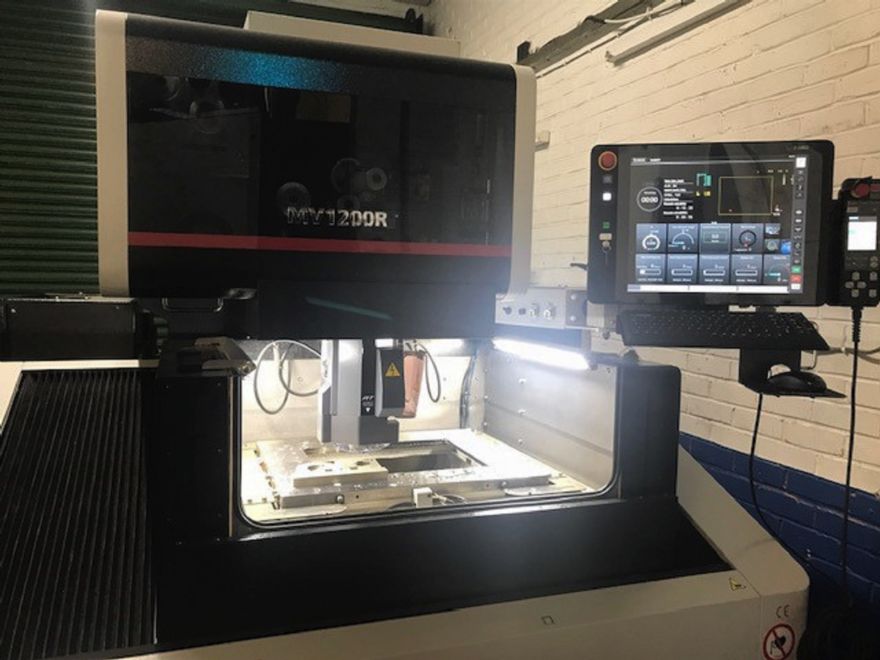
When long-established Sheffield-based cutting tool manufacturer
AA Tools was acquired by new owners in 2014, their objective was to modernise the shopfloor equipment with the very latest CNC machine tool technology.
The company manufactures a wide variety of tools and wear parts, alongside offering a sub-contract machining service; but when its production and re-grinding of bespoke cutting tools — many hundreds a month — began suffering a bottleneck due to a reliance on optical grinding, the directors investigated possible solutions and concluded that wire-cut EDM would alleviate the problem.
They subsequently selected a Mitsubishi MV1200R machine from the Wellesbourne-based
Engineering Technology Group.
Recalling the selection process, Chris Birt — AA Tools’ business development director — said: “We use our optical grinder for profiling, tip shaping and brazed-carbide production, which meant the machine and operator were overloaded and were a pinch point in our business.
As a newcomer to EDM, and a company looking to buy its first EDM machine, we reviewed a number of machines and spoke to a number of customers; and while many recommended Mitsubishi EDM machines, it was a demonstration by ETG’s Scott Elsmere that clinched the deal.”
Installed at the end of 2020, the Mitsubishi MV1200R has a work envelope of 400 ¥ 300 ¥ 220mm and has not only eradicated the optical grinding bottleneck but also reduced lead times on special tools by more than 50%.
Mr Birt continued: “With the Mitsubishi MV1200R we can undertake the profiling and shaping tasks that were once only possible on the optical grinder; moreover, we can modify tools, manufacture tools and take on new work that wasn’t previously possible.
“The Mitsubishi machine has also presented new opportunities beyond the scope of cutting tools, such as the manufacture of bespoke jigs and fixtures. It has also reduced operations and costs for our business. For example, when grinding steel tool bodies with carbide tips, the operator would have to change grinding wheels multiple times for the different materials and profiles; the EDM machine will precisely cut tool profiles regardless of material.”
Adam Wood, AA Tools’ production director, added: “For a company with no EDM experience, we found the user interface very easy to use, presenting a familiarity that shortened the learning curve for our team.
“We now have three staff members capable of using the machine as opposed to just one operator for the optical grinder — a situation that enables us to schedule our work more effectively. We can also easily import DXF files and rapidly set up repeat jobs with ease. Indeed, the machine is so easy to use,that we already have an 18-year-old apprentice working with it.”