Mr Palmer, owner and managing director of Repro Engineering, in front of the latest Miyano to be installed in Waterlooville — a BNJ-51SYIt is often said that a sub-contractor does not know what type of work will be coming through the door the next day, so needs versatile machine tools to be able to produce a wide variety of components.
The diversity of work is particularly large in the case of Hampshire-based contract machinists
Repro Engineering, 80% of whose turnover derives from turn-milling, components being mainly in the diameter range 19 to 51mm. Throughput in a variety of different plastics typically accounts for one-third of the total, but at times is as much as 50%, the remainder being mainly mild and stainless steels.
The mainstay for production of a large proportion of the turned parts are CNC turning centres from
Citizen Machinery, both Miyano fixed-head lathes and Cincom sliding-head models. The first Miyano to be installed was a BND42S twin-spindle lathe with live tooling.
It arrived in 1997 and departed just three years ago after 23 years of service, having produced more than two million components, most in one hit and a large proportion in lights-out operation. The second Miyano, a BND51S, was bought in 1998 and sold in mid-2022 after an even longer period on the shopfloor.
Repro Engineering’s owner and managing director Richard Palmer said: “We have a policy of regularly reviewing our capacity and keeping plant up to date. In the case of the Miyanos, however, earlier exchange simply was not necessary, as the machines continued to hold tolerance. Not having to spend money on replacing them earlier helps to keep costs down for our customers and makes us more competitive.”
Allows complex machining operations The replacement for the BND51S was a more capable BNJ-51SY, which arrived in May 2022. Featuring two turrets and Y-axis movement of the main turret, the lathe allows complex machining operations to be carried out at the main and sub spindles simultaneously. The turning centre also sports many more tool positions than the older model, so fewer tool changes are needed. It is normally possible to put the next part up without any cutter exchange at all.
Nine Miyano machines have been purchased over the years and many have been replaced by newer models. The sub-contractor’s current tally of bar-fed lathes of this make is five, accounting for nearly half of its fixed-head lathes. Three of the Miyanos have a Y-axis function and all are fitted with short bar magazines for feeding 1m stock up to 51mm diameter. Additionally, the sub-contractor operates a Miyano LZ-01R chucker for billet work, especially components that need hard turning.
Regarding Repro Engineering’s sliding-head capacity, the sub-contractor operates three Cincom lathes capable of machining parts from up to 32mm diameter bar. There are also five smaller capacity sliders of a different make on site. Impressed with the quality and longevity of the Miyano machines, Mr Palmer decided to approach Citizen for larger Swiss-type lathes capable of producing bigger diameter, often shaft-type components. He purchased a Cincom A32-VII in 2009, followed by a more highly specified M32-VIII with a B-axis in 2013, and another A32-VII two years later.
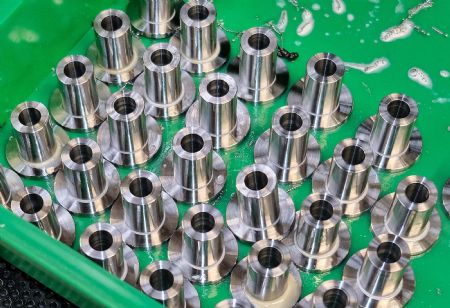
All were bought before the Japanese lathe manufacturer had introduced its novel LFV (low frequency vibration) chip breaking software, otherwise Mr Palmer would definitely have specified it. The programmable function, which breaks stringy swarf into short chips, is ideal for turning plastics and stainless steel efficiently. Instead, Mr Palmer relies conventionally on high-pressure oil to promote chip breaking and prevent bird’s nesting.
Extensive use is made of Citizen’s Alkart Wizard CNC programming software to prepare programs for both the Miyano and Cincom lathes. It guides operators through the creation of part programs, calling on a built-in code library and reference diagrams to optimise machining of different materials. It cuts down the amount of time spent typing in G and M codes, or consulting manuals, and validates the program before it is run.
Repro Engineering also operates four machining centres, which generate the other 20% of turnover. One machine is part of an automated cell with robot loading and some are equipped with a fourth CNC axis, but for indexing, not turning. It means that all components produced that require both turning and milling go onto the lathes.
The ideal platform for unattended productionMr Palmer points out that, in this respect, a twin-spindle bar-fed turning centre is the ideal platform for unattended production in one hit of complex components, even prismatic parts requiring all six sides to be accessed. Cycle times tend to be longer on mill-turn centres, which in any case normally require an operator to be present. He does not hesitate to put onto his lathes parts that require no turning operations at all except parting-off.
Mr Palmer concluded: “All Citizen lathes are real workhorses. They are robust, compact and some have hand-scraped guideways, which leads to excellent machining quality. The Miyanos in particular are so well built, they are almost over-engineered — they just keep going and going, maintaining their accuracy and repeatability for decades. Consequently, for machining parts up to 51mm, they are our preferred lathes. Likewise, for turning and milling in sliding-head mode, we have standardised on Cincom when machining parts from larger diameter bars up to 32mm.”
Founded by Mr Palmer’s father Davin in 1967 and now operating 24/7 from a 12,000ft
2 premises in Waterlooville, Repro Engineering produces batch sizes typically in the range 1,000 to 50,000, although prototype batches down to 100 are not infrequent. Some parts are machined to very tight tolerances down to 10µm total.
Customers are mainly in the motorsport, defence, sports and leisure, electronics, medical and fluid power sectors and many take advantage of the sub-contractor’s consignment stocking service. The company is accredited to ISO9001:2015 and AS9100 Rev D, ensuring high-quality standards. In addition, it is registered on the International Aerospace Quality Group’s OASIS (Online Aerospace Supplier Information System) database.