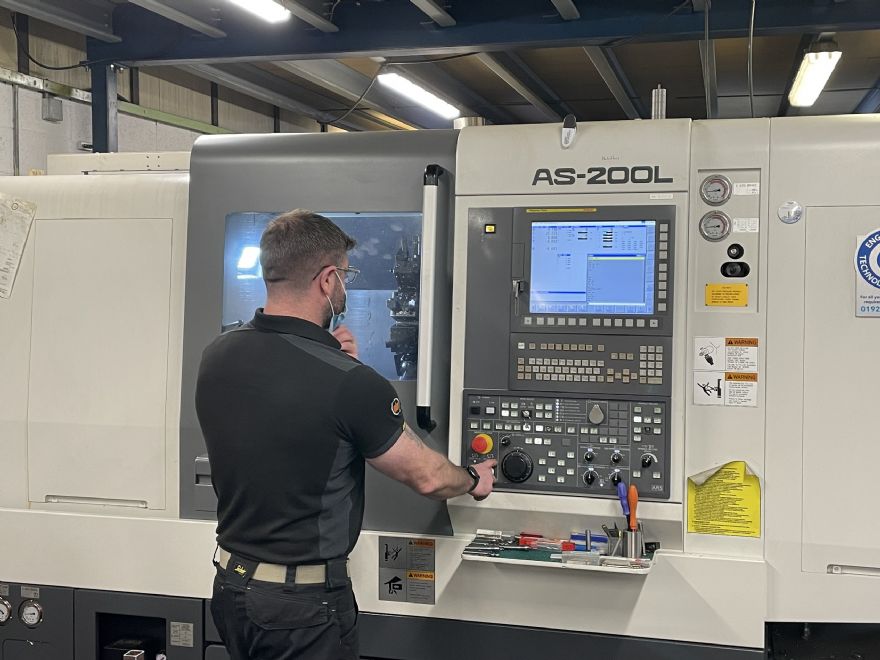
Founded in 1992, County Kildare-based
P&T Precision Engineering has an established reputation as a sub-contract manufacturer that specialises in the production of jigs, fixtures and machined components for the food, medical and pharmaceutical sector.
Historically a manual machine shop, the County Kildare company has made the transition from manual to CNC machining with the support of the
Engineering Technology Group (ETG) Ireland.
Darragh Walsh from P&T Precision Engineering said: “We were a small family company with six employees and we decided to invest in CNC equipment from ETG. This has helped us to grow in the industry sectors that we need to grow in, increase capacity and shorten lead times. As a result, we have rapidly gone from six staff to 22, and increased the number of machines.”
Jamie Fletchmore, managing director at ETG Ireland, said: “P&T was an up-and-coming family-run business that was coming from manual machines into the CNC world. They approached us and said they wanted to make that advance from manual to CNC machining. We sat down and spoke about the first machining centre and we introduced them to the Qauser MV184. From there, we migrated one every two years and they were buying more technology, which included the Nakamura AS200L turning centre and then two years later they purchased another Qauser MV184.”
The first step the Naas-based company took was to invest in the Qauser MV184 vertical machining centre. The Qauser MV184 provides a spacious work envelope with X-, Y- and Z-axis travels of 1,020 x 610 x 610mm and a 1,200 x 600mm bed with a load capacity of 500kg. The BT40 taper spindle machine provides a maximum spindle speed of 12,000rev/min that is supported by a 30-position automatic tool changer.
Mr Fletcher continued: “This type of machine is a big step up from where they were, machining parts on manual machines in multiple operations. With the Quaser MV184, P&T were able to take those manually machined parts from drawing and CAD model straight into the machine with a finished part coming off.
“So, they were able to get the parts through the shopfloor much faster and that also reduces the downtime involved with going from one operation to another with the manual process. Investing in our machines and technology has enabled P&T to move through different types of components and different kinds of materials, especially harder materials. This has allowed P&T to move into markets that they were not used to working in.”
Finishing parts in one operationHe added: “It has opened doors and opportunities that has led the company to then look at the Nakamura AS200L turning centre. This machine opened P&T up to a new range of products that they could now produce. They were making parts in multiple operations from a lathe point of view and now, by using the Nakamura AS200L turning centre they can finish those parts in one operation. P&T are now able to do all of the milling, drilling, tapping and then also transfer parts to the second spindle, so the part is coming off the machine in one complete operation as opposed to multiple operations.”
The Nakamura AS200L twin-spindle turning centre from ETG Ireland is a 65mm diameter bar capacity machine with an 8in chuck that offers a turning capacity up to 340mm diameter with a maximum turning length of 570mm — providing sufficient capacity for the requirements of P&T.
With a powerful 11/15kW 4,500rev/min main spindle motor and a sub-spindle unit with 5.5/7.5kW and 6,000rev/min, the Nakamura AS200L is perfect for the productive turning of all material types with its perfect blend of power, torque and spindle speed. This is complemented by a driven tooling unit with capacity for up to 15 driven tools with a maximum spindle speed of 6,000rev/min and 3.7/5.5kW spindle power, ideal for all the drilling, threading and milling requirements of P&T.
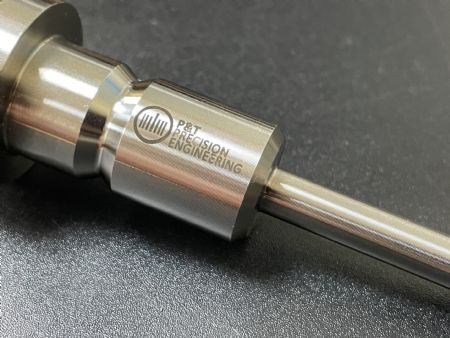
Mr Fletcher said: “P&T are a very creative company and they do a lot of design work for the companies that they work with. So, they came to us with particular types of work and asked if they could do it on our machines.
“We sat down with them and supported and guided them through the different ways that we could approach jobs – in a way that was different to what they were doing in the past. That has enabled P&T to create much better parts, much more quickly while retaining and improving upon the precision and the tolerances of the parts that they are making.”
Mr Walsh added: “We went to ETG because they give great support and service and they also provide fantastic quality machines with great repeatability and durability. We have never had any issues with any machine that ETG hasn’t been able to fix within a couple of hours.
“The Nakamura AS200L turning centre has enabled us to machine components in a much faster time because there are fewer setups. So, instead of taking jobs from the lathe to the mill - we can now do it all in one shot. This has decreased our machining times, it has reduced our delivery times and it also means we can get more parts through the machine shop.”
Mr FLetcher explained: “ETG Ireland also provided all of the training, as the Heidenhain CNC control was new to P&T. We guided them through the training process and how the CNC control works. We also provided full operator training where we came in and set their parts up with the shopfloor machinists and went through the full machining aspect. ETG has taken P&T from the manual machining process to the full CNC process, we were able to be there all the way.”
Mr Walsh concluded: “The future for P&T will hopefully see us increase the size of our workshop to 2,000ft
2, expand with quality machines, and also increase our workforce to help increase our capacity. This will certainly result in more machine tools from ETG Ireland.”