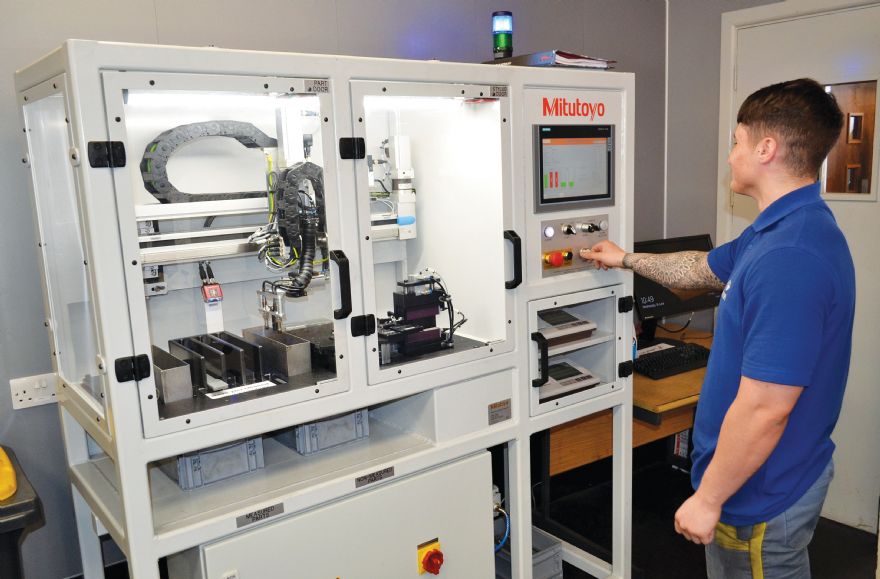
With operations in 26 countries
Tata Steel is one of the world’s most ‘geographically diversified’ steel producers. The company’s Port Talbot plant in South Wales can produce about 4.5 million tonnes of steel slab per annum, making it ‘the largest steel plant in the UK’, with the automotive industry a major user of steel-strip manufactured at the Welsh plant.
Because the correct surface finish characteristics enable paint and other coatings to successfully adhere to vehicles’ bodywork, the steel strip supplied by Tata steel to its global automotive customer base must conform to strict surface finish specifications — hence the installation of a bespoke machine that was designed and installed by Coventry-based
Mitutoyo Gauging Technology.
John Lovegrove, Tata Steel Port Talbot’s metallurgical testing manager, said: “Although our previously used manual surface-finish testing method delivered accurate results, it was extremely laborious and at times we struggled to keep pace with the amount of surface-finish tests needed — and we had to manually input each individual test result into our computer.
“Having decided that we needed to source a highly efficient, automated testing system, we approached three companies with a list of system requirements. The staff at Mitutoyo Gauging Technology not only quickly understood our needs but also suggested several improvements that would bring additional benefits.
“Moreover, as the project evolved and we realised the potential a new custom-built tester could offer, we asked for couple of further design tweaks, which Mitutoyo incorporated.”
Rapid and very accurate surface-finish testsHe continued: “Now installed and fully operational, our bespoke Mitutoyo machine performs rapid and very accurate surface-finish tests on both sides of our strip samples in a single-pass, slashing our inspection times; and because our surface-finish testing is now a fully automated process, after loading a large batch of samples into the machine the operator can undertake other work.
“Furthermore, because all relevant inspection data is now automatically downloaded, our new system has also removed the potential for errors associated with manual data input.”
Designed by the staff of Mitutoyo Gauging Technology with technical input from Tata metallurgical technologist and project manager Taylor Clarke, the surface-finish measuring machine was designed to remain ‘future proof’, as the bespoke aspects of the machine can be modified at a future date.
In addition, the system’s SJ-310 Surftest instruments can provide readings in a number of surface finish parameters.
Simon Elliott, Mitutoyo Gauging Technology’s general manager, said: “Mitutoyo Gauging Technology provides its customers with bespoke metrology systems for applications that cannot be satisfied by the use of off-the-shelf products.
“Following our liaison with John Lovegrove of Tata Steel, the resulting automated surface-finish measuring machine was schemed, designed, built, tested delivered and commissioned within the required timescale.”