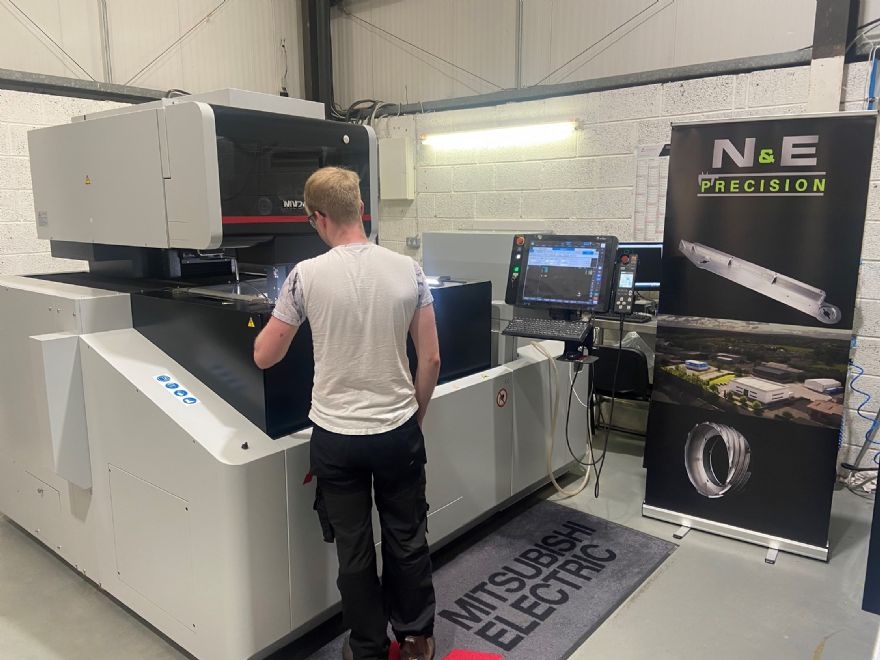
Founded in 2005 and located between Galway and Dublin, 24-employee
N&E Precision Ltd produces components for the aerospace, oil and gas, medical, pharmaceutical and general engineering sectors.
However, while many sub-contractors might consider ‘aerospace-grade’ materials like titanium, Inconel or super duplex stainless steel as ‘difficult to machine’, N&E Precision manufactures specialist precision parts from materials such as HSS and tungsten carbide — plus the ‘standard challenging materials’.
The company had been sub-contracting a considerable amount of EDM machining work out to local companies, but to reduce costs and improve control over its processes and lead times, N&E Precision went to the
MACH 2018 show to investigate the EDM market.
Following a comprehensive review, joint managing directors Noel and Eamon Farrell opted for a Mitsubishi MV2400R wire EDM (with an EKO Ioniser system) from the Wellsebourne-based
Engineering Technology Group (ETG). Such was the success of this first EDM machine that a second — a Mitsubishi MV1200R in 2020 — was later added.
Noel Farrell said: “Our monthly sub-contracting costs were taking the margins out of a lot of our work, but we immediately eradicated this issue with the Mitsubishi MV2400R. The training was first class and the user-friendly CNC interface contributed to the machine ‘hitting the ground running‘.
In fact, we now have two trainees operating the two EDM machines, which are running for up to 100hr a week. Our lead times for many components fell from weeks to just two to four days — with some parts being turned round in less than 24hr.
“We make a lot of specialist medical parts from HSS and carbide that couldn’t be produced on a machining centre. We also make parts from hardened tool steel that require 0.4mm-diameter holes up to 50mm deep — and we have regular large batches of super-duplex parts for the offshore and waste management sectors that require using the full 310mm Z axis of the Mitsubishi MV2400R to produce.
“We also make parts that require complex forms that would be impossible to process with a machining centre. That said, some parts we pre-machine, transfer them to an EDM machine then — if necessary — transfer them back to other machines for final operations.
“The two Mitsubishi machines have added greater flexibility to our business. Some parts have tight-tolerance bores, but instead of machining them conventionally we produce them on the EDM machines, confident that we can achieve tolerances better than ±5µm — and with excellent surface finishes.”