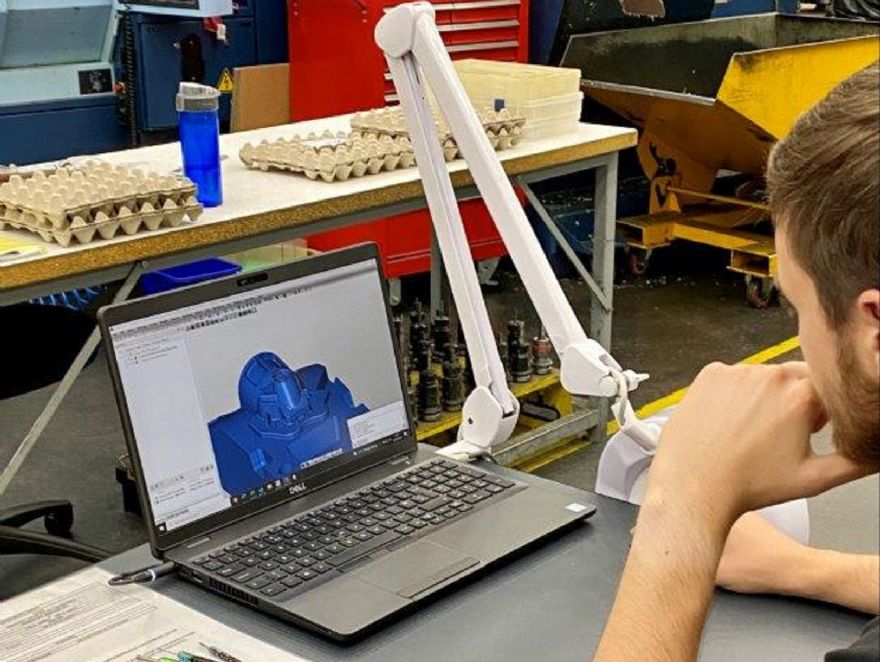
When Cambridgeshire-based
Shearline Precision Engineering Ltd recently added to its advanced five-axis machine tool capability, the company recognised that it needed to upgrade its CAM software to maximise the productivity of its investment. That is why the company has invested in the HyperMILL CAM software from
Open Mind Technologies.
As part of the Shearline Group that operates out of an 8,500m
2 manufacturing facility in Ely, the engineering firm is accredited with AS:9100, ISO:9001 and ISO:14001 and manufactures everything from simple to extremely complex components for customers in the aerospace, instrumentation, motorsport, medical, packaging, power generation and printing industries. It is the complex production tasks on its five-axis investments that have led the manufacturer to seek the expertise of Open Mind Technologies.
Simon Cooper from Shearline Precision Engineering Ltd said: “One of the key reasons we switched to HyperMILL software from a relatively successful CAD/CAM package, was because when it came to the top end — jobs that required 3-D scanning and simultaneous machining on our latest 10-pallet Matsuura MX-330 — the current system had its limitations. So, after a fair bit of research, we concluded that HyperMILL perfectly fulfilled our requirements.”
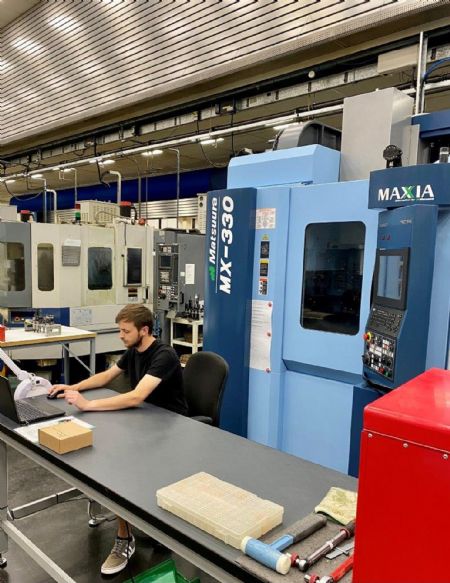
The company that was founded in 1973 invested in HyperMILL at the end of 2020 and the package is already making an impact. Mr Cooper said: “The cycle times and set up times are decreasing, especially as we always have our programming suites right next to the machines. We use the same operators that do all the programming, setting and methodology of fixturing as well as running the machines. As the they all work next to each other, all programming and fixturing can be done very quickly without having to go back to an office or acting as a liaison between people to undertake the tasks.
“As all the team see the projects through from start to finish, they are more invested in each job. This means that we always tend to get a better quality of product and a better understanding of how each part is being machined.”
Shearline cell leader and programmer Tom Biscoe said: “We have done a couple of jobs with HyperMILL and the difference shows. It just makes you quicker at doing everything. It is so much simpler to use, and a lot of the features are something that we didn’t have in our old software.”
Machine simulationHe continued: “One of the big features that HyperMILL has that our existing software doesn’t, is the machine simulation. This undertakes the collision checking and gives the operator a visual representation of how everything is going on the machine.
“This puts our mind at ease when we are watching something through, especially on five-axis jobs that you know are going to be tight.”
“Having the ability to work off a single datum point, an impressive tool library and tool path flexibility has reduced programming times by 30% compared to our previous system. However, as we do a lot of batch work from 50 to 150-off that is often repeat orders, we will benefit from the programming efficiency going forward more than at present.”
One feature of HyperMILL that has impressed Shearline during the programming process is the tool library. Mr Biscoe said: “Our old software package did have one, but because it wasn’t very good, nobody used it. With HyperMILL, the tool library is very helpful, especially with the fact that we have three machine tools with very large tool capacities.
“This means that we can use the same tool and spread it across all three machines and all of the functions remain and you can apply all sorts of cutting data to the tools and use that data for different tool paths.”
Tolerancing on 3-D tool paths“Another feature is the tolerancing on 3-D tool paths, which the operator can adjust, and this is a massive help to us; and as we see more of those complex parts that first enticed us to purchase the software, we are going to continually see more of those benefits.”
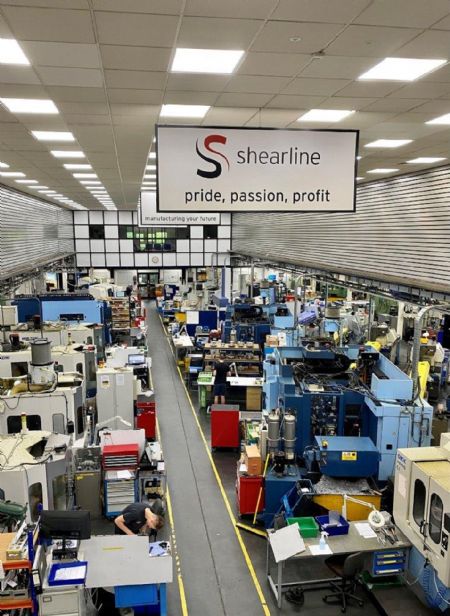
He added: “We have reprogrammed some parts with HyperMILL and it is 10-times better than before. The cycle times on the machine are currently around 30% faster too. This is because there is no ‘air cutting’ like with the previous system. With our type of batch production and pallet loaded machines, this 30% saving will be significant. We are also witnessing far better surface finishes and tool life too.”
Mr Biscoe added: “The training was really good considering the circumstances and the situation that we are all in at the minute with Covid-19. We have had two three-day sessions so far and we have another one to go. So far, we have got on very well with HyperMILL. I have been programming on our previous software for over 4.5 years and I thought the transition was going to be difficult, but it hasn’t been.
Mr Cooper concluded: “I think the real advantage of HyperMILL is the ease-of-use and how the amount of effort required to make such top-quality components can be reduced. This enables us to have more people involved from further down the tier levels of programming experience. HyperMILL seems to have everything we could have wanted from a top-end system, and it is a proven product.”
“If you go to the trouble of investing in a £300,000-plus machine tool without having a programming suite to go with it, it is a bad move. Now, we can not only offer our customers top-end machine tools, but also a top-end programming suite.”