machined via three turning operations and two milling operations. The S130 grade stainless steel parts were required in batches of more than 100 per month and the five set-ups on multiple machines was considered to be an unsustainable long-term solution.
Founded in 1974, the ISO:9001-certified company offers a wide ranging service that encompasses CNC milling up to five-axis, turning, wire erosion, jig boring, honing, surface and cylindrical grinding as well as full scientific instrument assembly.
Despite this comprehensive versatility, the challenging aerospace part required a new process to improve throughput, precision and quality. With six ETG turning centres on-site, JEB Precision was already familiar with the extensive solutions available from ETG – but this was the first Nakamura-Tome machine to be installed at JEB.
Robust platformMichael Bebbington, JEB operations director, said: “While our Hardinge turning centres are very capable machines, the Nakamura-Tome AS200L-MYS is a twin-spindle machine with milling capability and Y-axis machining that is built on a very robust platform. By investing in this technology, we were immediately able to reduce set-ups, increase throughput, improve process reliability and quality and free capacity on our other machines.”
Before the arrival of the Nakamura-Tome AS200LMYS in January 2020, the 83mm diameter x 23mm aerospace part was precisely machined on two turning centres with the third operation incorporating turning on a third machine with an expanding mandrel to ensure the thin-walled part achieved the concentricity and precision required.
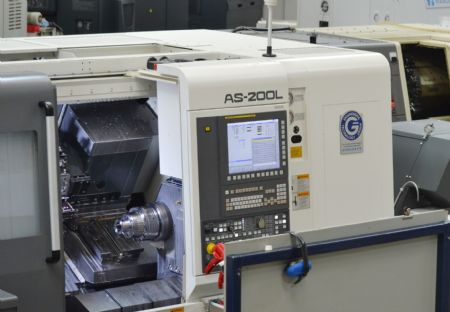
The three operations were followed by a milling process that required four reamed and counter-bored holes to a tolerance of +0.012/-0mm with final machining on a second machining centre that milled features on the final face.
Mr Bebbington continued: “The set-up time for the components was 2hr for the first turning operation, 1hr for the next and 1.5hr for the third operation. Then we had two milling set-ups of 1.5 and 1hr respectively, giving us a total set-up time of 7hr.
“Despite this, the combined cycle time was only 30min. However, almost all dimensions were tied to a tolerance of +/-10µm with some features having tolerances below that. What made this part more challenging was the behavioural characteristics of the material between processes with extensive machining and thin wall features creating a susceptibility to deformation.”
Complete machining in a single operationThe Nakamura-Tome AS200LMYS was installed at JEB Precision with a Hainbuch collet chuck in the main spindle and a Hainbuch expanding mandrel on the sub-spindle for ID (inside diameter) clamping to ensure complete machining in a single operation.
The part is machined complete in just 20min on the Nakamura-Tome AS200LMYS and in the early days of gaining familiarity with the twin-spindle workhorse, JEB had slashed 30% off its programming time – a figure that is destined to improve as the company enhances its understanding of the machine.
However, just two months after installing the Nakamura-Tome AS200LMYS, the world went into lockdown with the aerospace industry and its supply chain heaviest hit. For JEB Precision, the new order that justified the Nakamura purchase was put on hold.
Mr Bebbington explained: “The family of aerospace air-handling system components was forecast to be 25% of the capacity of the Nakamura. While this work has not been lost long-term, we needed to fill the capacity of the Nakamura throughout the pandemic. As a business, the impact of Covid-19 has not been as devastating for us as it has been for many others.
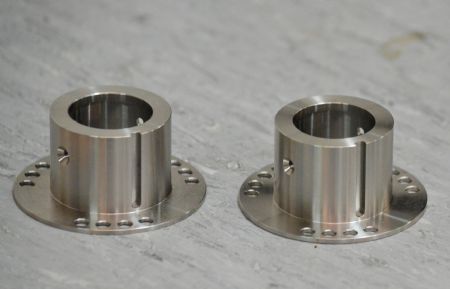
“The majority of our work is in the scientific instrument industry and we manufacture a lot of parts and assemblies for mass spectrometers and electron microscopes which have been required by the scientific community throughout the pandemic. We looked at some of our existing parts with multiple set-ups and how we could transfer those parts to the Nakamura to reduce set-ups and improve throughput and productivity.”
With increased availability on its new Nakamura-Tome AS200LMYS, JEB identified a scientific part that is used on a quadrupole analyser assembly that could be transferred to the new turning centre.
The long-term 304L stainless part had historically been machined with three turning operations and an additional two milling operations. This process included one rough turning operation with two subsequent finish turning operations on Hardinge turning centres that were followed by 4th axis drilling, countersinking and 3.2mm wide slotting on a machining centre with a final operation of drilling holes on a PCD around the flange face on a fifth machine.
By transferring this job from a multitude of machines to a single operation on the Nakamura-Tome AS200LMYS, JEB Precision reduced the machining time by almost 30% from 28 to 20min.
Once again, the major savings arrived from reduced set-ups, improved throughput and quality as well as the freeing of capacity throughout the facility. The previous process required 8hr of set-ups across the respective five machines, something that has been cut to less than 5hr.
Mr Bebbington said: “As our familiarity with the Nakamura improves, so will our set-up times. It has instantly improved productivity and reduced set-up times by more than 30%. However, this is not the only reason behind the purchase. Single set-up machining has reduced manual handling and improved process reliability, throughput, precision and overall quality.”
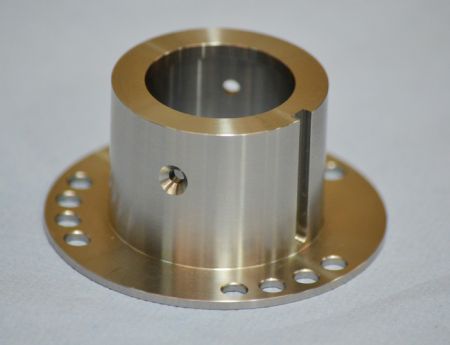
He added: “With the considerable complexity of many parts and the number of set-ups, the Nakamura has made an evident impact on lead times. For example, the quadrupole analyser component would have taken at least three to four weeks for us to get the first parts through the shopfloor – with the Nakamura we can set the machine and finished parts can be out of the door in 24hr.
“As we get more parts programmed and stored on the Nakamura, we will improve the lead times for many more of our complex parts. The overall benefit to our business will be huge as we free capacity on several older machines and we reduce the pressure on our skilled engineers to programme, set and produce parts on a number of machines.”
JEB Precision is delighted with the capabilities and benefits of its Nakamura-Tome AS200LMYS and the company has no qualms about buying more Nakamura machines in the future. As the world exits the pandemic and gradually returns to some semblance of normality, the 25-employee company has continued its investment strategy with a twin-spindle turning centre with Y-axis milling capacity arriving from ETG in February 2021. The was installed to replace an older machine.
Mr Bebbington concluded: “We have had Hardinge turning centres for over 25 years and some of our existing machines are 20 years old.
“The 51mm diameter capacity machine replaces a 20-year-old machine of similar specification that was at the end of its life. The Nakamura machine has proven invaluable for our business and as we continue to exit the pandemic and grow our business, we have no doubt we will be investing in more machines from ETG.”