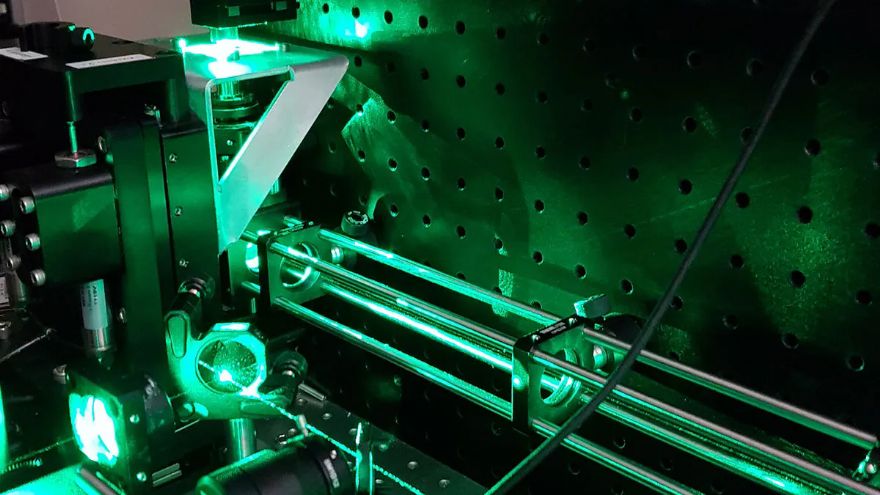
Highly innovative, thin, and flexible optical devices for the future diagnosis and treatment of a range of conditions have already been demonstrated, but such devices require complex systems of micro-optic lenses, mirrors, and prisms— like a microscope — at their end; and while these systems (distal-end-microsystems) have the potential to transform the delivery of procedures like key-hole surgeries and biopsies, manufacturing the complex end of each device has, up to now, taken hours per device, increasing costs, and limiting up-take.
A new ‘laser beam shaping’ technique developed by
Heriot-Watt University has dramatically reduced manufacturing time for the required optical systems — from hours to just a few minutes (the findings were published in the peer-reviewed journal
Optics Express). The team also developed new micro-optic systems for applications in minimally invasive precision microsurgery using ultra-fast laser pulses delivered by specialist hollow core fibres developed by the
University of Bath.
Professor Robert Thomson, who led the project team from Heriot-Watt University, said: “Medical device technologies are vital for the detection and treatment of a huge number of diseases and healthcare challenges. Increasingly, micro-devices are being developed for minimally invasive measurement and therapy, but up to now they have been very expensive to produce.
“Coming up with a medical device innovation is exciting but if it can’t be made commercially, it won’t be used in hospitals and clinics. To encourage the take-up of ‘state of the art’ devices, it is vital to provide low-cost and highly repeatable manufacturing solutions.
“We have achieved a major manufacturing advance using laser beam shaping techniques. This gives us control of the shape of the focal volume, and therefore more efficient use of the available laser pulse energy during manufacture. We have overcome a major drawback of using ultra-fast laser inscription techniques for manufacturing distal-end-microsystems for fibre-optic medical instruments.”