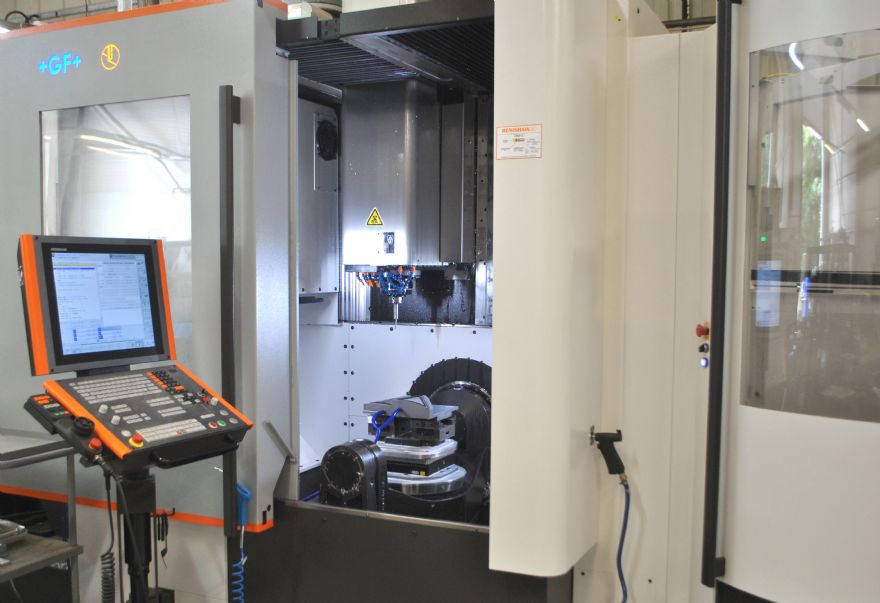
Northamptonshire-based
Luzzo Bespoke Ltd, a designer and manufacturer of innovative bespoke products, has been supplied with a new Mikron MILL E 700U five-axis machining centre by
GF Machining Solutions.
The rigidly-built and ergonomically-designed machine, which features an integrated seven-station automatic pallet changer (APC), was installed at the company’s 10,000ft
2-plus facility in Brackley in April and is currently being used to machine a range of high-precision and often complex-shaped components in low volumes that go into the products for Luzzo Bespoke’s growing number of high-end automotive, motorsport, and lifestyle customers.
These components, made from a wide range of materials including aluminium, brass, stainless steel, carbon fibre, wood and plastics, are machined to high accuracy — typically +/-0.1mm — and to exacting surface finishes.
The MILL E 700U is also being used to machine special and innovative work-holding and fixtures, as well as numerous prototypes and pre-production components – integral to the company’s Design for Manufacturing (DfM) services.
The machine joins an existing Mikron five-axis machining centre, a HEM 500U, acquired by the company in 2016. Together, these two high-performance five-axis machining centres, working side by side, provide Luzzo Bespoke with fast, efficient and reliable milling capabilities, and proven machine tool technology designed to improve part accuracies and repeatability’s and increase productivity.
Like many other manufacturers, Luzzo Bespoke felt the impact and effects of the pandemic. Staff were furloughed and several orders and contracts were postponed — some were cancelled altogether. However, during the summer of 2020, business began to pick-up and has been on an upward trajectory ever since.
‘Pinch points’Brian Challenger, Luzzo Bespoke’s managing director, said: “Since the beginning of 2021 things have improved considerably – so much so in fact that we could see that if we didn’t strengthen our existing milling capacity and capabilities, sooner rather than later, production ‘pinch points’ would occur that would detrimentally affect our operational efficiencies and productivity. As a result of these deliberations we decided to invest in a new machining centre.”
He continued: “Over the past 12 years our machine shop has changed and improved dramatically from having no CNC machine tools to one that features high-performance CNC multi-tasking lathes and three- and five-axis machining centres.
“We believe that five-axis machining is the way to go. The technology makes us more flexible and enables us to machine parts in fewer set ups - often in one hit. This makes us more efficient and productive.”
The same is true of automation. Mr Challenger added: “Machines with integrated automation have the ability to run ‘lights out’ overnight and over the weekends. A machine with integrated pallet change capabilities can give us up to 14hr additional machining time per day — a massive boost to our productivity.”
In addition to the machine having to be a five-axis machining centre equipped with integrated automation other machine requirements included: a high-speed, high-torque spindle; full simultaneous five-axis machining capability; good-sized working envelope with easy part loading/unloading; generous-sized automatic tool changer; efficient and effective swarf management; and the latest Heidenhain control
The decision to invest in a new Mikron five-axis machine from GF Machining Solutions was not a foregone conclusion, although Luzzo Bespoke has invested in a number of Mikron three- and five-axis machining centres over the years and, prior to the arrival of the new MILL E 500U, had two three-axis VCE 800 Pro machining centres and one HEM 500U five-axis machine at its disposal.

Mr Challenger recalled: “We approached GF Machining Solutions and other companies with our requirements. Taking the machine cost, its availability and its technical specifications into account, as well as the applications and service back up of GF Machining Solutions, we invested in the Mikron MILL E 700U.”
The new machine is a high-efficiency five-axis machining centre that has a rigid C-frame construction, large-sized guideways, a double-supported trunnion-type direct-drive rotary tilting table and an integrated seven-station APC.
Unrivalled machining flexibilityEquipped with a Heidenhain TNC 640 control and featuring a powerful, high-speed 36kW 20,000rev/min OptiCool spindle with oil-air lubrication, the MILL E 700U delivers ‘excellent cutting performance, unrivalled machining flexibility and best-in-class process reliability’.
Mr Challenger explained: “The machine’s advanced spindle technology with oil-air lubrication enables us to maintain part accuracies and keep within tolerances during long machining runs, and its direct-droive rotary table technology, in combination with the StepTec spindle, means we can achieve super-fine surface finishes on machined parts.
“All in all, the MILL E 700U is a versatile, high-productivity machine – and is a real asset to the company.”
Luzzo Bespoke designs and manufactures a range of high-quality bespoke products for a wide range of markets and industries. One of the most important of these is the luxury car market where the company designs and manufactures high-end products that include drinks cabinets, picnic hampers, under seat fridges, humidors, customised and bespoke clocks, dials and instrumentation panels, for the prestigious automotive manufacturers including Rolls-Royce, Bentley, McLaren, Bugatti and Jaguar Land Rover.
The company also manufactures a range of motorsport and classic car parts and, to lessen a potential over-reliance on the automotive sector, has diversified its operations designing and manufacturing products for the marine and furniture markets.
Many products manufactured by Luzzo Bespoke, especially for its luxury car maker customers, are supplied as ‘finished’ products – with all manufacturing and assembly taking place at its Brackley facility.
Mr Challenger added: “We are a ‘one-stop shop’ design and manufacturing solutions provider. In addition to our comprehensive machining capabilities, we provide a range of ‘other’ manufacturing and finishing services and specialisms in-house; these include wood veneering, laser engraving/marking, spray painting and polishing.”
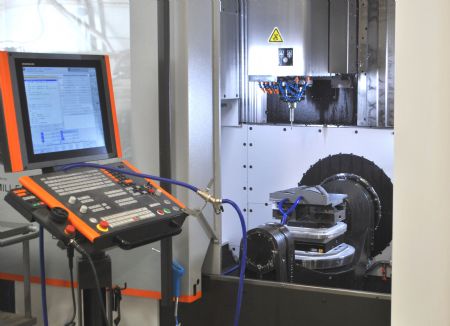
Bringing all these services and specialisms under one roof helps the company maintain its high-quality standards, and keep control of its operational costs and customer delivery schedules etc.
Mr Challenger continued: “We made a conscious decision some years ago to avoid sub-contracting work out. This move has helped make us more competitive and has differentiated us positively in our markets, and with our customers.”
The new Mikron MILL E 700U machining centre is helping Luzzo Bespoke improve its productivity and performance with its full simultaneous five-axis machining capabilities. They have been put to full use machining complex features and details that could only be achieved previously by using a multitude of special fixtures or multiple set ups.
The machine’s integrated automation is also proving its worth with multiple parts being set-up during the day on its seven pallets and machined to completion overnight.
Mr Challenger concluded: “The future is five-axis machining and over the next few months we intend to make further investments in this technology.”